1. What is welded steel tube?
Welded steel pipe is a metal pipe made by rolling steel plates and welding them on a mold of a specific diameter. It is commonly used in industries such as construction, machinery manufacturing, and bridge engineering. Its advantages are high production efficiency, and it is quite rigid and pressure-resistant in larger sizes. Welded pipes can be divided into carbon steel pipes and stainless steel pipes.2. Connection methods of welded steel tubing
(1)Threaded connection
Threaded connection is a connection method that connects pipes to pipes, pipes, and valves through internal and external threads. This method is often used to connect some threaded equipment, accessories, and situations where fire is not allowed when disassembly is frequent.① Galvanized welded steel pipes for transporting low-pressure fluids
Generally, the nominal diameter is required to be below 150mm, and the working pressure is below 1.6MPa.
②Water supply pipe
The working pressure does not exceed 1.6MPa, and the maximum nominal diameter is 150mm.
③Hot water pipes
The working pressure does not exceed 0.2MPa, and the maximum nominal diameter is 50mm.
④Thin-walled stainless steel welded pipe
Suitable for connecting pipe sections from DN65 to DN100.
When connecting welded pipes with threads, appropriate packing should be placed between the external thread of the pipe and the internal thread of the pipe opening or valve. The main functions of the packing are: sealing, protecting the pipe opening, and facilitating disassembly. Threaded connection features: easy to install, disassemble, easy to adjust, simple construction, and land ow pressure resistance. The main installation procedures include; pipe breaking, threading, assembling pipe fittings, and pipe section straightening.
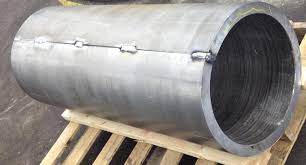
(2)Flange connection
Flange connections are often used when connecting temporary drainage and irrigation pipelines, pipe-fitting combinations of pump stations, welded steel pipes, valves, and accessories.Flanges are classified according to material: cast iron flange, steel pipe flange, plastic flange, non-ferrous metal flange, glass flange, and fiberglass flange.The flange is selected according to the nature, pressure, and temperature of the medium; the nominal pressure needs to meet the design requirements; where the welded pipe section is connected to the welded pipe section using a flange plate or the pipe section is connected to a flange valve, the standard method must be selected according to the design requirements and working pressure Lanpan. The flange of the equipment is generally concave or grooved, and the selected flange should be convex or tenon. Thin-walled stainless steel welded pipes are suitable for pipe sections above DN100.
The main features of flange connections are easy disassembly, high strength, good sealing performance, and the ability to withstand large pressures. When installing the flange, the two flanges must be kept parallel, and the sealing surface of the flange must not be damaged and must be cleaned. The gasket used for the flange must be selected according to the design requirements.
(3)Welding
Welding connection is a relatively common method of connecting welded steel pipes. Generally, the steel pipe interface and welding rod are heated, and then the weldments are connected and fixed together. This connection method has the advantages of firm welding, good sealing, good durability, low cost, and does not require frequent maintenance.The main welding methods of steel pipes include gas welding, arc welding (automatic spot welding, manual electric welding), resistance welding, manual arc welding, manual argon arc welding, submerged arc automatic welding, and contact welding.
For example, the common ERW pipe is resistance welding. It refers to the method of using the resistance heat generated by current passing through the weldment and the contact as a heat source to locally heat the weldment and pressurize it at the same time. When welding, there is no need for filler metal, high productivity, small deformation of the weldment, and easy automation.
(4) Groove clamp connection
The grooved clamp connection is a new type of welded pipe connection method with many advantages. The principle is to use the cooperation of the clamp and the groove to compress the pipe through bolt tightening to achieve a sealed connection. Grooved clamp connections usually include clamps, slots, seals, flanges and other components. The clamp is usually made of gray cast iron, ductile iron or stainless steel, while the clamping groove and sealing plate are mostly round or square, and the flange is used to withstand the pressure in the welded pipe.The grooved clamp connection has the advantages of fast installation, simple operation, and reliable sealing. It is suitable for large-diameter, high-pressure, high-temperature, and corrosion-resistant pipeline systems, and has a high error tolerance during installation. In addition, the grooved clamp connection does not require precision machining, which saves costs and reduces the engineering cost of the entire pipeline system. It is also easy to repair and replace, reducing maintenance difficulty and cost.
However, grooved clamp connections also have some limitations. For example, it is not suitable for pipeline systems under special working conditions such as high pressure, high temperature, corrosion resistance, etc., and the sealing performance may be poor. Therefore, when selecting a grooved clamp connection, it needs to be decided based on specific engineering needs and environmental conditions.