Large-diameter straight seam steel pipe is a welded steel pipe whose weld seam is parallel to the longitudinal direction of the steel pipe. It is usually divided into metric electric welded steel pipe, electric welded thin-walled pipe, transformer cooling oil pipe and so on. The production process of large diameter straight seam steel pipe is simple, the production rate is good, the cost is not bad, and the development is not slow. The outer diameter of large-diameter straight seam steel pipes can reach more than 500mm, the maximum diameter of double welds can reach 2020mm, and the maximum diameter of single welds can reach 1220mm.
The general large-diameter straight seam steel pipe submerged arc welded pipe manufacturing method is to bend a single steel plate according to the radius of curvature and then form it. The single steel plate is used as a raw material, and the welding is performed internally and then externally. This method is not easy to determine the small and medium diameter straight seam arc welded pipe, there are many pores and inclusions, and the price of the steel plate is higher than that of the steel strip, which increases the cost. Therefore the existing LSAW pipe manufacturing method is not suitable for producing medium and small diameter LSAW pipes. When using JCOE or spiral submerged arc welding production process to produce medium and small diameter submerged arc welded pipes, the production rate is relatively low and the cost is relatively good.
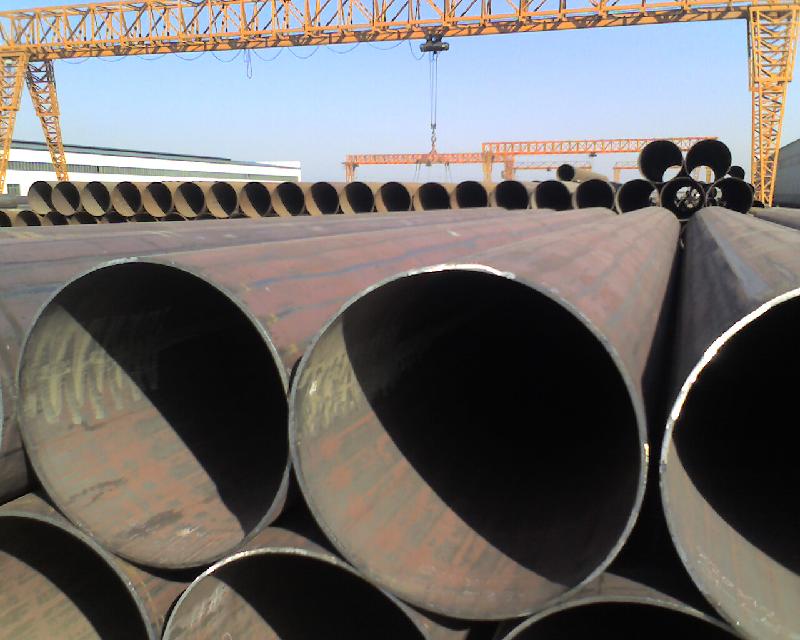
Appearance requirements for large diameter straight seam steel pipes:
1. Cracks, incomplete fusion, pores, slag inclusions, and splashes are not allowed.
2. The weld surface of pipes with a design temperature lower than -29 degrees, stainless steel and alloy steel pipes with a large tendency to harden should not have undercuts. The undercut of welded seam of pipes made of other materials shall be greater than 0.5mm, the length of continuous undercut shall not exceed 100mm, and the total length of undercut on both sides of the weld shall not exceed 10% of the total length of the weld.
3. The surface of the weld seam cannot be lower than the surface of the pipe. Weld seam reinforcement, and not greater than 3mm, (the maximum width of the groove after the welding joint is assembled).
4. The wrong side of the welded joint should not be greater than 10% of the wall thickness, and not greater than 2mm.
The general large-diameter straight seam steel pipe submerged arc welded pipe manufacturing method is to bend a single steel plate according to the radius of curvature and then form it. The single steel plate is used as a raw material, and the welding is performed internally and then externally. This method is not easy to determine the small and medium diameter straight seam arc welded pipe, there are many pores and inclusions, and the price of the steel plate is higher than that of the steel strip, which increases the cost. Therefore the existing LSAW pipe manufacturing method is not suitable for producing medium and small diameter LSAW pipes. When using JCOE or spiral submerged arc welding production process to produce medium and small diameter submerged arc welded pipes, the production rate is relatively low and the cost is relatively good.
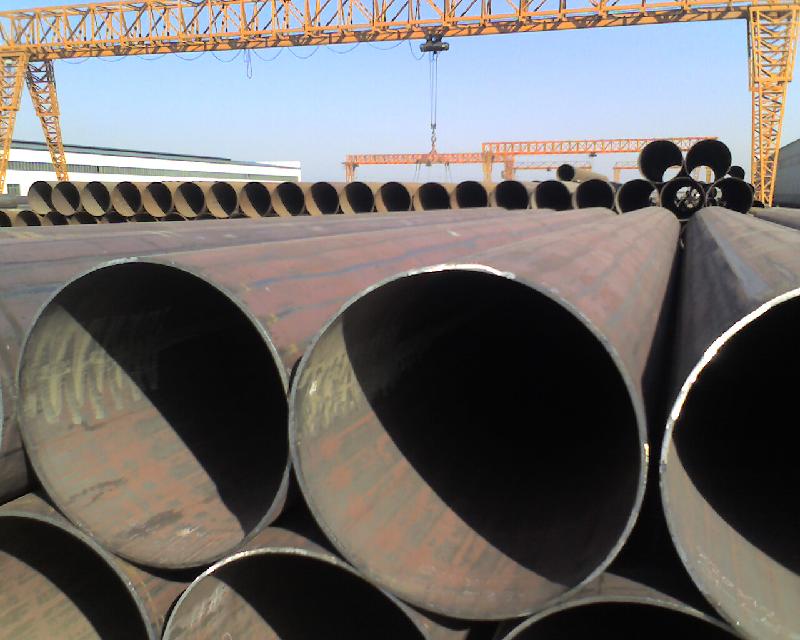
Appearance requirements for large diameter straight seam steel pipes:
1. Cracks, incomplete fusion, pores, slag inclusions, and splashes are not allowed.
2. The weld surface of pipes with a design temperature lower than -29 degrees, stainless steel and alloy steel pipes with a large tendency to harden should not have undercuts. The undercut of welded seam of pipes made of other materials shall be greater than 0.5mm, the length of continuous undercut shall not exceed 100mm, and the total length of undercut on both sides of the weld shall not exceed 10% of the total length of the weld.
3. The surface of the weld seam cannot be lower than the surface of the pipe. Weld seam reinforcement, and not greater than 3mm, (the maximum width of the groove after the welding joint is assembled).
4. The wrong side of the welded joint should not be greater than 10% of the wall thickness, and not greater than 2mm.