Casing couplings and tubing couplings are essential components in oil and gas well construction and production operations, playing critical roles in the assembly of continuous casing and tubing strings. Both types of couplings are designed to provide secure connections between pipe segments, enabling the extraction of hydrocarbons from subsurface reservoirs. While they share similarities in their threaded connections and sealing mechanisms, casing couplings and tubing couplings have distinct features, applications, and design considerations tailored to their specific functions in the well environment.
1.Casing Couplings
Casing couplings are primarily used to connect two joints of casing, which are large-diameter steel pipes installed during the drilling process to line the wellbore and protect the surrounding geological formations. The primary function of casing couplings is to create a threaded connection between adjacent casing segments, ensuring the integrity and continuity of the casing string. These couplings are subjected to high axial loads and external pressures, making their design and material selection critical for withstanding challenging downhole conditions.
(1)Design and Construction
Casing couplings are typically constructed from high-strength steel and are threaded on both ends to facilitate the connection with adjacent casing segments. The threads are precision-machined to ensure a tight seal and prevent leaks under the high-pressure conditions encountered in oil and gas wells. The design of casing couplings also takes into account factors such as corrosion resistance, mechanical strength, and compatibility with downhole environments.
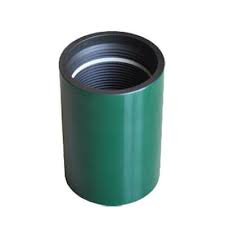
(2)Materials and Specifications
The materials used in casing couplings are carefully selected based on factors such as mechanical strength, corrosion resistance, and compatibility with downhole environments. Common materials include carbon steel, alloy steel, and stainless steel, with specific grades designed to meet performance requirements in corrosive or high-temperature reservoirs. Additionally, casing couplings must conform to industry standards and regulations, such as those set by the American Petroleum Institute (API), to ensure consistency and reliability in their performance.
(3)Applications
Casing couplings are employed in various well construction and completion activities, including drilling, cementing, and production operations. They are critical components in creating a continuous casing string that protects the wellbore and facilitates efficient reservoir production. Casing couplings are designed to withstand the forces exerted during installation, cementing, and subsequent production, making their structural integrity and performance vital to the overall success and safety of the well.
(4)Considerations
When selecting casing couplings for a particular well application, factors such as casing size, weight, grade, and thread type must be carefully considered to ensure proper compatibility and performance. Additionally, environmental factors, such as the presence of corrosive fluids or high-pressure conditions, influence the choice of materials and coatings to enhance the longevity and reliability of casing couplings in challenging downhole environments.
2.Tubing Couplings
On the other hand,tubing couplings are used to join sections of tubing, which are smaller-diameter pipes that convey fluids from the reservoir to the surface. Tubing serves as a conduit for the production of oil, gas, and other well fluids, and tubing couplings play a pivotal role in maintaining the integrity of the tubing string while providing a means for efficient fluid production and well intervention activities.
(1)Design and Construction
Similar to casing couplings, tubing couplings are designed with threaded connections to securely link individual tubing segments together. Their construction and sealing mechanisms are specifically engineered to withstand internal pressure, tensile loads, and bending forces associated with tubing strings in producing wells. Tubing couplings are available in various sizes and configurations to accommodate the diverse range of tubing dimensions and operational requirements in oil and gas wells.
(2)Materials and Specifications
The materials used in tubing couplings are chosen based on similar criteria as casing couplings, with an emphasis on mechanical strength, corrosion resistance, and compatibility with downhole conditions. Depending on the specific well environment and production characteristics, tubing couplings may be manufactured from carbon steel, alloy steel, or corrosion-resistant alloys to ensure reliable performance and longevity in challenging operating conditions.
(3)Applications
Tubing couplings are integral components in the completion and production phases of oil and gas wells. They provide the necessary connection points for assembling tubing strings that transport reservoir fluids to the surface, where they can be processed and transported for further refining. Tubing couplings must effectively seal the tubing joints to prevent leakage and maintain well productivity while accommodating dynamic forces and movements experienced during production and well interventions.
(4)Considerations
Selecting the appropriate tubing couplings involves considering factors such as tubing size, weight, grade, and connection type to ensure compatibility and performance within the well environment. Additionally, considerations relating to fluid properties, well temperature, and the potential for corrosive elements influence the selection of materials and coatings to enhance the reliability and longevity of tubing couplings in demanding downhole applications.
1.Casing Couplings
Casing couplings are primarily used to connect two joints of casing, which are large-diameter steel pipes installed during the drilling process to line the wellbore and protect the surrounding geological formations. The primary function of casing couplings is to create a threaded connection between adjacent casing segments, ensuring the integrity and continuity of the casing string. These couplings are subjected to high axial loads and external pressures, making their design and material selection critical for withstanding challenging downhole conditions.
(1)Design and Construction
Casing couplings are typically constructed from high-strength steel and are threaded on both ends to facilitate the connection with adjacent casing segments. The threads are precision-machined to ensure a tight seal and prevent leaks under the high-pressure conditions encountered in oil and gas wells. The design of casing couplings also takes into account factors such as corrosion resistance, mechanical strength, and compatibility with downhole environments.
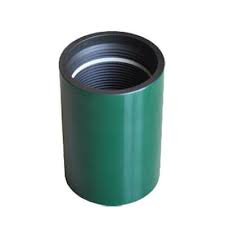
(2)Materials and Specifications
The materials used in casing couplings are carefully selected based on factors such as mechanical strength, corrosion resistance, and compatibility with downhole environments. Common materials include carbon steel, alloy steel, and stainless steel, with specific grades designed to meet performance requirements in corrosive or high-temperature reservoirs. Additionally, casing couplings must conform to industry standards and regulations, such as those set by the American Petroleum Institute (API), to ensure consistency and reliability in their performance.
(3)Applications
Casing couplings are employed in various well construction and completion activities, including drilling, cementing, and production operations. They are critical components in creating a continuous casing string that protects the wellbore and facilitates efficient reservoir production. Casing couplings are designed to withstand the forces exerted during installation, cementing, and subsequent production, making their structural integrity and performance vital to the overall success and safety of the well.
(4)Considerations
When selecting casing couplings for a particular well application, factors such as casing size, weight, grade, and thread type must be carefully considered to ensure proper compatibility and performance. Additionally, environmental factors, such as the presence of corrosive fluids or high-pressure conditions, influence the choice of materials and coatings to enhance the longevity and reliability of casing couplings in challenging downhole environments.
2.Tubing Couplings
On the other hand,tubing couplings are used to join sections of tubing, which are smaller-diameter pipes that convey fluids from the reservoir to the surface. Tubing serves as a conduit for the production of oil, gas, and other well fluids, and tubing couplings play a pivotal role in maintaining the integrity of the tubing string while providing a means for efficient fluid production and well intervention activities.
(1)Design and Construction
Similar to casing couplings, tubing couplings are designed with threaded connections to securely link individual tubing segments together. Their construction and sealing mechanisms are specifically engineered to withstand internal pressure, tensile loads, and bending forces associated with tubing strings in producing wells. Tubing couplings are available in various sizes and configurations to accommodate the diverse range of tubing dimensions and operational requirements in oil and gas wells.
(2)Materials and Specifications
The materials used in tubing couplings are chosen based on similar criteria as casing couplings, with an emphasis on mechanical strength, corrosion resistance, and compatibility with downhole conditions. Depending on the specific well environment and production characteristics, tubing couplings may be manufactured from carbon steel, alloy steel, or corrosion-resistant alloys to ensure reliable performance and longevity in challenging operating conditions.
(3)Applications
Tubing couplings are integral components in the completion and production phases of oil and gas wells. They provide the necessary connection points for assembling tubing strings that transport reservoir fluids to the surface, where they can be processed and transported for further refining. Tubing couplings must effectively seal the tubing joints to prevent leakage and maintain well productivity while accommodating dynamic forces and movements experienced during production and well interventions.
(4)Considerations
Selecting the appropriate tubing couplings involves considering factors such as tubing size, weight, grade, and connection type to ensure compatibility and performance within the well environment. Additionally, considerations relating to fluid properties, well temperature, and the potential for corrosive elements influence the selection of materials and coatings to enhance the reliability and longevity of tubing couplings in demanding downhole applications.