Galvanized pipes are divided into two types: hot-dip galvanizing and electric galvanizing. Hot-dip galvanizing has a thick galvanized layer, which has the advantages of uniform coating, strong adhesion, and long service life. The cost of electro-galvanizing is low, the surface is not very smooth, and its corrosion resistance is much worse than that of hot-dip galvanized pipes.
Hot-dip galvanizing is a method in which steel pipes (seamless pipe or welded pipes) are immersed in molten zinc to obtain a metal coating. With the rapid development of high-voltage power transmission, transportation, and communication, the protection requirements for steel pipes are getting higher and higher, and the demand for hot-dip galvanized steel pipes is also increasing.
Hot-dip galvanizing principle:
The hot-dip galvanized pipe reacts the molten metal with the iron substrate to produce an alloy layer, so that the substrate and the coating are combined. Hot-dip galvanizing is to pickle the steel pipe first, in order to remove the iron oxide on the surface of the steel pipe. After pickling, it is washed in an ammonium chloride or zinc chloride aqueous solution or a mixed aqueous solution of ammonium chloride and zinc chloride, and then sent to a hot-dip coating tank. Hot-dip galvanizing has the advantages of uniform coating, strong adhesion and long service life. Complicated physical and chemical reactions occur between the steel pipe substrate and the molten plating solution to form a corrosion-resistant zinc-iron alloy layer with a tight structure. The alloy layer is integrated with the pure zinc layer and the steel pipe substrate. Therefore, it has strong corrosion resistance.
Tips:Clean the steel pipe, then solvent treatment, after drying, immerse in the zinc solution, the steel pipe reacts with the molten zinc to form an alloyed zinc layer, and the process is: degreasing-water washing-pickling-helping plating-drying --Hot-dip galvanizing--separation--cooling passivation.
Protection performance of hot-dip galvanized pipe
Usually the thickness of the electro-galvanized layer is 5-15 μm, while the thickness of the hot-dip galvanized layer is generally above 35 μm, even as high as 200 μm. Hot-dip galvanizing has good coverage, dense coating, and no organic inclusions. The mechanism of zinc’s anti-atmospheric corrosion includes mechanical protection and electrochemical protection. Under atmospheric corrosion conditions, there are ZnO, Zn(OH)2 and basic zinc carbonate protective films on the surface of the zinc layer, which can slow down the corrosion of zinc to a certain extent.
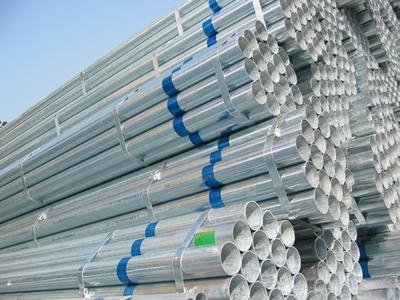
Galvanized layer formation process
The formation process of the hot-dip galvanized layer is the process of forming an iron-zinc alloy between the iron substrate and the outermost pure zinc layer. The iron-zinc alloy layer is formed on the surface of the steel pipe during hot-dip plating, which makes the iron and the pure zinc layer well bonded. The process can be simply described as: when the steel pipe is immersed in molten zinc, a solid solution is first formed on the interface. This is a crystal formed by dissolving zinc atoms in the base metal iron in a solid state. The two metal atoms are fused, and the attraction between the atoms is relatively small. Therefore, when zinc reaches saturation in the solid solution, the atoms of the two elements diffuse into each other, and the diffused zinc atoms migrate in the matrix lattice and gradually form an alloy with iron. The elements diffused into the molten zinc liquid form intermetallic compounds with zinc, and sink into the bottom of the hot-dip galvanizing pot, which is zinc slag. When the steel pipe is removed from the galvanizing solution, a pure zinc layer is formed on the surface, which is a hexagonal crystal. Its iron content is not more than 0.003%.
The technical difference between hot-dip galvanized pipe and cold-dip galvanized pipe
The corrosion resistance of hot-dip galvanizing is much higher than that of cold-dip galvanizing (also known as electro-galvanizing). Hot-dip galvanizing will not rust in a few years, and cold-dip galvanizing will rust in three months.
The cold galvanizing process is used to protect metals against corrosion by utilizing zinc filler coatings, which are applied to the surface to be protected by any of the application methods. After drying a zinc filler coating is formed, with a content of zinc (up to 95%) in the dried coating. The steel pipe is galvanized on the surface under the condition of cooling. And hot-dip galvanizing is that the steel pipe is galvanized on the surface under the condition of hot dipping, and its adhesion is very strong and it is not easy to fall off. Although hot-dip galvanized pipes also appear to be rusted, they can meet technical and hygienic requirements in a long period of time.
Advantages of hot-dip galvanized pipe
1. Low processing cost. The cost of hot-dip galvanized anti-rust is lower than that of other paint coatings;
2. Durable. In the suburban environment, the standard hot-dip galvanized anti-rust thickness can be maintained for more than 50 years without repair; in urban or offshore areas, the standard hot-dip galvanized anti-rust layer can be maintained for 20 years without repair;
3. Good reliability. There is a metallurgical bond between the galvanized layer and the steel, which becomes a part of the surface of the steel pipe, so the durability of the galvanized layer is more reliable;
4. The toughness of the coating is strong. The galvanized layer forms a special metallurgical structure that can withstand mechanical damage during transportation and use;
5. Comprehensive protection. Every part of the hot-dip galvanized pipe can be coated with zinc
6. Save time and effort. The galvanizing process is quicker than other coating application methods and avoids the time required to paint on the job site after installation.
7. Low initial cost. In general, hot-dip galvanizing is less expensive than applying other protective coatings. The reason is simple. Other protective coatings such as sandblasting paint are labor-intensive processes, whereas hot-dip galvanizing is a highly mechanized, tightly controlled in-plant process.
8. The inspection is simple and convenient. Hot-dip galvanized coatings can be tested visually and with a simple non-destructive coating thickness gauge
9. Reliability. The specifications of hot-dip galvanizing are generally implemented in accordance with BS EN ISO 1461, which limits the minimum thickness of the zinc layer, so the anti-rust period and performance are reliable and predictable.
Hot-dip galvanizing is a method in which steel pipes (seamless pipe or welded pipes) are immersed in molten zinc to obtain a metal coating. With the rapid development of high-voltage power transmission, transportation, and communication, the protection requirements for steel pipes are getting higher and higher, and the demand for hot-dip galvanized steel pipes is also increasing.
Hot-dip galvanizing principle:
The hot-dip galvanized pipe reacts the molten metal with the iron substrate to produce an alloy layer, so that the substrate and the coating are combined. Hot-dip galvanizing is to pickle the steel pipe first, in order to remove the iron oxide on the surface of the steel pipe. After pickling, it is washed in an ammonium chloride or zinc chloride aqueous solution or a mixed aqueous solution of ammonium chloride and zinc chloride, and then sent to a hot-dip coating tank. Hot-dip galvanizing has the advantages of uniform coating, strong adhesion and long service life. Complicated physical and chemical reactions occur between the steel pipe substrate and the molten plating solution to form a corrosion-resistant zinc-iron alloy layer with a tight structure. The alloy layer is integrated with the pure zinc layer and the steel pipe substrate. Therefore, it has strong corrosion resistance.
Tips:Clean the steel pipe, then solvent treatment, after drying, immerse in the zinc solution, the steel pipe reacts with the molten zinc to form an alloyed zinc layer, and the process is: degreasing-water washing-pickling-helping plating-drying --Hot-dip galvanizing--separation--cooling passivation.
Protection performance of hot-dip galvanized pipe
Usually the thickness of the electro-galvanized layer is 5-15 μm, while the thickness of the hot-dip galvanized layer is generally above 35 μm, even as high as 200 μm. Hot-dip galvanizing has good coverage, dense coating, and no organic inclusions. The mechanism of zinc’s anti-atmospheric corrosion includes mechanical protection and electrochemical protection. Under atmospheric corrosion conditions, there are ZnO, Zn(OH)2 and basic zinc carbonate protective films on the surface of the zinc layer, which can slow down the corrosion of zinc to a certain extent.
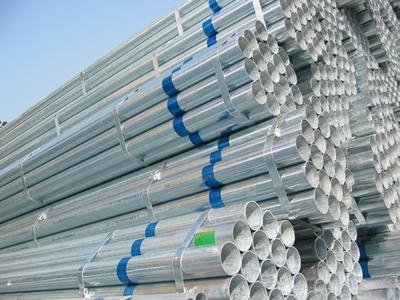
Galvanized layer formation process
The formation process of the hot-dip galvanized layer is the process of forming an iron-zinc alloy between the iron substrate and the outermost pure zinc layer. The iron-zinc alloy layer is formed on the surface of the steel pipe during hot-dip plating, which makes the iron and the pure zinc layer well bonded. The process can be simply described as: when the steel pipe is immersed in molten zinc, a solid solution is first formed on the interface. This is a crystal formed by dissolving zinc atoms in the base metal iron in a solid state. The two metal atoms are fused, and the attraction between the atoms is relatively small. Therefore, when zinc reaches saturation in the solid solution, the atoms of the two elements diffuse into each other, and the diffused zinc atoms migrate in the matrix lattice and gradually form an alloy with iron. The elements diffused into the molten zinc liquid form intermetallic compounds with zinc, and sink into the bottom of the hot-dip galvanizing pot, which is zinc slag. When the steel pipe is removed from the galvanizing solution, a pure zinc layer is formed on the surface, which is a hexagonal crystal. Its iron content is not more than 0.003%.
The technical difference between hot-dip galvanized pipe and cold-dip galvanized pipe
The corrosion resistance of hot-dip galvanizing is much higher than that of cold-dip galvanizing (also known as electro-galvanizing). Hot-dip galvanizing will not rust in a few years, and cold-dip galvanizing will rust in three months.
The cold galvanizing process is used to protect metals against corrosion by utilizing zinc filler coatings, which are applied to the surface to be protected by any of the application methods. After drying a zinc filler coating is formed, with a content of zinc (up to 95%) in the dried coating. The steel pipe is galvanized on the surface under the condition of cooling. And hot-dip galvanizing is that the steel pipe is galvanized on the surface under the condition of hot dipping, and its adhesion is very strong and it is not easy to fall off. Although hot-dip galvanized pipes also appear to be rusted, they can meet technical and hygienic requirements in a long period of time.
Advantages of hot-dip galvanized pipe
1. Low processing cost. The cost of hot-dip galvanized anti-rust is lower than that of other paint coatings;
2. Durable. In the suburban environment, the standard hot-dip galvanized anti-rust thickness can be maintained for more than 50 years without repair; in urban or offshore areas, the standard hot-dip galvanized anti-rust layer can be maintained for 20 years without repair;
3. Good reliability. There is a metallurgical bond between the galvanized layer and the steel, which becomes a part of the surface of the steel pipe, so the durability of the galvanized layer is more reliable;
4. The toughness of the coating is strong. The galvanized layer forms a special metallurgical structure that can withstand mechanical damage during transportation and use;
5. Comprehensive protection. Every part of the hot-dip galvanized pipe can be coated with zinc
6. Save time and effort. The galvanizing process is quicker than other coating application methods and avoids the time required to paint on the job site after installation.
7. Low initial cost. In general, hot-dip galvanizing is less expensive than applying other protective coatings. The reason is simple. Other protective coatings such as sandblasting paint are labor-intensive processes, whereas hot-dip galvanizing is a highly mechanized, tightly controlled in-plant process.
8. The inspection is simple and convenient. Hot-dip galvanized coatings can be tested visually and with a simple non-destructive coating thickness gauge
9. Reliability. The specifications of hot-dip galvanizing are generally implemented in accordance with BS EN ISO 1461, which limits the minimum thickness of the zinc layer, so the anti-rust period and performance are reliable and predictable.