The flaring test is a method to test the deformation performance of the steel pipe end flaring process. When performing the flaring test, press the top core with a certain taper into one end of the metal tube sample to make it evenly expand to the flaring rate (%) specified in the relevant technical conditions, and then check whether there are cracks and other defects at the flaring , to determine whether it is qualified or not.
The characteristics of the expansion test
1. The test process is similar to the use conditions of the material.
2. Generally, the magnitude of the stress is not considered, but the quality of the material is assessed by the surface deformation (such as cracks, cracks, etc.) and certain characteristics after deformation. The test results can reflect the plasticity, toughness and some quality problems of the material.
3. The sample is easy to process.
4. The test method is simple and does not require complicated test equipment.
Therefore, the flaring test can be used as a product delivery condition according to the technical agreement. The pros and cons of the test results can provide the basis for improvement measures for material production enterprises such as melting and casting, cold and hot processing.
Principles of the expansion bore test
The steel pipe flaring test is a test method to test the deformation performance of the steel pipe from radial expansion to the specified diameter, and to show its defects. It is suitable for the determination of the flaring plastic deformation capacity of circular cross-section metal pipes with an outer diameter not exceeding 150mm (non-ferrous metal pipes not exceeding 100mm) and a pipe wall thickness not exceeding 10mm. It is suitable for seamless pipes and welded steel pipes.
Test principle: Use a conical top core to expand one end of the pipe section sample until the maximum outer diameter of the enlarged end reaches the value specified in the relevant product standard.
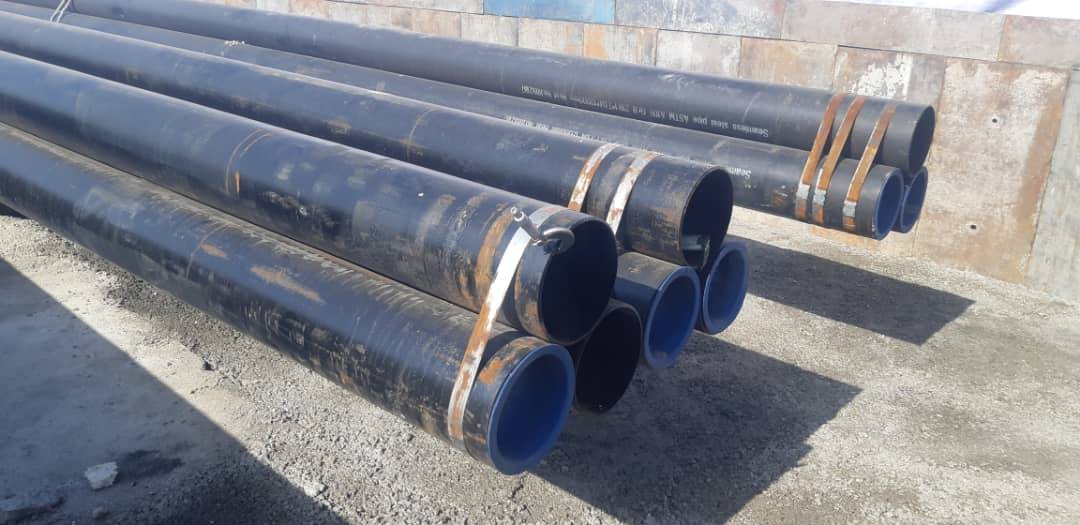
The method of dilated caliber test
1. According to the relevant technical conditions or the stipulations of the agreement between the two parties, select the top core with different taper angles. The recommended top core angles are 30°, 45° and 60°.
2. The test should generally be carried out at room temperature. For tests with strict temperature requirements, it should be controlled within (23±5)°C.
3. Apply force to the conical top core steadily to make it press into the end of the sample and expand evenly until the required outer diameter is reached. The maximum outer diameter or expansion rate of the sample after expansion shall be stipulated by relevant product standards. The expansion rate Xd is calculated according to the following formula:
Xd=(D0-D)/D×100%
In the formula, D0 and D are respectively the maximum outer diameter and the original outer diameter after the test, mm.
4. Allow the top core to be lubricated. The speed at which the top core is pressed into the sample is generally not specified, but in case of disputes or arbitration tests, the speed at which the top core is pressed into the sample should not exceed 50mm/min. The results of the flaring test shall be uated in accordance with the requirements of the relevant product standards. If no specific requirements are stipulated, the test sample without visible cracks should be uated as qualified, and only slight cracks at the edge of the sample should not be judged as scrapped.
Precautions for expansion test
1. During the test, the top cores with different tapers must be used according to the relevant technical documents. After the test, the top core and backing plate should be removed immediately.
2. The working surface of the top core should be polished and have sufficient hardness. During the test, the working surface of the top core can be coated with lubricating oil. Be careful when testing.
The characteristics of the expansion test
1. The test process is similar to the use conditions of the material.
2. Generally, the magnitude of the stress is not considered, but the quality of the material is assessed by the surface deformation (such as cracks, cracks, etc.) and certain characteristics after deformation. The test results can reflect the plasticity, toughness and some quality problems of the material.
3. The sample is easy to process.
4. The test method is simple and does not require complicated test equipment.
Therefore, the flaring test can be used as a product delivery condition according to the technical agreement. The pros and cons of the test results can provide the basis for improvement measures for material production enterprises such as melting and casting, cold and hot processing.
Principles of the expansion bore test
The steel pipe flaring test is a test method to test the deformation performance of the steel pipe from radial expansion to the specified diameter, and to show its defects. It is suitable for the determination of the flaring plastic deformation capacity of circular cross-section metal pipes with an outer diameter not exceeding 150mm (non-ferrous metal pipes not exceeding 100mm) and a pipe wall thickness not exceeding 10mm. It is suitable for seamless pipes and welded steel pipes.
Test principle: Use a conical top core to expand one end of the pipe section sample until the maximum outer diameter of the enlarged end reaches the value specified in the relevant product standard.
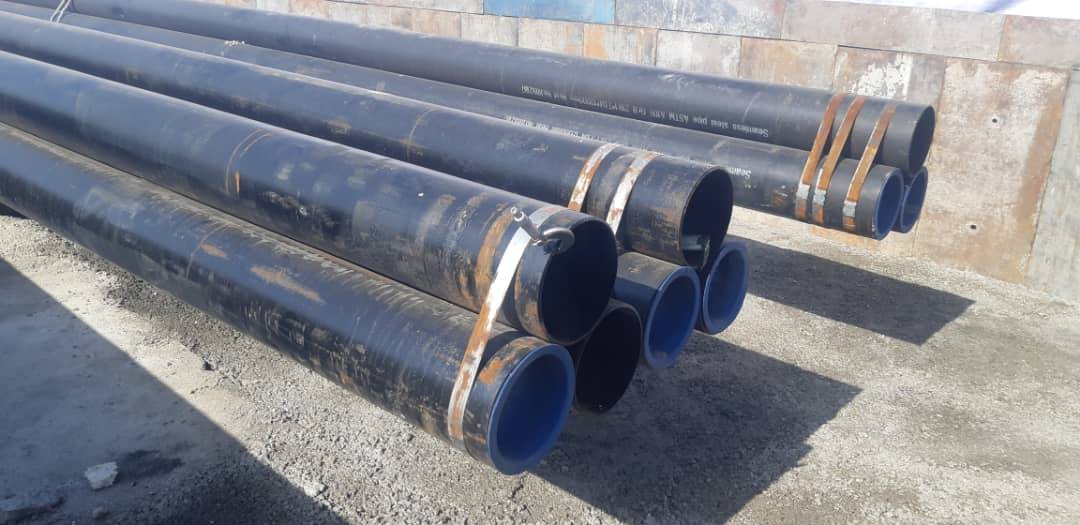
The method of dilated caliber test
1. According to the relevant technical conditions or the stipulations of the agreement between the two parties, select the top core with different taper angles. The recommended top core angles are 30°, 45° and 60°.
2. The test should generally be carried out at room temperature. For tests with strict temperature requirements, it should be controlled within (23±5)°C.
3. Apply force to the conical top core steadily to make it press into the end of the sample and expand evenly until the required outer diameter is reached. The maximum outer diameter or expansion rate of the sample after expansion shall be stipulated by relevant product standards. The expansion rate Xd is calculated according to the following formula:
Xd=(D0-D)/D×100%
In the formula, D0 and D are respectively the maximum outer diameter and the original outer diameter after the test, mm.
4. Allow the top core to be lubricated. The speed at which the top core is pressed into the sample is generally not specified, but in case of disputes or arbitration tests, the speed at which the top core is pressed into the sample should not exceed 50mm/min. The results of the flaring test shall be uated in accordance with the requirements of the relevant product standards. If no specific requirements are stipulated, the test sample without visible cracks should be uated as qualified, and only slight cracks at the edge of the sample should not be judged as scrapped.
Precautions for expansion test
1. During the test, the top cores with different tapers must be used according to the relevant technical documents. After the test, the top core and backing plate should be removed immediately.
2. The working surface of the top core should be polished and have sufficient hardness. During the test, the working surface of the top core can be coated with lubricating oil. Be careful when testing.