Boiler tubes, as an indispensable key component in the industrial field, are like the arteries in the human body, shouldering the important mission of transporting heat energy. From the production process point of view, boiler tubes are mainly divided into two categories: seamless steel tubes and welded steel tubes. According to the difference in operating temperature, boiler tubes can be divided into general boiler tubes and high-pressure boiler tubes. In industrial production, the corrosion resistance of boiler tubes is like their "lifeline", which is of great significance in ensuring the safe operation of equipment, extending service life, improving production efficiency and reducing costs.
Main factors affecting the corrosion resistance of boiler tubes
Low alloy steel (such as 15CrMoG, 12Cr1MoVG): improves oxidation resistance and sulfur corrosion resistance through Cr and Mo elements.
Stainless steel (such as 304H, 321H, 316L): high Cr/Ni content, acid, alkali and chloride corrosion resistance, but high cost.
Duplex steel (such as 2205): resistant to chloride ion stress corrosion cracking (Cl-SCC), suitable for seawater or high salt environment.
2. Working environment
Temperature: high temperature (>400℃) accelerates oxidation and sulfidation corrosion.
Pressure: high pressure may aggravate stress corrosion cracking (SCC).
Medium:
Acidic medium (such as H₂S, CO₂) → prone to hydrogen embrittlement or sulfide corrosion.
Alkaline environment (such as NaOH) → may cause alkali embrittlement (caustic embrittlement).
Containing chloride ions (Cl⁻) → stainless steel is prone to pitting or Cl-SCC.
3. Protective measures
In order to improve the corrosion resistance of boiler tubes, some protective measures can also be taken. For example, the corrosion resistance of boiler tubes can be increased by surface treatment and coating, such as galvanizing, sandblasting, spraying, etc. In addition, regular maintenance and care of boiler tubes are also important means to ensure their corrosion resistance, timely clean up the sediment in the pipeline and prevent the formation of rust.
Inner wall coating/lining: such as enamel, epoxy resin coating, acid and alkali corrosion prevention.
Chemical water treatment: control pH value (8.5~9.2), deoxygenation (<7 ppb) to reduce oxygen corrosion.
Cathode protection: used for seawater or underground pipelines.
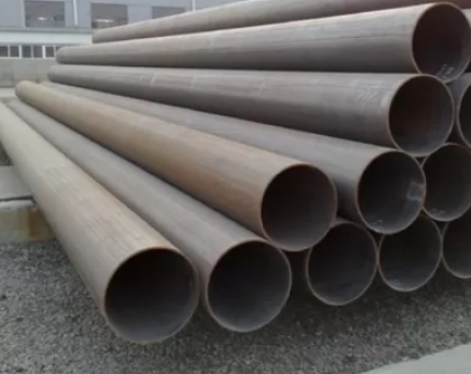
"Protection Secrets" to improve corrosion resistance
Faced with various challenges to the corrosion resistance of boiler tubes, we are not helpless. Through a series of scientific and effective protective measures, we can significantly improve the corrosion resistance of boiler tubes, extend their service life, and ensure the safe and stable operation of industrial production.
1. Strictly control water quality
Water quality is a key factor affecting boiler tube corrosion. Strictly controlling water quality is the primary task to improve the corrosion resistance of boiler tubes. In actual operation, it is necessary to ensure that the suspended solids content of the boiler feed water is less than or equal to 5mg/L, the total hardness is less than or equal to 0.03mmol/L, the pH value is controlled between 7-9, and the dissolved oxygen content is less than or equal to 0.1mg/L (for different types of boilers, the specific standards may be slightly different).
2. Metal surface treatment
Appropriate surface treatment of boiler tubes can form a protective film on the metal surface, effectively blocking the erosion of corrosive media. Common surface treatment technologies include electroplating, hot dip plating, shot blasting, sand blasting, etc.
3. Coating protection
Coating protection is a widely used anti-corrosion method. By applying a corrosion-resistant coating on the surface of the boiler tube, the contact between the corrosive medium and the metal can be isolated, thereby achieving the purpose of corrosion protection. Common corrosion-resistant coatings include epoxy resin coating, ceramic coating, silicone coating, etc.
4. Cathodic protection
Cathodic protection is an anti-corrosion technology based on electrochemical principles. It inhibits corrosion by making the boiler tube a cathode. There are two main types of cathodic protection: sacrificial anode method and impressed current method.
5. Reasonable material selection and design
During the selection and design stage of boiler tubes, it is crucial to fully consider their working environment and medium characteristics, select suitable materials and optimize pipeline design to improve their corrosion resistance. Select corresponding corrosion-resistant materials according to different corrosion environments.
By comprehensively applying the above protective measures, the corrosion resistance of boiler tubes can be effectively improved, providing a solid guarantee for the safe, stable and efficient operation of industrial production. In practical applications, appropriate protection methods should be selected according to specific working conditions and requirements, and maintenance management should be continuously strengthened to ensure that boiler tubes are always in good operating condition.
Read more: Introduction of High Pressure Boiler Tubes
Main factors affecting the corrosion resistance of boiler tubes
1. Boiler tube material
Carbon steel (such as 20G, SA210): resistant to general water vapor corrosion, but susceptible to oxygen corrosion and acidic medium erosion.Low alloy steel (such as 15CrMoG, 12Cr1MoVG): improves oxidation resistance and sulfur corrosion resistance through Cr and Mo elements.
Stainless steel (such as 304H, 321H, 316L): high Cr/Ni content, acid, alkali and chloride corrosion resistance, but high cost.
Duplex steel (such as 2205): resistant to chloride ion stress corrosion cracking (Cl-SCC), suitable for seawater or high salt environment.
2. Working environment
Temperature: high temperature (>400℃) accelerates oxidation and sulfidation corrosion.
Pressure: high pressure may aggravate stress corrosion cracking (SCC).
Medium:
Acidic medium (such as H₂S, CO₂) → prone to hydrogen embrittlement or sulfide corrosion.
Alkaline environment (such as NaOH) → may cause alkali embrittlement (caustic embrittlement).
Containing chloride ions (Cl⁻) → stainless steel is prone to pitting or Cl-SCC.
3. Protective measures
In order to improve the corrosion resistance of boiler tubes, some protective measures can also be taken. For example, the corrosion resistance of boiler tubes can be increased by surface treatment and coating, such as galvanizing, sandblasting, spraying, etc. In addition, regular maintenance and care of boiler tubes are also important means to ensure their corrosion resistance, timely clean up the sediment in the pipeline and prevent the formation of rust.
Inner wall coating/lining: such as enamel, epoxy resin coating, acid and alkali corrosion prevention.
Chemical water treatment: control pH value (8.5~9.2), deoxygenation (<7 ppb) to reduce oxygen corrosion.
Cathode protection: used for seawater or underground pipelines.
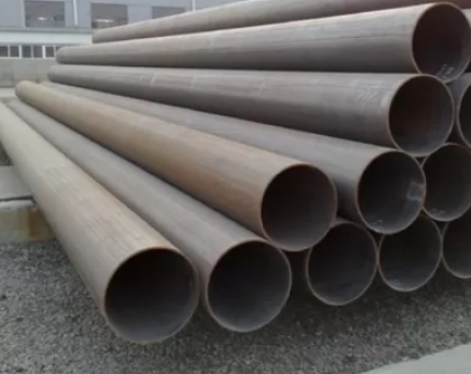
"Protection Secrets" to improve corrosion resistance
Faced with various challenges to the corrosion resistance of boiler tubes, we are not helpless. Through a series of scientific and effective protective measures, we can significantly improve the corrosion resistance of boiler tubes, extend their service life, and ensure the safe and stable operation of industrial production.
1. Strictly control water quality
Water quality is a key factor affecting boiler tube corrosion. Strictly controlling water quality is the primary task to improve the corrosion resistance of boiler tubes. In actual operation, it is necessary to ensure that the suspended solids content of the boiler feed water is less than or equal to 5mg/L, the total hardness is less than or equal to 0.03mmol/L, the pH value is controlled between 7-9, and the dissolved oxygen content is less than or equal to 0.1mg/L (for different types of boilers, the specific standards may be slightly different).
2. Metal surface treatment
Appropriate surface treatment of boiler tubes can form a protective film on the metal surface, effectively blocking the erosion of corrosive media. Common surface treatment technologies include electroplating, hot dip plating, shot blasting, sand blasting, etc.
3. Coating protection
Coating protection is a widely used anti-corrosion method. By applying a corrosion-resistant coating on the surface of the boiler tube, the contact between the corrosive medium and the metal can be isolated, thereby achieving the purpose of corrosion protection. Common corrosion-resistant coatings include epoxy resin coating, ceramic coating, silicone coating, etc.
4. Cathodic protection
Cathodic protection is an anti-corrosion technology based on electrochemical principles. It inhibits corrosion by making the boiler tube a cathode. There are two main types of cathodic protection: sacrificial anode method and impressed current method.
5. Reasonable material selection and design
During the selection and design stage of boiler tubes, it is crucial to fully consider their working environment and medium characteristics, select suitable materials and optimize pipeline design to improve their corrosion resistance. Select corresponding corrosion-resistant materials according to different corrosion environments.
By comprehensively applying the above protective measures, the corrosion resistance of boiler tubes can be effectively improved, providing a solid guarantee for the safe, stable and efficient operation of industrial production. In practical applications, appropriate protection methods should be selected according to specific working conditions and requirements, and maintenance management should be continuously strengthened to ensure that boiler tubes are always in good operating condition.
Read more: Introduction of High Pressure Boiler Tubes