In the manufacturing and use process of welded tubes, non-destructive testing to ensure the quality of welds is particularly important. Commonly used non-destructive testing methods for welded tubes include: offline magnetic flux leakage testing, eddy current testing and ultrasonic flaw testing for the entire pipe body, which is more than 5mm away from the surface of the welded pipe; online magnetic flux leakage testing and eddy current testing, which are used to verify the welding quality more than 5mm away from the surface of the welded pipe; suitable for thick Off-line ultrasonic flaw detection of the entire weld body of wall welded tubes; ultrasonic flaw detection to verify the welding quality of thick wall welded tubes. This article will briefly introduce the commonly used flaw detection methods and technologies for welded tubes based on production experience, and analyze and compare their advantages and disadvantages.
1. Magnetic flux leakage inspection of the entire welded pipe body
Magnetic flux leakage inspection refers to a non-destructive testing technology that detects defects by detecting the leakage magnetic field and detecting the leakage magnetic field on the surface of the material after the ferromagnetic material is magnetized. Magnetic flux leakage inspection has low requirements on the surface condition of pipes and has a large detection depth. It is widely used in the inspection of welded tubes abroad. It has also been widely used in China, especially for the inspection of welded tubes used in petroleum. During production inspection, there have been cases where magnetic flux leakage inspection failed to detect large holes through the wall of welded tubes. In addition to management and personnel factors, this is related to the instrument, probe performance, and defect size and shape. Based on practical experience, I have concluded that the main factors affecting the accuracy of magnetic flux leakage flaw detection of the entire welded pipe body are as follows.
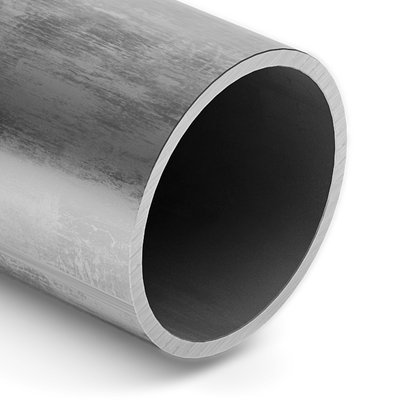
(1) Magnetization intensity
When the magnetization intensity is low, the leakage magnetic field is small and increases slowly; when the magnetic induction intensity reaches about 80% of the saturation value, the peak value of the defect leakage magnetic field will increase rapidly as the magnetization intensity increases. However, when the ferromagnetic material enters In the magnetic saturation state, the increase in external magnetization has little effect on the defect magnetic field intensity. Therefore, the design of the magnetic circuit should make the material under test reach a near-saturation magnetization state as much as possible.
(2) Direction, location and size of defects.
The direction of the defect has a great influence on the accuracy of magnetic flux leakage detection. When the main plane of the defect is perpendicular to the direction of the magnetizing magnetic field, the leakage magnetic field generated is the strongest. The leakage magnetic field is the largest when the same defect is located on the surface of the pipeline, and gradually decreases as the burial depth increases. When the burial depth is large enough, the leakage magnetic field will tend to zero. Therefore, the wall thickness of welded tubes that can be detected is generally 6~15mm; when the sensitivity is reduced, the wall thickness that can be detected is 20mm.
The size of the defect also has a great influence on the leakage magnetic field. When the defect width is the same but the depth is different, the leakage magnetic field increases with the increase of the defect depth, and within a certain range, the two are approximately in a linear relationship.The effect of defect width on the leakage magnetic field does not change monotonically. When the defect width is small, the leakage magnetic field tends to increase with the increase in width; but when the width is large, the leakage magnetic field decreases slowly as the width increases.
(3) Lift-off value
When the lift-off value exceeds 2 times the crack width, the leakage magnetic field intensity decreases rapidly as the lift-off height increases.The design of the sensor bracket must keep the lift-off value of the probe constant when scanning the surface of the steel pipe to be detected, which is generally less than 2mm, and is often 1mm.
(4) Flaw detection speed
During the flaw detection process, try to maintain a constant speed. Different speeds will cause different shapes of magnetic flux leakage signals, but generally it will not cause misjudgment.
(5) Surface quality of welded pipe
The thickness of the paint and other coatings on the surface of the welded pipe has a great impact on the flaw detection sensitivity. As the coating thickness increases, the flaw detection sensitivity drops sharply. Judging from the current instrument performance, when the coating thickness is ≥6mm, it is no longer possible to obtain effective defect identification signals.
The difference in surface roughness of the welded pipe causes the lift-off value between the sensor and the surface to be inspected to change dynamically, which will affect the consistency of the flaw detection sensitivity. In addition, it will also cause system vibration and noise, so the surface of the welded pipe to be inspected should be as smooth and flat as possible. .The oxide scale, rust and other debris on the surface of the welded pipe may also produce false signals during the flaw detection process, which should be confirmed or re-inspected in time.
2. Eddy current flaw detection of the entire welded pipe body
The characteristics of eddy current flaw detection method are:
①No coupling agent is required and can be performed non-contactly;
② The flaw detection speed is fast, enabling online production (up to 3 m/s, 2 m/s during normal production), and the time for adjusting and changing specifications is short (generally 10 to 20 minutes);
③Can detect high-temperature welded pipe welds;
④The flaw detection results are highly reliable. Due to the fast speed of eddy current flaw detection, the through-coil eddy current flaw detection method has been widely used to detect the quality of welded tubes, especially its compactness, for many years. However, it is difficult to detect longitudinal cracks in the welds of ferromagnetic welded tubes.
Therefore, in high-standard eddy current flaw detection, the probe coil eddy current flaw detection method is generally used. For the "internal burr adsorption" that often occurs in welded pipe welds, eddy current flaw detection equipment often falsely reports it as a defect.During the eddy current inspection process, the inner burrs are frequently adsorbed on the weld due to electromagnetic force. After leaving the eddy current magnetic field, the steel pipe contacts the automatic degaussing device. When there is no magnetic attraction, the inner burrs automatically fall off. After manual re-inspection, no defects are displayed.
Due to the influence of the skin effect, as the distance between the welded pipe under inspection and the detection coil increases, the detection sensitivity will gradually decrease. Therefore, for the same size defect, the signal amplitude reflected by the inner wall of the pipe will be smaller than that of the outer wall of the pipe. defects on.
The ability of the full-body eddy current flaw detection equipment for welded tubes to detect defects on the outer and inner surfaces of welded tubes is determined by many factors, but the most important ones depend on the wall thickness of the welded pipe being inspected, the eddy current excitation frequency and the magnetic saturation intensity. At the same time, when selecting instrument parameters, the impact of physical parameters such as conductivity and magnetic permeability of the welded pipe under inspection on the accuracy of eddy current flaw detection should also be considered.
3. Ultrasonic flaw detection of the entire welded pipe body
Ultrasonic flaw detection of the entire welded pipe body is mainly divided into direct contact method and liquid immersion method.
(1) Direct contact method
There is a very thin coupling agent layer between the ultrasonic probe and the detection surface of the specimen, so it can be regarded as direct contact between the two. The direct contact method is easy to operate, has relatively simple flaw detection patterns, is easy to judge, and has high sensitivity in detecting defects. It is the most commonly used method in actual flaw detection. However, this method requires higher accuracy on the detection surface of the tested specimen.
(2) Liquid immersion method
The method of immersing the ultrasonic probe and the workpiece in a liquid and using the liquid as a coupling agent for flaw detection is called the liquid immersion method. Coupling agent can be oil or water. The liquid immersion method is divided into full immersion and partial immersion.This method is suitable for specimens with rough surfaces. The probe is not easy to wear, the coupling is stable, the detection results are repeatable, and it is convenient for automated flaw detection.However, the propagation attenuation of sound waves in the pipe wall in the liquid immersion method is very serious. A better solution is to use the water film method instead of the water immersion method for acoustic coupling.
4. Ultrasonic flaw detection of welded pipe welds
(1) Off-line flaw detection of welds
The welded pipe is sent to the flaw detection area by the transfer roller, the rotating roller is raised, and the steel pipe weld seam is manually rotated on the roller to a certain point of the weld.The flaw detection car is running, and each set of probes falls on the welded pipe in sequence with a delayed delay. The coupling agent used for flaw detection is the emulsion of the welded pipe production line. It receives the sensing signal and is automatically sprayed on the weld and both sides.
Because the ultrasonic offline system is arranged after water cooling and air cooling, the influence of weld deviation becomes very important. Therefore, in the offline flaw detection of welds, two groups of 6 probes in total are used to detect longitudinal linear defects in welded pipe welds, each group has 3 probes. , distributed on both sides of the weld, bidirectional detection, occupying a total of 6 channels, and can perform normal flaw detection within the range of 15mm of weld rotation (deviation).
The flaw detection coverage range of a single longitudinal probe is 12.7mm in the vertical direction of the weld (6.4mm on both sides of the weld), and there is no blind zone coverage in the direction of the weld thickness (maximum 13.72mm) within the 12.7mm wide area in the vertical direction of the weld.The detection of transverse linear defects and point defects in the weld should also consider a small amount of twist (deviation) in the steel pipe weld.
Therefore, two groups of 6 probes are used, each group has 3 probes, distributed front and back. Even if the weld seam is twisted (deviated), the probe can always cover the flaw detection area. Due to the wide coverage area, it can scan 5mm in and out of the left and right sides of the weld seam to achieve full coverage. Bidirectional detection of weld seam coverage better ensures the accuracy of flaw detection quality control, and the transverse probe occupies a total of 6 channels. The device occupies a total of 12 channels.
In order to prevent probe wear and minimize direct contact between the probe and the welded pipe, steel pipe companies and flaw detection equipment production and R&D institutions jointly designed and studied the upgrade and improvement of probe shoes and probe covers.
In the upgrade of flaw detection equipment, most welded pipe manufacturers have adopted the control mode of offline flaw detection PLC + industrial computer to improve equipment control accuracy and avoid blind areas at pipe ends. Most flaw detection systems use paired probes to achieve coupled monitoring, consisting of 2 probes. One pair, symmetrically located on both sides of the weld, with different triggering times.
One of them triggers during the repetition frequency period, while the other triggers after a delay of 1/2 the repetition frequency period.If the coupling is good, one of the probes in the pair should be able to receive the transmitted signal of the other during the repetition frequency period.This "time-sharing mutual coupling monitoring" method can save flaw detection speed and defect feedback time, monitor the location and size of defects more accurately and timely, and improve flaw detection efficiency.
(2) Manual flaw detection of welds
Strict determination of defects detected by offline weld flaw detection requires manual flaw detection for confirmation. Before manual re-inspection and confirmation, the appearance of the weld and the flaw detection surface should be inspected. The appearance quality should comply with the relevant standards. The shape of both sides of the weld and the flaw detection surface should not affect the detection of defects, otherwise it should be repaired; the flaw detection inspector must Check the testing equipment to see if the instrument is placed in the correct position and direction, and whether the couplant and testing joints are correct.
The flaw detection equipment must be calibrated before manual re-inspection begins. After the first calibration, the second calibration must be performed every 3 to 4 hours. At the end of the inspection, the flaw detection equipment must be calibrated again.After the weld position is aligned, apply coupling agent (emulsion) on both sides of the weld for formal flaw detection; for steel pipes that fail the weld flaw detection, mark the defective areas and make detailed records.
Summarize
(1) Magnetic flux leakage inspection has high sensitivity and can well distinguish defects on the inner and outer walls of welded tubes. However, long pipe bodies and large-walled pipes need to be degaussed after magnetic flux leakage inspection.
(2) Eddy current flaw detection is fast, but limited by the skin effect, it is difficult to find defects deep in the workpiece.
(3) Ultrasonic testing has the characteristics of strong detection penetration, accurate defect location, low cost, and fast speed. However, the flaw detection operation requires coupling (it is recommended to use the water film method instead of the water immersion method for acoustic coupling) to detect. In the harsh northern winter environment The lower coupling welded pipe is easy to freeze, which brings inconvenience to the flaw detection operation.
(4) In the construction of new projects and welded pipe production, flaw detection methods, equipment selection and process technology should be comprehensively considered based on the characteristics, quality requirements, execution standards, and enterprise economic conditions of welded tubes.
1. Magnetic flux leakage inspection of the entire welded pipe body
Magnetic flux leakage inspection refers to a non-destructive testing technology that detects defects by detecting the leakage magnetic field and detecting the leakage magnetic field on the surface of the material after the ferromagnetic material is magnetized. Magnetic flux leakage inspection has low requirements on the surface condition of pipes and has a large detection depth. It is widely used in the inspection of welded tubes abroad. It has also been widely used in China, especially for the inspection of welded tubes used in petroleum. During production inspection, there have been cases where magnetic flux leakage inspection failed to detect large holes through the wall of welded tubes. In addition to management and personnel factors, this is related to the instrument, probe performance, and defect size and shape. Based on practical experience, I have concluded that the main factors affecting the accuracy of magnetic flux leakage flaw detection of the entire welded pipe body are as follows.
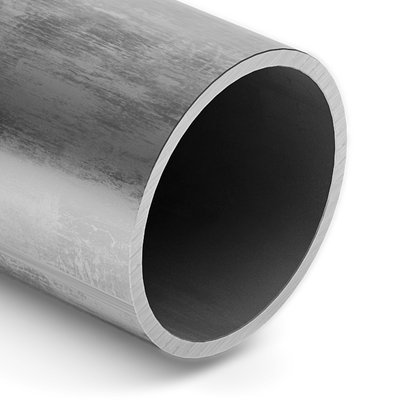
(1) Magnetization intensity
When the magnetization intensity is low, the leakage magnetic field is small and increases slowly; when the magnetic induction intensity reaches about 80% of the saturation value, the peak value of the defect leakage magnetic field will increase rapidly as the magnetization intensity increases. However, when the ferromagnetic material enters In the magnetic saturation state, the increase in external magnetization has little effect on the defect magnetic field intensity. Therefore, the design of the magnetic circuit should make the material under test reach a near-saturation magnetization state as much as possible.
(2) Direction, location and size of defects.
The direction of the defect has a great influence on the accuracy of magnetic flux leakage detection. When the main plane of the defect is perpendicular to the direction of the magnetizing magnetic field, the leakage magnetic field generated is the strongest. The leakage magnetic field is the largest when the same defect is located on the surface of the pipeline, and gradually decreases as the burial depth increases. When the burial depth is large enough, the leakage magnetic field will tend to zero. Therefore, the wall thickness of welded tubes that can be detected is generally 6~15mm; when the sensitivity is reduced, the wall thickness that can be detected is 20mm.
The size of the defect also has a great influence on the leakage magnetic field. When the defect width is the same but the depth is different, the leakage magnetic field increases with the increase of the defect depth, and within a certain range, the two are approximately in a linear relationship.The effect of defect width on the leakage magnetic field does not change monotonically. When the defect width is small, the leakage magnetic field tends to increase with the increase in width; but when the width is large, the leakage magnetic field decreases slowly as the width increases.
(3) Lift-off value
When the lift-off value exceeds 2 times the crack width, the leakage magnetic field intensity decreases rapidly as the lift-off height increases.The design of the sensor bracket must keep the lift-off value of the probe constant when scanning the surface of the steel pipe to be detected, which is generally less than 2mm, and is often 1mm.
(4) Flaw detection speed
During the flaw detection process, try to maintain a constant speed. Different speeds will cause different shapes of magnetic flux leakage signals, but generally it will not cause misjudgment.
(5) Surface quality of welded pipe
The thickness of the paint and other coatings on the surface of the welded pipe has a great impact on the flaw detection sensitivity. As the coating thickness increases, the flaw detection sensitivity drops sharply. Judging from the current instrument performance, when the coating thickness is ≥6mm, it is no longer possible to obtain effective defect identification signals.
The difference in surface roughness of the welded pipe causes the lift-off value between the sensor and the surface to be inspected to change dynamically, which will affect the consistency of the flaw detection sensitivity. In addition, it will also cause system vibration and noise, so the surface of the welded pipe to be inspected should be as smooth and flat as possible. .The oxide scale, rust and other debris on the surface of the welded pipe may also produce false signals during the flaw detection process, which should be confirmed or re-inspected in time.
2. Eddy current flaw detection of the entire welded pipe body
The characteristics of eddy current flaw detection method are:
①No coupling agent is required and can be performed non-contactly;
② The flaw detection speed is fast, enabling online production (up to 3 m/s, 2 m/s during normal production), and the time for adjusting and changing specifications is short (generally 10 to 20 minutes);
③Can detect high-temperature welded pipe welds;
④The flaw detection results are highly reliable. Due to the fast speed of eddy current flaw detection, the through-coil eddy current flaw detection method has been widely used to detect the quality of welded tubes, especially its compactness, for many years. However, it is difficult to detect longitudinal cracks in the welds of ferromagnetic welded tubes.
Therefore, in high-standard eddy current flaw detection, the probe coil eddy current flaw detection method is generally used. For the "internal burr adsorption" that often occurs in welded pipe welds, eddy current flaw detection equipment often falsely reports it as a defect.During the eddy current inspection process, the inner burrs are frequently adsorbed on the weld due to electromagnetic force. After leaving the eddy current magnetic field, the steel pipe contacts the automatic degaussing device. When there is no magnetic attraction, the inner burrs automatically fall off. After manual re-inspection, no defects are displayed.
Due to the influence of the skin effect, as the distance between the welded pipe under inspection and the detection coil increases, the detection sensitivity will gradually decrease. Therefore, for the same size defect, the signal amplitude reflected by the inner wall of the pipe will be smaller than that of the outer wall of the pipe. defects on.
The ability of the full-body eddy current flaw detection equipment for welded tubes to detect defects on the outer and inner surfaces of welded tubes is determined by many factors, but the most important ones depend on the wall thickness of the welded pipe being inspected, the eddy current excitation frequency and the magnetic saturation intensity. At the same time, when selecting instrument parameters, the impact of physical parameters such as conductivity and magnetic permeability of the welded pipe under inspection on the accuracy of eddy current flaw detection should also be considered.
3. Ultrasonic flaw detection of the entire welded pipe body
Ultrasonic flaw detection of the entire welded pipe body is mainly divided into direct contact method and liquid immersion method.
(1) Direct contact method
There is a very thin coupling agent layer between the ultrasonic probe and the detection surface of the specimen, so it can be regarded as direct contact between the two. The direct contact method is easy to operate, has relatively simple flaw detection patterns, is easy to judge, and has high sensitivity in detecting defects. It is the most commonly used method in actual flaw detection. However, this method requires higher accuracy on the detection surface of the tested specimen.
(2) Liquid immersion method
The method of immersing the ultrasonic probe and the workpiece in a liquid and using the liquid as a coupling agent for flaw detection is called the liquid immersion method. Coupling agent can be oil or water. The liquid immersion method is divided into full immersion and partial immersion.This method is suitable for specimens with rough surfaces. The probe is not easy to wear, the coupling is stable, the detection results are repeatable, and it is convenient for automated flaw detection.However, the propagation attenuation of sound waves in the pipe wall in the liquid immersion method is very serious. A better solution is to use the water film method instead of the water immersion method for acoustic coupling.
4. Ultrasonic flaw detection of welded pipe welds
(1) Off-line flaw detection of welds
The welded pipe is sent to the flaw detection area by the transfer roller, the rotating roller is raised, and the steel pipe weld seam is manually rotated on the roller to a certain point of the weld.The flaw detection car is running, and each set of probes falls on the welded pipe in sequence with a delayed delay. The coupling agent used for flaw detection is the emulsion of the welded pipe production line. It receives the sensing signal and is automatically sprayed on the weld and both sides.
Because the ultrasonic offline system is arranged after water cooling and air cooling, the influence of weld deviation becomes very important. Therefore, in the offline flaw detection of welds, two groups of 6 probes in total are used to detect longitudinal linear defects in welded pipe welds, each group has 3 probes. , distributed on both sides of the weld, bidirectional detection, occupying a total of 6 channels, and can perform normal flaw detection within the range of 15mm of weld rotation (deviation).
The flaw detection coverage range of a single longitudinal probe is 12.7mm in the vertical direction of the weld (6.4mm on both sides of the weld), and there is no blind zone coverage in the direction of the weld thickness (maximum 13.72mm) within the 12.7mm wide area in the vertical direction of the weld.The detection of transverse linear defects and point defects in the weld should also consider a small amount of twist (deviation) in the steel pipe weld.
Therefore, two groups of 6 probes are used, each group has 3 probes, distributed front and back. Even if the weld seam is twisted (deviated), the probe can always cover the flaw detection area. Due to the wide coverage area, it can scan 5mm in and out of the left and right sides of the weld seam to achieve full coverage. Bidirectional detection of weld seam coverage better ensures the accuracy of flaw detection quality control, and the transverse probe occupies a total of 6 channels. The device occupies a total of 12 channels.
In order to prevent probe wear and minimize direct contact between the probe and the welded pipe, steel pipe companies and flaw detection equipment production and R&D institutions jointly designed and studied the upgrade and improvement of probe shoes and probe covers.
In the upgrade of flaw detection equipment, most welded pipe manufacturers have adopted the control mode of offline flaw detection PLC + industrial computer to improve equipment control accuracy and avoid blind areas at pipe ends. Most flaw detection systems use paired probes to achieve coupled monitoring, consisting of 2 probes. One pair, symmetrically located on both sides of the weld, with different triggering times.
One of them triggers during the repetition frequency period, while the other triggers after a delay of 1/2 the repetition frequency period.If the coupling is good, one of the probes in the pair should be able to receive the transmitted signal of the other during the repetition frequency period.This "time-sharing mutual coupling monitoring" method can save flaw detection speed and defect feedback time, monitor the location and size of defects more accurately and timely, and improve flaw detection efficiency.
(2) Manual flaw detection of welds
Strict determination of defects detected by offline weld flaw detection requires manual flaw detection for confirmation. Before manual re-inspection and confirmation, the appearance of the weld and the flaw detection surface should be inspected. The appearance quality should comply with the relevant standards. The shape of both sides of the weld and the flaw detection surface should not affect the detection of defects, otherwise it should be repaired; the flaw detection inspector must Check the testing equipment to see if the instrument is placed in the correct position and direction, and whether the couplant and testing joints are correct.
The flaw detection equipment must be calibrated before manual re-inspection begins. After the first calibration, the second calibration must be performed every 3 to 4 hours. At the end of the inspection, the flaw detection equipment must be calibrated again.After the weld position is aligned, apply coupling agent (emulsion) on both sides of the weld for formal flaw detection; for steel pipes that fail the weld flaw detection, mark the defective areas and make detailed records.
Summarize
(1) Magnetic flux leakage inspection has high sensitivity and can well distinguish defects on the inner and outer walls of welded tubes. However, long pipe bodies and large-walled pipes need to be degaussed after magnetic flux leakage inspection.
(2) Eddy current flaw detection is fast, but limited by the skin effect, it is difficult to find defects deep in the workpiece.
(3) Ultrasonic testing has the characteristics of strong detection penetration, accurate defect location, low cost, and fast speed. However, the flaw detection operation requires coupling (it is recommended to use the water film method instead of the water immersion method for acoustic coupling) to detect. In the harsh northern winter environment The lower coupling welded pipe is easy to freeze, which brings inconvenience to the flaw detection operation.
(4) In the construction of new projects and welded pipe production, flaw detection methods, equipment selection and process technology should be comprehensively considered based on the characteristics, quality requirements, execution standards, and enterprise economic conditions of welded tubes.