1. Weld gap control of welded steel tube
The strip steel is sent to the welded pipe unit, rolled by multiple rollers, and the strip steel is gradually rolled up to form a round tube blank with an opening gap. Adjust the reduction of the extrusion roller to control the gap between the welds at 1~3mm, and make both ends of the welds flush. If the gap is too large, the proximity effect will be reduced, the heat of the eddy current will be insufficient, and the intergranular bonding of the weld will be poor, resulting in lack of fusion or cracking. If the gap is too small, the proximity effect will increase, and the welding heat will be too large, causing the weld seam to burn. Or the weld seam forms deep pits after extrusion and rolling, which affects the surface quality of the weld seam.
2. Welding temperature control of welded pipe
The welding temperature is mainly affected by the high-frequency eddy current thermal power. For low carbon steel, the welding temperature is controlled at 1250~1460°C, which can meet the penetration requirements of the pipe wall thickness of 3~5mm. In addition, the welding temperature can also be achieved by adjusting the welding speed. When the input heat is insufficient, the heated weld edge cannot reach the welding temperature, and the metal structure remains solid, forming incomplete fusion or incomplete penetration. When the input heat is insufficient, the heated weld edge exceeds the welding temperature, resulting in overburning or molten droplets, which cause the weld to form a molten hole.
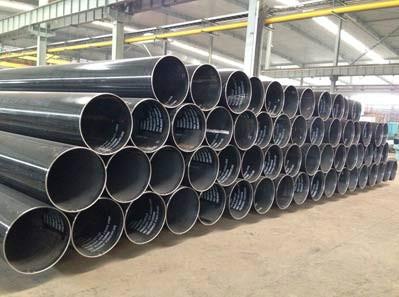
3. Control of extrusion force
After the two edges of the tube blank are heated to the welding temperature, under the extrusion of the extrusion roller, the common metal grains are formed to penetrate and crystallize each other, and finally form a firm weld. If the extrusion force is too small, the number of common crystals formed will be small, the strength of the weld metal will decrease, and cracks will occur after being stressed. If the extrusion force is too large, the metal in the molten state will be squeezed out of the weld, which not only reduces the strength of the weld, but also produces a large number of internal and external burrs, and even causes defects such as weld laps.
4. Regulation of the position of the high-frequency induction coil
The high-frequency induction coil should be as close as possible to the squeeze roller position. If the induction coil is far away from the extrusion roller, the effective heating time will be longer, the heat-affected zone will be wider, and the weld strength will decrease. On the contrary, the edge of the weld seam is insufficiently heated, and the molding is poor after extrusion
5. Weld scars will be produced after welding and extrusion, which need to be removed. The removal method is to fix the tool on the frame, and scrape the weld scars flat by the rapid movement of the welded pipe. The burrs inside the welded pipe are generally not removed.
The strip steel is sent to the welded pipe unit, rolled by multiple rollers, and the strip steel is gradually rolled up to form a round tube blank with an opening gap. Adjust the reduction of the extrusion roller to control the gap between the welds at 1~3mm, and make both ends of the welds flush. If the gap is too large, the proximity effect will be reduced, the heat of the eddy current will be insufficient, and the intergranular bonding of the weld will be poor, resulting in lack of fusion or cracking. If the gap is too small, the proximity effect will increase, and the welding heat will be too large, causing the weld seam to burn. Or the weld seam forms deep pits after extrusion and rolling, which affects the surface quality of the weld seam.
2. Welding temperature control of welded pipe
The welding temperature is mainly affected by the high-frequency eddy current thermal power. For low carbon steel, the welding temperature is controlled at 1250~1460°C, which can meet the penetration requirements of the pipe wall thickness of 3~5mm. In addition, the welding temperature can also be achieved by adjusting the welding speed. When the input heat is insufficient, the heated weld edge cannot reach the welding temperature, and the metal structure remains solid, forming incomplete fusion or incomplete penetration. When the input heat is insufficient, the heated weld edge exceeds the welding temperature, resulting in overburning or molten droplets, which cause the weld to form a molten hole.
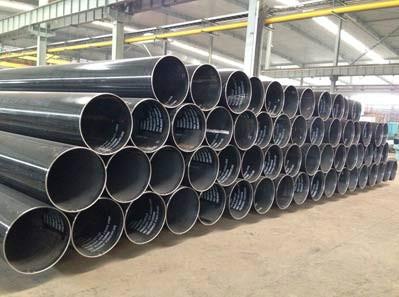
3. Control of extrusion force
After the two edges of the tube blank are heated to the welding temperature, under the extrusion of the extrusion roller, the common metal grains are formed to penetrate and crystallize each other, and finally form a firm weld. If the extrusion force is too small, the number of common crystals formed will be small, the strength of the weld metal will decrease, and cracks will occur after being stressed. If the extrusion force is too large, the metal in the molten state will be squeezed out of the weld, which not only reduces the strength of the weld, but also produces a large number of internal and external burrs, and even causes defects such as weld laps.
4. Regulation of the position of the high-frequency induction coil
The high-frequency induction coil should be as close as possible to the squeeze roller position. If the induction coil is far away from the extrusion roller, the effective heating time will be longer, the heat-affected zone will be wider, and the weld strength will decrease. On the contrary, the edge of the weld seam is insufficiently heated, and the molding is poor after extrusion
5. Weld scars will be produced after welding and extrusion, which need to be removed. The removal method is to fix the tool on the frame, and scrape the weld scars flat by the rapid movement of the welded pipe. The burrs inside the welded pipe are generally not removed.