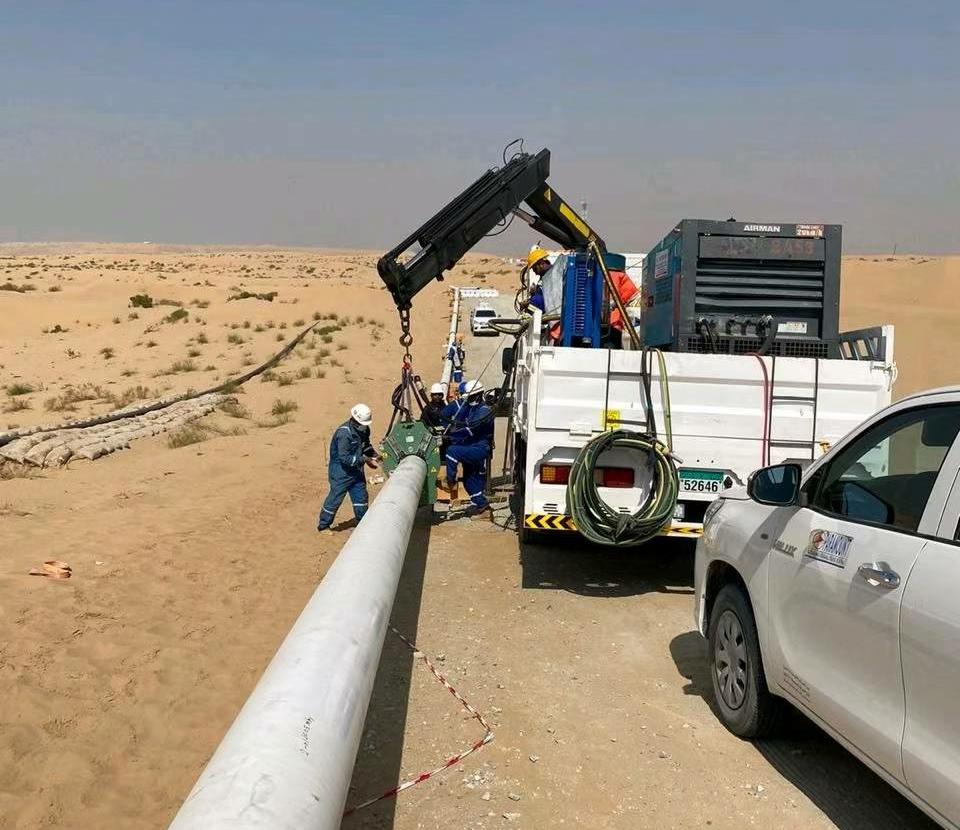
Project introduction: The long-distance oil pipeline system established in the northern part of Iraq has various auxiliary supporting projects, and the annual oil transportation volume of a single pipeline exceeds several million tons |
Location Iraq Product Value US$914,390.00 Product Details Seamless pipe,API 5L X80, Elbow Contract No. Nansteel202210384392 Date 10.2022 |
How are long-distance oil and gas pipelines built? 01 handover pile The design representative hands over the design control (corner) piles to the construction unit on site and checks the pile number, mileage, elevation, and corner angle. 02 Measurement and setting out Based on the line plan, longitudinal section, line control piles and other design data, surveyors use special instruments to determine the centerline position of the pipeline installation along the line and draw the boundaries of the construction zone. 03 Construction work belt cleaning Use bulldozers and other construction equipment to level the work zone and remove obstacles such as trees in the work zone. The width of the pipeline construction operation belt is generally between 12 and 32 meters. For non-mechanized construction areas in mountainous areas, the width of the operation belt can be appropriately reduced according to the terrain conditions. 04 Steel pipe transportation Transport steel pipes(such as seamless pipe) from the pipe factory or train transfer station to the construction site by road. Special transportation vehicles are required for transporting steel pipes. Special pipe lifting belts are also required for loading and unloading of steel pipes. There must be space between the steel pipe and the frame and between the two steel pipes. Separate them with soft materials such as rubber sheets. 05 Pipe trench excavation Long-distance oil and gas pipelines are generally laid underground, which requires trench excavation. The depth of the trench is generally between 3-5 meters, and the width of the trench bottom is generally less than 3 meters. When pipelines cross rivers, methods such as large-scale excavation, directional drilling, shield tunneling, and crossing are often used. The specific laying method needs to be comprehensively considered based on the size of the river and the geological conditions. 06 Pipe routing Place the steel pipes in the work zone at the construction location. Generally, the steel pipes are required to be connected end to end and distributed in a zigzag shape. The steel pipes also need to be placed on flexible objects and must not come into contact with hard objects such as stones to avoid damage to the pipes. 07 Steel pipe assembly, welding and weld inspection This is the most important link in the construction process of long-distance pipelines. The alignment process is the preparation for the welding process. It is necessary to align the nozzles of the two pipelines and then clamp the two pipelines together with a pairing tool. After the assembly process is completed, the welding process can be carried out! After welding, the welds need to be inspected to ensure welding quality. At present, welding processes mainly include manual semi-automatic welding and fully automatic welding. New pipelines such as the China-Russia East Line focus on promoting the application of fully automatic welding processes. 08 Pipe repair and repair After the pipeline welding is completed, the damage to the anti-corrosion layer of the pipeline interface needs to be repaired. After the operation is completed, a comprehensive quality inspection is required to ensure that the pipeline can operate safely and smoothly after being put into operation. 09 Pipe trench After the pipeline has completed welding, non-destructive testing and repair work, recheck the depth of the pipeline trench to ensure compliance with specifications, remove foreign matter that damages the anti-corrosion layer in the pipeline trench, and then use special pipe lifting equipment to lower the welded pipeline to the The bottom of the trench. 10 Pipe Backfill This is the last process to ensure the burial depth of long-distance pipelines, and is also an important factor in ensuring pipeline installation quality and operational safety. The trench backfilling work is generally completed within 10 days after the pipeline is lowered into the trench. During the backfilling process, communication optical cables were laid in the trenches to serve as a "highway" for remote monitoring and information transmission of smart pipelines. 11 Pipeline cleaning, diameter measurement and pressure test Use a cleaning ball (device) to clean the pipe and remove debris in the pipeline; use a caliper plate to measure the diameter. After the caliper plate passes through the pipe section, if there is no deformation or wrinkles, it is qualified; use water (gas) medium to pour into the pipeline, And increase the injection pressure for testing to ensure that the pipeline can withstand sufficient pressure. 12 Landscape restoration After the trench backfilling process is completed, the construction materials and debris in the work zone will be cleaned up and restored according to the pre-construction landform. 13 Project completion acceptance After the construction phase of the picture is completed, the project completion acceptance can be carried out after the trial operation and production, handover acceptance, special acceptance and other processes have been successfully completed. |