To quickly identify the quality of cold-drawn seamless steel pipes, you can uate them through the following key indicators and inspection methods. These methods can help you preliminarily determine the quality of steel pipes during the procurement or acceptance process to avoid quality problems affecting subsequent use or installation.
Appearance inspection
Appearance is an important intuitive basis for judging the quality of cold-drawn seamless steel pipes. Through visual inspection, the surface quality of the steel pipe can be roughly judged.
Main checkpoints:
Surface finish: The surface of the cold-drawn steel pipe should be smooth, without obvious scratches, dents, pores and other defects. If the surface is rough, it may be due to improper cold drawing process or pickling.
Oxide scale: Oxide scale is a layer of hard shell that may exist on the surface of cold-drawn steel pipes. If the oxide scale is not removed thoroughly, it will affect the corrosion resistance and appearance of the steel pipe. High-quality cold-drawn steel pipes should have no obvious oxide scale or rust on the surface.
Cracks and holes: Check whether the steel pipe has defects such as cracks, holes, bubbles, etc., especially at the welding joints and pipe ends.
Straightness and bending: Observe whether the steel pipe has defects such as bending and corrugation. Excellent cold-drawn seamless steel pipe should maintain straightness to avoid affecting installation and load-bearing capacity.
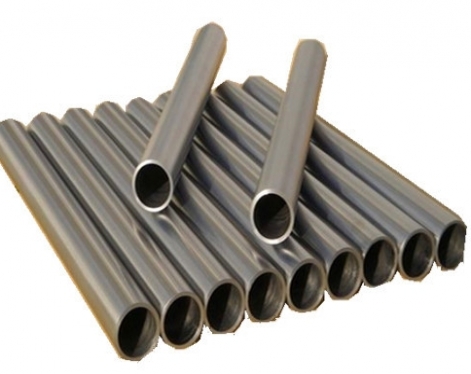
Dimensional measurement
The precision of cold-drawn seamless steel pipes is high, and dimensional accuracy is an important criterion for uating their quality.
Main checkpoints:
Outer diameter and wall thickness: Use calipers, outside diameter gauges and other tools to measure the outer diameter and wall thickness of the steel pipe to check whether it meets the design requirements. Cold-drawn steel pipes usually have smaller dimensional tolerances, and any deviations should be strictly controlled.
Length tolerance: Check whether the length of the steel pipe meets the standard, especially in applications where long dimensions are required, the length error should not exceed the specified tolerance range.
Mechanical properties test
The mechanical properties of cold-drawn seamless steel pipes are crucial to their load-bearing capacity during use.
Main checkpoints:
Tensile strength and yield strength: The tensile strength and yield strength of the steel pipe are tested through tensile tests to ensure that it can meet the load-bearing requirements in the application. For cold-drawn steel pipes, the tensile strength and yield strength are usually higher, which is suitable for high-pressure or high-strength applications.
Elongation: Elongation testing can determine the plasticity of the steel pipe. High-quality cold-drawn steel pipes should have a higher elongation, indicating that they have better toughness.
Hardness test: The hardness of the steel pipe is tested by a hardness tester. Too high hardness may cause the steel pipe to become more brittle, while too low hardness may cause the pipe to be insufficiently strong. A reasonable hardness range indicates that the steel pipe has a good balance of strength and toughness.
Nondestructive Testing
Nondestructive testing is an effective means to verify the internal quality of cold-drawn steel tubes, especially for detecting defects that cannot be directly observed on the surface.
Commonly used non-destructive testing methods:
Ultrasonic testing (UT): It can detect whether there are cracks, pores, inclusions and other defects inside the steel pipe. Ultrasonic testing is the most commonly used non-destructive testing method and is suitable for detecting internal defects of steel pipes.
X-ray testing (RT): Suitable for detecting larger or deep defects inside the steel pipe, such as the quality of the welded joints. X-ray testing conducts a detailed scan of the internal quality of the cold-drawn steel pipe.
Magnetic particle testing (MT): mainly used to detect cracks on the surface or near the surface of steel pipes, suitable for application scenarios with high surface quality requirements.
Penetrant testing (PT): used to check surface cracks, pores and other defects, especially for steel pipes with high requirements for surface smoothness.
Chemical composition analysis
The analysis of chemical composition can ensure that the material of the cold-drawn steel pipe meets the standard requirements, thereby ensuring its mechanical properties and corrosion resistance.
Inspection content:
Steel alloy composition: The chemical composition of the steel pipe can be confirmed by chemical analysis (such as spectral analysis) to ensure that it meets relevant standards or customer requirements.
Carbon content: Carbon content directly affects the hardness and strength of the steel pipe. High carbon content steel pipe may have better strength, but may sacrifice toughness.
Other alloying elements: Alloying elements such as manganese, silicon, chromium, molybdenum, etc. will also affect the corrosion resistance, hardness and strength of the steel pipe and must meet specific requirements.
Quality certification provided by the supplier
Qualified seamless steel pipe manufacturers usually provide corresponding quality certificates to prove that the cold-drawn seamless steel pipes they produce meet the relevant standards and customer technical requirements. The relevant quality certificates include:
Material certificate: ensure that the chemical composition of the steel pipe meets the standards.
Inspection report: Contains test results of mechanical properties such as tensile strength, yield strength, and elongation.
Nondestructive testing report: Inspection report on surface and internal defects.
Read more: Key Points of Machining Cold Drawn Seamless Pipes
Appearance inspection
Appearance is an important intuitive basis for judging the quality of cold-drawn seamless steel pipes. Through visual inspection, the surface quality of the steel pipe can be roughly judged.
Main checkpoints:
Surface finish: The surface of the cold-drawn steel pipe should be smooth, without obvious scratches, dents, pores and other defects. If the surface is rough, it may be due to improper cold drawing process or pickling.
Oxide scale: Oxide scale is a layer of hard shell that may exist on the surface of cold-drawn steel pipes. If the oxide scale is not removed thoroughly, it will affect the corrosion resistance and appearance of the steel pipe. High-quality cold-drawn steel pipes should have no obvious oxide scale or rust on the surface.
Cracks and holes: Check whether the steel pipe has defects such as cracks, holes, bubbles, etc., especially at the welding joints and pipe ends.
Straightness and bending: Observe whether the steel pipe has defects such as bending and corrugation. Excellent cold-drawn seamless steel pipe should maintain straightness to avoid affecting installation and load-bearing capacity.
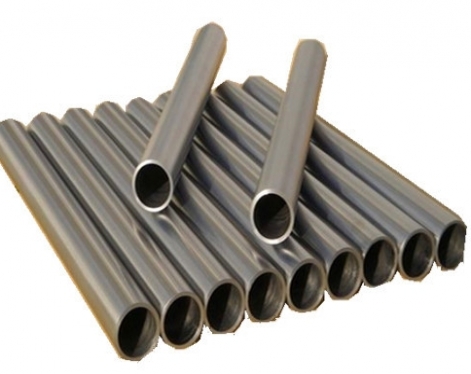
Dimensional measurement
The precision of cold-drawn seamless steel pipes is high, and dimensional accuracy is an important criterion for uating their quality.
Main checkpoints:
Outer diameter and wall thickness: Use calipers, outside diameter gauges and other tools to measure the outer diameter and wall thickness of the steel pipe to check whether it meets the design requirements. Cold-drawn steel pipes usually have smaller dimensional tolerances, and any deviations should be strictly controlled.
Length tolerance: Check whether the length of the steel pipe meets the standard, especially in applications where long dimensions are required, the length error should not exceed the specified tolerance range.
Mechanical properties test
The mechanical properties of cold-drawn seamless steel pipes are crucial to their load-bearing capacity during use.
Main checkpoints:
Tensile strength and yield strength: The tensile strength and yield strength of the steel pipe are tested through tensile tests to ensure that it can meet the load-bearing requirements in the application. For cold-drawn steel pipes, the tensile strength and yield strength are usually higher, which is suitable for high-pressure or high-strength applications.
Elongation: Elongation testing can determine the plasticity of the steel pipe. High-quality cold-drawn steel pipes should have a higher elongation, indicating that they have better toughness.
Hardness test: The hardness of the steel pipe is tested by a hardness tester. Too high hardness may cause the steel pipe to become more brittle, while too low hardness may cause the pipe to be insufficiently strong. A reasonable hardness range indicates that the steel pipe has a good balance of strength and toughness.
Nondestructive Testing
Nondestructive testing is an effective means to verify the internal quality of cold-drawn steel tubes, especially for detecting defects that cannot be directly observed on the surface.
Commonly used non-destructive testing methods:
Ultrasonic testing (UT): It can detect whether there are cracks, pores, inclusions and other defects inside the steel pipe. Ultrasonic testing is the most commonly used non-destructive testing method and is suitable for detecting internal defects of steel pipes.
X-ray testing (RT): Suitable for detecting larger or deep defects inside the steel pipe, such as the quality of the welded joints. X-ray testing conducts a detailed scan of the internal quality of the cold-drawn steel pipe.
Magnetic particle testing (MT): mainly used to detect cracks on the surface or near the surface of steel pipes, suitable for application scenarios with high surface quality requirements.
Penetrant testing (PT): used to check surface cracks, pores and other defects, especially for steel pipes with high requirements for surface smoothness.
Chemical composition analysis
The analysis of chemical composition can ensure that the material of the cold-drawn steel pipe meets the standard requirements, thereby ensuring its mechanical properties and corrosion resistance.
Inspection content:
Steel alloy composition: The chemical composition of the steel pipe can be confirmed by chemical analysis (such as spectral analysis) to ensure that it meets relevant standards or customer requirements.
Carbon content: Carbon content directly affects the hardness and strength of the steel pipe. High carbon content steel pipe may have better strength, but may sacrifice toughness.
Other alloying elements: Alloying elements such as manganese, silicon, chromium, molybdenum, etc. will also affect the corrosion resistance, hardness and strength of the steel pipe and must meet specific requirements.
Quality certification provided by the supplier
Qualified seamless steel pipe manufacturers usually provide corresponding quality certificates to prove that the cold-drawn seamless steel pipes they produce meet the relevant standards and customer technical requirements. The relevant quality certificates include:
Material certificate: ensure that the chemical composition of the steel pipe meets the standards.
Inspection report: Contains test results of mechanical properties such as tensile strength, yield strength, and elongation.
Nondestructive testing report: Inspection report on surface and internal defects.
Read more: Key Points of Machining Cold Drawn Seamless Pipes