On the surface of seamless steel pipes, scraps and extremely fine microscopic metal particles appear on the surface, which are called burrs. The more glitches, the lower its quality standard. The types of burrs mainly include flash burrs, sharp corner burrs, splashes, etc.
One of the surface defects of seamless steel pipes, which is manifested as uneven flash at the ends of cold-cut, hot-sawed or flame-cut steel. Welded steel pipes sometimes have excess metal extruded from the weld. The thickness of the end burrs on cold cut products depends on the gap between the cutting edges. General products allow a certain height of burrs; but the internal and external burrs of seamless steel pipes must be scraped off.
The reasons for the burrs of seamless steel pipes are:
(1) The cutting blade becomes dull and the gap is too large; the saw blade is dull or improperly installed;
(2) The punch is worn or improperly installed;
(3) Improper flame cutting operation;
(4) The welding system is not standardized.
For this problem, there is currently no effective way to eliminate it in the production process, so in order to ensure the design requirements of seamless steel pipes, engineers have to work hard to eliminate them later. So far, there have been many different deburring methods and equipment for different steel pipe products.
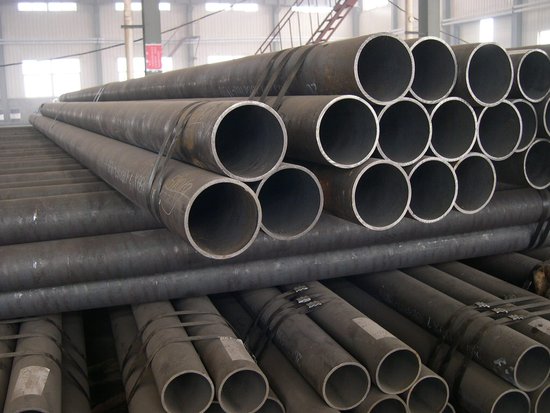
Method for removing burrs from seamless pipes
1) Manual deburring
It is the most commonly used method, using files, sandpaper, grinding heads, etc. as auxiliary tools. There are manual files and pneumatic interleavers.
Features: The labor cost is relatively expensive, the efficiency is not very high, and the complex cross holes are difficult to remove. The technical requirements for workers are not very high, and it is suitable for products with small burrs and simple product structure.
2) Die deburring
Deburring using production dies and punches.
Features: A certain mold (rough mold + fine mold) production fee is required, and a forming mold may also be required. It is suitable for products with simpler parting surfaces, and its efficiency and deburring effect are better than those of manual work.
3) Grinding and deburring
This type of deburring includes vibration, sandblasting, rollers, etc., and is currently used by many companies.
Features: There is a problem that the removal is not very clean, and subsequent manual processing of residual burrs or other deburring methods is required. Suitable for small products in large quantities.
4) Freeze deburring
The burrs are quickly embrittled using cooling and then blasted with projectiles to remove the burrs.
Features: The price of the equipment is around 200,000 or 300,000; it is suitable for products with small burr wall thickness and small products.
5) Hot air deburring
Also known as thermal deburring, explosion deburring. By introducing some flammable gas into the equipment furnace, and then through the action of some media and conditions, the gas will explode instantly, and the energy generated by the explosion will be used to dissolve and remove the burrs.
Features: expensive equipment, high operating technical requirements, low efficiency, side effects of rust and deformation; mainly used for some high-precision parts, such as automotive and aerospace precision parts.
6) Deburring of engraving machine
Features: The price of the equipment is not very expensive, it is suitable for simple space structure, and the required deburring position is simple and regular.
7) Chemical deburring
Using the principle of electrochemical reaction, parts made of metal materials can be automatically and selectively deburred.
Features: It is suitable for internal burrs that are difficult to remove, and suitable for small burrs (thickness less than 7 wires) of products such as pump bodies and valve bodies.
8) Electrolytic deburring
An electrolytic machining method that uses electrolysis to remove burrs from metal parts.
Features: The electrolyte is corrosive to a certain extent, and electrolysis also occurs near the burr of the parts, the surface will lose its original luster, and even affect the dimensional accuracy. The workpiece should be cleaned and rust-proof after deburring. Electrolytic deburring is suitable for deburring hidden parts of intersecting holes or parts with complex shapes. The production efficiency is high, and the deburring time is generally only a few seconds to tens of seconds. It is suitable for deburring gears, connecting rods, valve bodies and crankshaft oil passages, etc., as well as rounding of sharp corners.
9) High pressure water jet deburring
Using water as the medium, the instantaneous impact force is used to remove the burrs and flashes generated after processing, and at the same time achieve the purpose of cleaning.
Features: The equipment is expensive, mainly used in the heart of automobiles and hydraulic control systems of construction machinery.
10) Ultrasonic deburring
Ultrasonic produces instant high pressure to remove burrs.
Features: Mainly for some microscopic burrs. Generally, if you need to observe the burr with a microscope, you can try to remove it with ultrasonic waves.
One of the surface defects of seamless steel pipes, which is manifested as uneven flash at the ends of cold-cut, hot-sawed or flame-cut steel. Welded steel pipes sometimes have excess metal extruded from the weld. The thickness of the end burrs on cold cut products depends on the gap between the cutting edges. General products allow a certain height of burrs; but the internal and external burrs of seamless steel pipes must be scraped off.
The reasons for the burrs of seamless steel pipes are:
(1) The cutting blade becomes dull and the gap is too large; the saw blade is dull or improperly installed;
(2) The punch is worn or improperly installed;
(3) Improper flame cutting operation;
(4) The welding system is not standardized.
For this problem, there is currently no effective way to eliminate it in the production process, so in order to ensure the design requirements of seamless steel pipes, engineers have to work hard to eliminate them later. So far, there have been many different deburring methods and equipment for different steel pipe products.
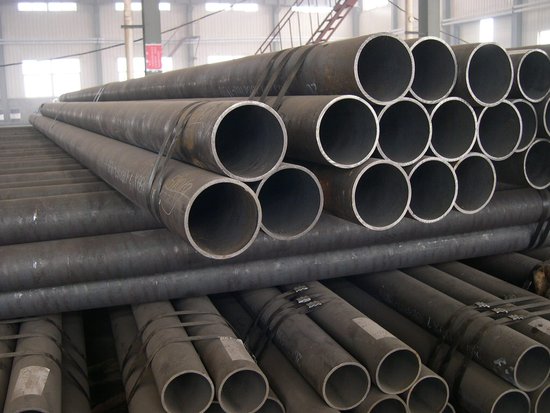
Method for removing burrs from seamless pipes
1) Manual deburring
It is the most commonly used method, using files, sandpaper, grinding heads, etc. as auxiliary tools. There are manual files and pneumatic interleavers.
Features: The labor cost is relatively expensive, the efficiency is not very high, and the complex cross holes are difficult to remove. The technical requirements for workers are not very high, and it is suitable for products with small burrs and simple product structure.
2) Die deburring
Deburring using production dies and punches.
Features: A certain mold (rough mold + fine mold) production fee is required, and a forming mold may also be required. It is suitable for products with simpler parting surfaces, and its efficiency and deburring effect are better than those of manual work.
3) Grinding and deburring
This type of deburring includes vibration, sandblasting, rollers, etc., and is currently used by many companies.
Features: There is a problem that the removal is not very clean, and subsequent manual processing of residual burrs or other deburring methods is required. Suitable for small products in large quantities.
4) Freeze deburring
The burrs are quickly embrittled using cooling and then blasted with projectiles to remove the burrs.
Features: The price of the equipment is around 200,000 or 300,000; it is suitable for products with small burr wall thickness and small products.
5) Hot air deburring
Also known as thermal deburring, explosion deburring. By introducing some flammable gas into the equipment furnace, and then through the action of some media and conditions, the gas will explode instantly, and the energy generated by the explosion will be used to dissolve and remove the burrs.
Features: expensive equipment, high operating technical requirements, low efficiency, side effects of rust and deformation; mainly used for some high-precision parts, such as automotive and aerospace precision parts.
6) Deburring of engraving machine
Features: The price of the equipment is not very expensive, it is suitable for simple space structure, and the required deburring position is simple and regular.
7) Chemical deburring
Using the principle of electrochemical reaction, parts made of metal materials can be automatically and selectively deburred.
Features: It is suitable for internal burrs that are difficult to remove, and suitable for small burrs (thickness less than 7 wires) of products such as pump bodies and valve bodies.
8) Electrolytic deburring
An electrolytic machining method that uses electrolysis to remove burrs from metal parts.
Features: The electrolyte is corrosive to a certain extent, and electrolysis also occurs near the burr of the parts, the surface will lose its original luster, and even affect the dimensional accuracy. The workpiece should be cleaned and rust-proof after deburring. Electrolytic deburring is suitable for deburring hidden parts of intersecting holes or parts with complex shapes. The production efficiency is high, and the deburring time is generally only a few seconds to tens of seconds. It is suitable for deburring gears, connecting rods, valve bodies and crankshaft oil passages, etc., as well as rounding of sharp corners.
9) High pressure water jet deburring
Using water as the medium, the instantaneous impact force is used to remove the burrs and flashes generated after processing, and at the same time achieve the purpose of cleaning.
Features: The equipment is expensive, mainly used in the heart of automobiles and hydraulic control systems of construction machinery.
10) Ultrasonic deburring
Ultrasonic produces instant high pressure to remove burrs.
Features: Mainly for some microscopic burrs. Generally, if you need to observe the burr with a microscope, you can try to remove it with ultrasonic waves.