1. Roll Forming
Definition: A processing method that uses metal sheets or coils as raw materials, and gradually bends and deforms the blank through multiple racks equipped with forming rollers of a certain shape, thereby obtaining a uniform cross-section product. Generally, each frame is equipped with 2 or more forming rollers. This forming method is one of the most common methods in ERW pipes.
Characteristics of ERW pipes
(1) Multiple frames distribute the deformation amount, and the surface quality after molding is good.
(2) There are few equipment limiting factors, and it is suitable for both thin-walled and thick-walled welded pipes.
(3) The rollers for the closed forming part are not universal, and almost every product specification corresponds to a set of rollers. The number of rolls is large and the management cost is high.
(4) It takes a long time to change rollers, making it difficult to adapt to fast-paced, multi-specification production.
Although the equipment of the roll forming method is bulky, it is highly reliable. It is the pioneer of the welded pipe forming concept and has become the basis for many subsequent improvements and applications of ERW welded pipe forming technology.
2. row roller forming method (CageForming)
In the mid-1940s, it was pioneered by the American Torrance Company. It was improved by the American Yoder Company in the late 1960s. By the early 1980s, welded pipe equipment manufacturers around the world had developed a variety of machine models based on Yoder's original roller forming technology.
Row roller forming refers to the use of the 3-point bending principle in the continuous forming process of welded pipes to use multiple sets of passive small roller frames with adjustable positions and arranged in rows between the front-end transmission roller frame and the precision forming frame to replace several The horizontal roller and vertical roller frames enable the tube blank to complete deformation according to the designed pass system.
The main advantages of roller forming:
(1) Multiple rows of small rollers replace large rollers to reduce the linear speed difference on the roller surface, eliminate scratches, and improve the appearance of the steel pipe.
(2) Using the downhill method for forming, the motion trajectory of the edge of the strip is almost straight, which greatly reduces the edge extension.
(3) When changing specifications, the roller row section only needs to be adjusted and does not need to be replaced, which saves the time of changing rollers and improves production efficiency.
Disadvantages of roller forming:
(3) The strength and rigidity of the rollers in the roller section are insufficient, making it difficult to produce high-strength, large-wall-thickness welded pipe products.
Roller forming technology and equipment have been greatly improved on traditional roll forming technology, but there is still great potential for development in terms of roll versatility and unit stiffness.
Definition: A processing method that uses metal sheets or coils as raw materials, and gradually bends and deforms the blank through multiple racks equipped with forming rollers of a certain shape, thereby obtaining a uniform cross-section product. Generally, each frame is equipped with 2 or more forming rollers. This forming method is one of the most common methods in ERW pipes.
Characteristics of ERW pipes
(1) Multiple frames distribute the deformation amount, and the surface quality after molding is good.
(2) There are few equipment limiting factors, and it is suitable for both thin-walled and thick-walled welded pipes.
(3) The rollers for the closed forming part are not universal, and almost every product specification corresponds to a set of rollers. The number of rolls is large and the management cost is high.
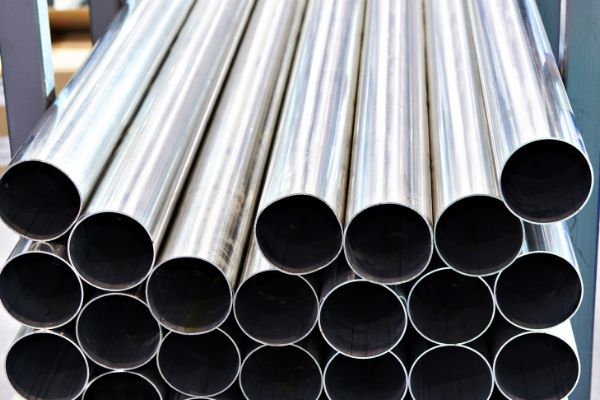
(4) It takes a long time to change rollers, making it difficult to adapt to fast-paced, multi-specification production.
Although the equipment of the roll forming method is bulky, it is highly reliable. It is the pioneer of the welded pipe forming concept and has become the basis for many subsequent improvements and applications of ERW welded pipe forming technology.
2. row roller forming method (CageForming)
In the mid-1940s, it was pioneered by the American Torrance Company. It was improved by the American Yoder Company in the late 1960s. By the early 1980s, welded pipe equipment manufacturers around the world had developed a variety of machine models based on Yoder's original roller forming technology.
Row roller forming refers to the use of the 3-point bending principle in the continuous forming process of welded pipes to use multiple sets of passive small roller frames with adjustable positions and arranged in rows between the front-end transmission roller frame and the precision forming frame to replace several The horizontal roller and vertical roller frames enable the tube blank to complete deformation according to the designed pass system.
The main advantages of roller forming:
(1) Multiple rows of small rollers replace large rollers to reduce the linear speed difference on the roller surface, eliminate scratches, and improve the appearance of the steel pipe.
(2) Using the downhill method for forming, the motion trajectory of the edge of the strip is almost straight, which greatly reduces the edge extension.
(3) When changing specifications, the roller row section only needs to be adjusted and does not need to be replaced, which saves the time of changing rollers and improves production efficiency.
Disadvantages of roller forming:
(1)The weakening of the strip preform not only adds more deformation force to the roller section and the finishing part, but also the edge forming is insufficient, and the requirements for the sizing machine are also higher.
(2) Insufficient strip traveling force may cause unstable welding speed.(3) The strength and rigidity of the rollers in the roller section are insufficient, making it difficult to produce high-strength, large-wall-thickness welded pipe products.
Roller forming technology and equipment have been greatly improved on traditional roll forming technology, but there is still great potential for development in terms of roll versatility and unit stiffness.