Seamless line pipes are mainly used to transport high-pressure oil and gas near the wellhead. With the deepening of oil and natural gas exploitation, there are more and more oil and gas wells with complex exploitation conditions and in sulfur-containing environments, and the problem of hydrogen sulfide corrosion is becoming more and more serious. The development of sulfur-resistant seamless line pipes is imminent. The addition of Cu and Ni can improve the HIC performance of the seamless line pipe material, reduce the S content in the steel, and reduce the sensitivity of hydrogen bubbling by spraying silicon calcium powder.
1 Test method
According to the ISO3183 standard, using the immersion method, 7 furnaces of 1 t steel ingots were smelted in the laboratory. After forging, perforation, pipe jacking and stretching, they were made into tubes, and 20 mm × 100 mm × 5 mm plate thickness or tube thickness was cut from the steel pipe for test. The sample was immersed in a solution configured according to the standard, taken out after 96 hours, and the cross section was vertically rolled, and three parameters (crack length ratio CLR, crack thickness ratio CTR, and crack sensitivity ratio CSR) were calculated by metallographic method. Comparison of susceptibility to hydrogen-induced cracking (HIC).
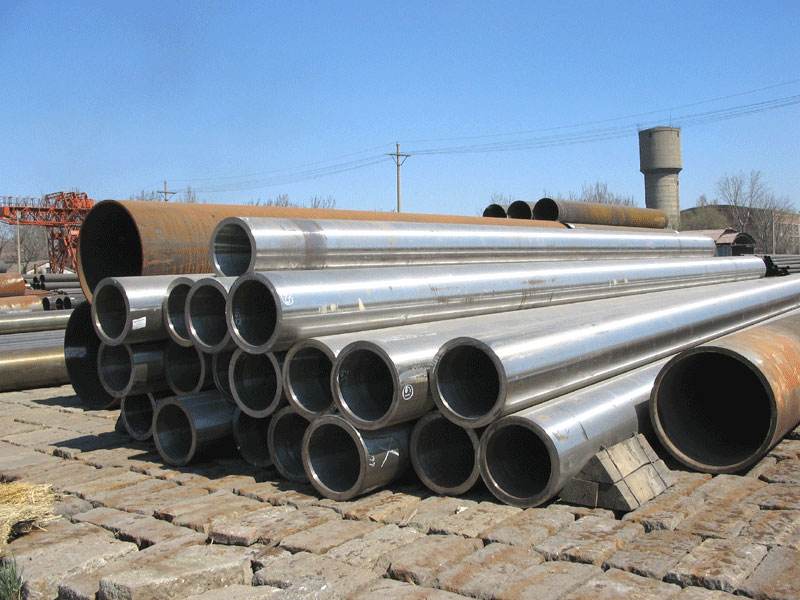
2 Factors Affecting HIC Performance
1) pH value. A large number of research results show that in the range of pH 1-6, the sensitivity of hydrogen bubbling decreases with the increase of pH, and when pH>6, hydrogen bubbling does not occur.
2) H2S concentration. The higher the concentration of hydrogen sulfide, the greater the susceptibility to hydrogen bubbling.
3) Chloride ions. In the pH range of 3.5 to 4.5, the presence of Cl- increases the corrosion rate and increases the sensitivity of hydrogen bubbling.
4) Temperature. At 25℃, the CLR is the largest, and the sensitivity of hydrogen bubbling is the largest. When the temperature is lower than 25°C, the corrosion reaction and the hydrogen diffusion rate are accelerated by the temperature increase, so that the sensitivity of hydrogen bubbling increases. However, after the temperature is higher than 25°C, the sensitivity of hydrogen bubbling decreases due to the decrease of H2S concentration.
5) Time. The test uses 96h as a comparison. Generally, with the increase of test time, the degree of corrosion tends to be serious.
1 Test method
According to the ISO3183 standard, using the immersion method, 7 furnaces of 1 t steel ingots were smelted in the laboratory. After forging, perforation, pipe jacking and stretching, they were made into tubes, and 20 mm × 100 mm × 5 mm plate thickness or tube thickness was cut from the steel pipe for test. The sample was immersed in a solution configured according to the standard, taken out after 96 hours, and the cross section was vertically rolled, and three parameters (crack length ratio CLR, crack thickness ratio CTR, and crack sensitivity ratio CSR) were calculated by metallographic method. Comparison of susceptibility to hydrogen-induced cracking (HIC).
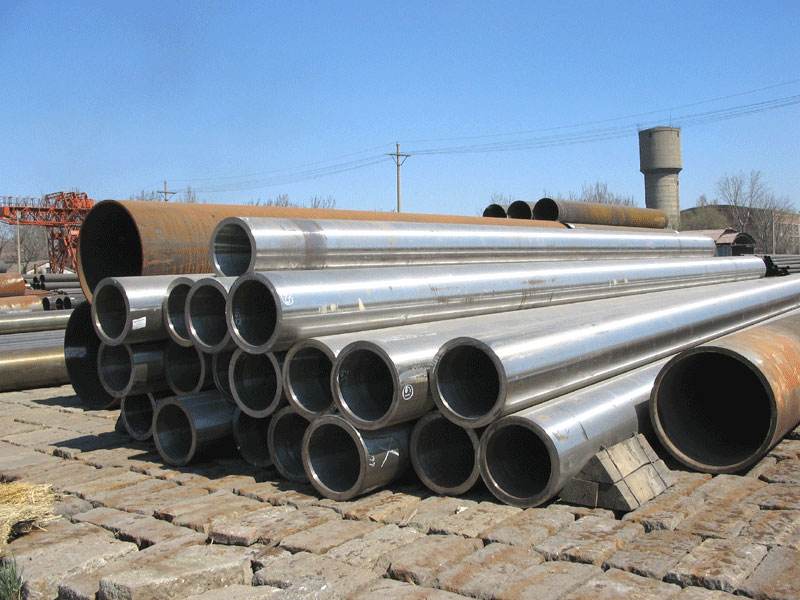
2 Factors Affecting HIC Performance
1) pH value. A large number of research results show that in the range of pH 1-6, the sensitivity of hydrogen bubbling decreases with the increase of pH, and when pH>6, hydrogen bubbling does not occur.
2) H2S concentration. The higher the concentration of hydrogen sulfide, the greater the susceptibility to hydrogen bubbling.
3) Chloride ions. In the pH range of 3.5 to 4.5, the presence of Cl- increases the corrosion rate and increases the sensitivity of hydrogen bubbling.
4) Temperature. At 25℃, the CLR is the largest, and the sensitivity of hydrogen bubbling is the largest. When the temperature is lower than 25°C, the corrosion reaction and the hydrogen diffusion rate are accelerated by the temperature increase, so that the sensitivity of hydrogen bubbling increases. However, after the temperature is higher than 25°C, the sensitivity of hydrogen bubbling decreases due to the decrease of H2S concentration.
5) Time. The test uses 96h as a comparison. Generally, with the increase of test time, the degree of corrosion tends to be serious.