LSAW steel pipe is a welded pipe produced by pressing (rolling) the steel plate into a tube blank in a mold or a forming machine, and using a double-sided submerged arc welding method and expanding the diameter. The finished product has a wide range of specifications, good toughness, plasticity, uniformity and compactness of the weld, and has the advantages of large pipe diameter, pipe wall thickness, high pressure resistance, low temperature resistance and strong corrosion resistance.
LSAW steel pipe expansion is a pressure processing process that uses hydraulic or mechanical means to apply force from the inner wall of the steel pipe to expand the steel pipe radially outward. The mechanical method is simpler and more efficient than the hydraulic method, and the steel pipe machining is more accurate under the condition of high precision.The expansion process of LSAW steel pipe is divided into mechanical expansion and hydraulic expansion.
The purpose of the expansion process
1) Correct the deformation of the steel pipe caused by the thermal effect of welding, so that the geometric dimensions of the steel pipe, such as pipe diameter, roundness, straightness, etc., can reach the required accuracy
Note: The diameter accuracy and geometric dimensions of steel pipes are one of the important indicators of quality control in the production process of welded pipes.Whether it is a pipeline steel pipe, or a steel pipe pile and structural steel pipe, it is formed by butt welding of multiple welded pipes. Therefore, there are strict technical requirements and standards for its pipe diameter tolerance, ovality and straightness.
(2) Eliminate the Baushinger Ef-fect produced by forming and compression during the pipe making process, and increase the strength of the steel pipe by 0~15% depending on the steel type.
(3) Eliminate the residual stress of the weld seam caused by the welding process, and avoid hydrogen embrittlement caused by hydrogen in the oil or natural gas in the area where the stress of the weld seam is concentrated and cause cracks.
The characteristics of mechanical expansion and hydraulic expansion
The expansion methods of LSAW steel pipes are divided into hydraulic expansion and mechanical expansion. In 1957, A.Smith Company of the United States first developed a mechanical expander, obtained a patent, and put it into use in the company's Wilwaukee plant. Since then, almost all UOE welded pipe units built have adopted mechanical expanders. The comparison between mechanical expansion and hydraulic expansion is as follows:
(1) High efficiency when producing large diameter steel pipes. Due to the water pressure expansion, it is necessary to fill with low-pressure water first, and then pressurize, and then pressurize when the steel pipe yields. As the diameter of the produced pipe gradually increases, the efficiency is greatly reduced. The mechanical diameter expansion efficiency has little to do with the size of the pipe diameter, so relatively speaking, the efficiency is high when the pipe diameter is increased.
(2) It is easy to meet the strict requirements on the inner diameter of the steel pipe. When laying long-distance pipelines, the steel pipes are installed and welded in the field, and the inner diameter is the benchmark. It is becoming more and more strict, and hydraulic expansion is precisely to control the outer diameter of the steel pipe with the outer die sleeve, which cannot guarantee the dimensional accuracy of the inner diameter. Mechanical expansion is to expand the diameter with an expansion head inserted into the steel pipe, so the dimensional accuracy of the inner diameter of the steel pipe can be completely controlled, regardless of the change in wall thickness.
(3) Sui roundness is good. When the water pressure expands the diameter, the outer weld is in contact with the outer die sleeve, so that the nearby pipe wall is recessed, which destroys the roundness of the steel pipe. When mechanically expanding the diameter, as long as the welding seam is aligned with the groove of the fan-shaped block on the expanding head, the welding seam is not constrained during diameter expansion to form a smooth surface, which effectively reduces the damage caused by the welding part.
(4) The shape and size of the pipe end are of high precision. When comparing the diameter expansion effect of the weld, both ends of the steel pipe need to be pressed into the conical indenter, and the radial sealing is carried out by the sealing tension ring embedded on the indenter.In this way, the diameter expansion effect of the contact portion between the steel pipe end and the indenter is inconsistent with that of the steel pipe body. However, there is no such phenomenon in mechanical expansion, and the shape and size of the pipe end are good, which is beneficial to field installation and butt welding.
In addition, the biggest advantage of hydraulic expansion is that it can expand the diameter and conduct hydraulic tests at the same time, so it can reduce production sites and operators.
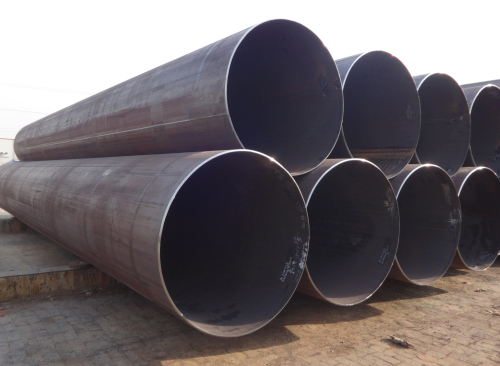
The process of mechanical expansion
Mechanical diameter expansion utilizes the segmented sector blocks at the end of the expander to expand radially, so that the tube blank can be step-by-step along the length direction to realize the process of plastic deformation of the full tube length in sections. Divided into 5 stages
1. Preliminary rounding stage. The fan-shaped block is opened until all the fan-shaped blocks touch the inner wall of the steel pipe. At this time, the radius of each point in the inner circular pipe of the steel pipe within the step size is almost the same, and the steel pipe is initially rounded.
2. Nominal inner diameter stage. The fan-shaped block starts to reduce the movement speed from the front position until it reaches the required position, which is the inner circumference position of the finished pipe with quality requirements.
3. Repetition compensation stage. The fan-shaped block starts to further reduce the speed at the position of stage 2 until it reaches the required position, which is the inner circumference position of the steel pipe before the rebound required by the process design.
4. Stable pressure holding stage. The inner circumference of the steel pipe remains stationary for a period of time before the sector block is bounced back, which is the pressure-holding and stable stage required by the equipment and the expansion process.
5. Unloading return stage. The fan-shaped block quickly retracts from the inner circumference of the steel pipe before the rebound until it reaches the initial diameter expansion position, which is the minimum shrinkage Note: diameter of the fan-shaped block required by the expansion process.
In practical applications, in the process simplification, steps 2 and 3 can be combined and simplified, which has no effect on the quality of the expansion of the steel pipe.
LSAW steel pipe expansion is a pressure processing process that uses hydraulic or mechanical means to apply force from the inner wall of the steel pipe to expand the steel pipe radially outward. The mechanical method is simpler and more efficient than the hydraulic method, and the steel pipe machining is more accurate under the condition of high precision.The expansion process of LSAW steel pipe is divided into mechanical expansion and hydraulic expansion.
The purpose of the expansion process
1) Correct the deformation of the steel pipe caused by the thermal effect of welding, so that the geometric dimensions of the steel pipe, such as pipe diameter, roundness, straightness, etc., can reach the required accuracy
Note: The diameter accuracy and geometric dimensions of steel pipes are one of the important indicators of quality control in the production process of welded pipes.Whether it is a pipeline steel pipe, or a steel pipe pile and structural steel pipe, it is formed by butt welding of multiple welded pipes. Therefore, there are strict technical requirements and standards for its pipe diameter tolerance, ovality and straightness.
(2) Eliminate the Baushinger Ef-fect produced by forming and compression during the pipe making process, and increase the strength of the steel pipe by 0~15% depending on the steel type.
(3) Eliminate the residual stress of the weld seam caused by the welding process, and avoid hydrogen embrittlement caused by hydrogen in the oil or natural gas in the area where the stress of the weld seam is concentrated and cause cracks.
The characteristics of mechanical expansion and hydraulic expansion
The expansion methods of LSAW steel pipes are divided into hydraulic expansion and mechanical expansion. In 1957, A.Smith Company of the United States first developed a mechanical expander, obtained a patent, and put it into use in the company's Wilwaukee plant. Since then, almost all UOE welded pipe units built have adopted mechanical expanders. The comparison between mechanical expansion and hydraulic expansion is as follows:
(1) High efficiency when producing large diameter steel pipes. Due to the water pressure expansion, it is necessary to fill with low-pressure water first, and then pressurize, and then pressurize when the steel pipe yields. As the diameter of the produced pipe gradually increases, the efficiency is greatly reduced. The mechanical diameter expansion efficiency has little to do with the size of the pipe diameter, so relatively speaking, the efficiency is high when the pipe diameter is increased.
(2) It is easy to meet the strict requirements on the inner diameter of the steel pipe. When laying long-distance pipelines, the steel pipes are installed and welded in the field, and the inner diameter is the benchmark. It is becoming more and more strict, and hydraulic expansion is precisely to control the outer diameter of the steel pipe with the outer die sleeve, which cannot guarantee the dimensional accuracy of the inner diameter. Mechanical expansion is to expand the diameter with an expansion head inserted into the steel pipe, so the dimensional accuracy of the inner diameter of the steel pipe can be completely controlled, regardless of the change in wall thickness.
(3) Sui roundness is good. When the water pressure expands the diameter, the outer weld is in contact with the outer die sleeve, so that the nearby pipe wall is recessed, which destroys the roundness of the steel pipe. When mechanically expanding the diameter, as long as the welding seam is aligned with the groove of the fan-shaped block on the expanding head, the welding seam is not constrained during diameter expansion to form a smooth surface, which effectively reduces the damage caused by the welding part.
(4) The shape and size of the pipe end are of high precision. When comparing the diameter expansion effect of the weld, both ends of the steel pipe need to be pressed into the conical indenter, and the radial sealing is carried out by the sealing tension ring embedded on the indenter.In this way, the diameter expansion effect of the contact portion between the steel pipe end and the indenter is inconsistent with that of the steel pipe body. However, there is no such phenomenon in mechanical expansion, and the shape and size of the pipe end are good, which is beneficial to field installation and butt welding.
In addition, the biggest advantage of hydraulic expansion is that it can expand the diameter and conduct hydraulic tests at the same time, so it can reduce production sites and operators.
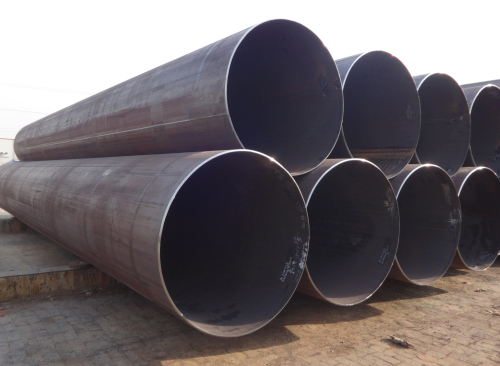
The process of mechanical expansion
Mechanical diameter expansion utilizes the segmented sector blocks at the end of the expander to expand radially, so that the tube blank can be step-by-step along the length direction to realize the process of plastic deformation of the full tube length in sections. Divided into 5 stages
1. Preliminary rounding stage. The fan-shaped block is opened until all the fan-shaped blocks touch the inner wall of the steel pipe. At this time, the radius of each point in the inner circular pipe of the steel pipe within the step size is almost the same, and the steel pipe is initially rounded.
2. Nominal inner diameter stage. The fan-shaped block starts to reduce the movement speed from the front position until it reaches the required position, which is the inner circumference position of the finished pipe with quality requirements.
3. Repetition compensation stage. The fan-shaped block starts to further reduce the speed at the position of stage 2 until it reaches the required position, which is the inner circumference position of the steel pipe before the rebound required by the process design.
4. Stable pressure holding stage. The inner circumference of the steel pipe remains stationary for a period of time before the sector block is bounced back, which is the pressure-holding and stable stage required by the equipment and the expansion process.
5. Unloading return stage. The fan-shaped block quickly retracts from the inner circumference of the steel pipe before the rebound until it reaches the initial diameter expansion position, which is the minimum shrinkage Note: diameter of the fan-shaped block required by the expansion process.
In practical applications, in the process simplification, steps 2 and 3 can be combined and simplified, which has no effect on the quality of the expansion of the steel pipe.