JCOE pipe forming method is the main forming method of straight seam submerged arc welded pipe (LSAW). Sequential forming of O type, each step of stamping is based on three-point bending as the basic principle
Production process of JCOE
Material re-inspection→vacuum hoisting→plate detection→turning plate→creaming edge→upper plate→rolling the first half steel plate (J forming)→ loosening→inputting the second half steel plate→curling the second half steel plate (C forming)→ loosening→back bending →Pre-welding→Welding bow (extinguishing) arc plate→Internal welding→Root cleaning→External welding→De-lead (extinguishing) arc plate—Ultrasonic inspection→Mechanical expansion→Hydraulic test→Mechanical end repair→Ultrasonic inspection→Pipe end circumferential UT layer inspection→X-ray inspection→finished product inspection→magnetic particle inspection→weighing and length measurement→external anticorrosion→internal anticorrosion→marking→delivery.
The JCOE forming process press is equipped with an upper die with a longer arc segment and two lower dies with an arc surface.First, make half of the steel plate enter the forming machine laterally according to the set step size, and start from one side of the steel plate (leaving the pre-bending area) to form a predetermined curvature between the upper and lower dies of the press.Make half of the steel plate into a horizontal "J" shape first, and then lift the upper die.The steel plate is advanced by the traveling mechanism, so that the unformed side reaches the bottom of the mold for multi-step, step-by-step bending of the other half, forming a horizontal "C"-shaped tube failure. Finally, the final bending is performed in the middle of the "C"-shaped tube blank, so that the opening of the horizontal "C"-shaped tube blank is reduced to become an open "O"-shaped tube blank, that is, a JCOE forming process is completed.
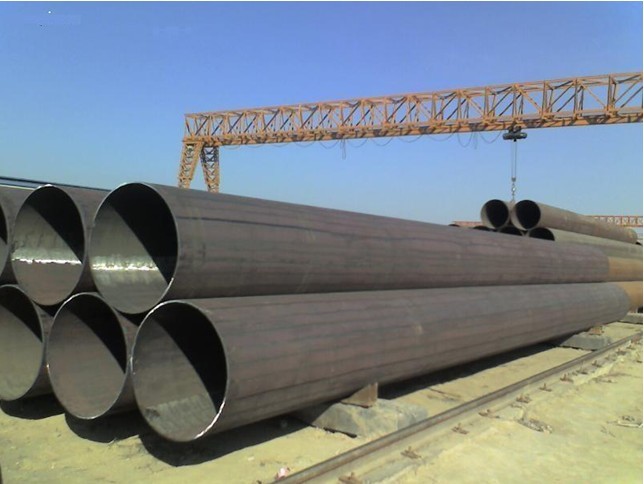
Advantages of JCOE molding method
The biggest feature of the JCOE forming method is that its press completes the forming of the tube blank by means of multi-step die bending. The production method is flexible, which can produce both large-volume products and small-volume products: it can produce large-diameter, high-strength, thick-walled steel pipes, as well as medium-diameter (406mm), thick-walled steel pipes. The annual output can reach 100,000 to 150,000 tons. This forming method is very suitable for medium-sized enterprises, and has become one of the DC forming technologies for modern LSAW pipe units.
The characteristics of modern JCOE molding are as follows:
1. Compared with the common UOE production line, the difference between the JCOE production line and the common UOE production line is that a JCOE molding machine is used to replace the U molding machine and the O molding machine of the UOE production line. Usually, the JCOE production line is equipped with 2 sets of internal and external welding devices and one mechanical full-length expanding machine, which can meet the normal production takt time requirements.
2. The ideal deformation of the steel plate is realized by the numerical control system, and the deformation of each part of the steel plate is uniform, and there is no obvious stress concentration.
3. The steel plate is always stretched during the process of forming to diameter expansion, the effect of wrapping and stretching is small, and the strength of the material is fully utilized.
4. Since there is almost no relative sliding between the mold and the steel plate during JCOE molding, the load and wear on the mold are much smaller than those in UO molding, so the mold loss is small and the service life is long.
5. The progressive JCOE forming process adopts the progressive bending forming method. Only a small part of the steel plate is bent and formed in each step, and it is not necessary to equip each pipe diameter with a mold.As a result, the number and mass of molds required are much less, and for the same pipe diameter range, the total tonnage of the JCOE forming mold is less than 5% of that of the UO forming mold.
6. The oxide scale in the forming process is less peeled off, easy to clean, and has little impact on the welding quality.
Note: UOE is also a forming process for straight seam welded pipes. Compared with JCOE, it has high cost and small production batches, poor flexibility when producing multi-specification steel pipes, and long adjustment time.Therefore, people decompose the UO steps, and on this basis, the JCOE molding technology was born.
Production process of JCOE
Material re-inspection→vacuum hoisting→plate detection→turning plate→creaming edge→upper plate→rolling the first half steel plate (J forming)→ loosening→inputting the second half steel plate→curling the second half steel plate (C forming)→ loosening→back bending →Pre-welding→Welding bow (extinguishing) arc plate→Internal welding→Root cleaning→External welding→De-lead (extinguishing) arc plate—Ultrasonic inspection→Mechanical expansion→Hydraulic test→Mechanical end repair→Ultrasonic inspection→Pipe end circumferential UT layer inspection→X-ray inspection→finished product inspection→magnetic particle inspection→weighing and length measurement→external anticorrosion→internal anticorrosion→marking→delivery.
The JCOE forming process press is equipped with an upper die with a longer arc segment and two lower dies with an arc surface.First, make half of the steel plate enter the forming machine laterally according to the set step size, and start from one side of the steel plate (leaving the pre-bending area) to form a predetermined curvature between the upper and lower dies of the press.Make half of the steel plate into a horizontal "J" shape first, and then lift the upper die.The steel plate is advanced by the traveling mechanism, so that the unformed side reaches the bottom of the mold for multi-step, step-by-step bending of the other half, forming a horizontal "C"-shaped tube failure. Finally, the final bending is performed in the middle of the "C"-shaped tube blank, so that the opening of the horizontal "C"-shaped tube blank is reduced to become an open "O"-shaped tube blank, that is, a JCOE forming process is completed.
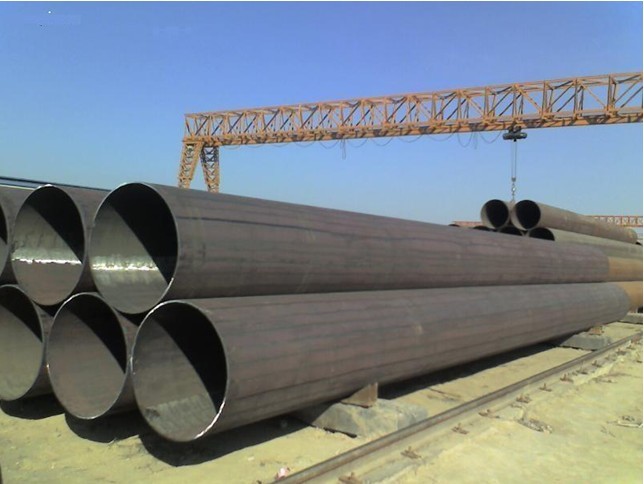
Advantages of JCOE molding method
The biggest feature of the JCOE forming method is that its press completes the forming of the tube blank by means of multi-step die bending. The production method is flexible, which can produce both large-volume products and small-volume products: it can produce large-diameter, high-strength, thick-walled steel pipes, as well as medium-diameter (406mm), thick-walled steel pipes. The annual output can reach 100,000 to 150,000 tons. This forming method is very suitable for medium-sized enterprises, and has become one of the DC forming technologies for modern LSAW pipe units.
The characteristics of modern JCOE molding are as follows:
1. Compared with the common UOE production line, the difference between the JCOE production line and the common UOE production line is that a JCOE molding machine is used to replace the U molding machine and the O molding machine of the UOE production line. Usually, the JCOE production line is equipped with 2 sets of internal and external welding devices and one mechanical full-length expanding machine, which can meet the normal production takt time requirements.
2. The ideal deformation of the steel plate is realized by the numerical control system, and the deformation of each part of the steel plate is uniform, and there is no obvious stress concentration.
3. The steel plate is always stretched during the process of forming to diameter expansion, the effect of wrapping and stretching is small, and the strength of the material is fully utilized.
4. Since there is almost no relative sliding between the mold and the steel plate during JCOE molding, the load and wear on the mold are much smaller than those in UO molding, so the mold loss is small and the service life is long.
5. The progressive JCOE forming process adopts the progressive bending forming method. Only a small part of the steel plate is bent and formed in each step, and it is not necessary to equip each pipe diameter with a mold.As a result, the number and mass of molds required are much less, and for the same pipe diameter range, the total tonnage of the JCOE forming mold is less than 5% of that of the UO forming mold.
6. The oxide scale in the forming process is less peeled off, easy to clean, and has little impact on the welding quality.
Note: UOE is also a forming process for straight seam welded pipes. Compared with JCOE, it has high cost and small production batches, poor flexibility when producing multi-specification steel pipes, and long adjustment time.Therefore, people decompose the UO steps, and on this basis, the JCOE molding technology was born.
Previous:API casing hydrotest pressure