High frequency resistance welded pipes(ERW steel pipe) are widely used. The produced steel pipe requires straight welds, no burrs, and no defects such as cracks, cracks, and unwelded welding, and the surface of the steel pipe does not exceed the specified scratches, pressure injuries and other defects. The eddy current inspection method has the advantages of fast detection speed, no need to couple with the surface of the workpiece, detection sensitivity, etc. It is very suitable for the quality control and quality inspection of welded pipe production.
Eddy current flaw detection is based on the principle of electromagnetic induction, which makes the steel pipe pass through a detection coil excited by a current of a specific frequency.When there is a defect on the surface or near surface of the steel pipe, the eddy current near it will change, which will change the impedance or induced voltage of the coil. The eddy current flaw detector is used to analyze this change, determine the defect and issue an alarm signal. Because eddy current flaw detection is easy to realize on-line detection, especially the alarm signal can be sent to the automatic control line of the production line for processing, and the automatic online sorting can be realized. Therefore, eddy current flaw detection has been widely used in welded pipe production lines.
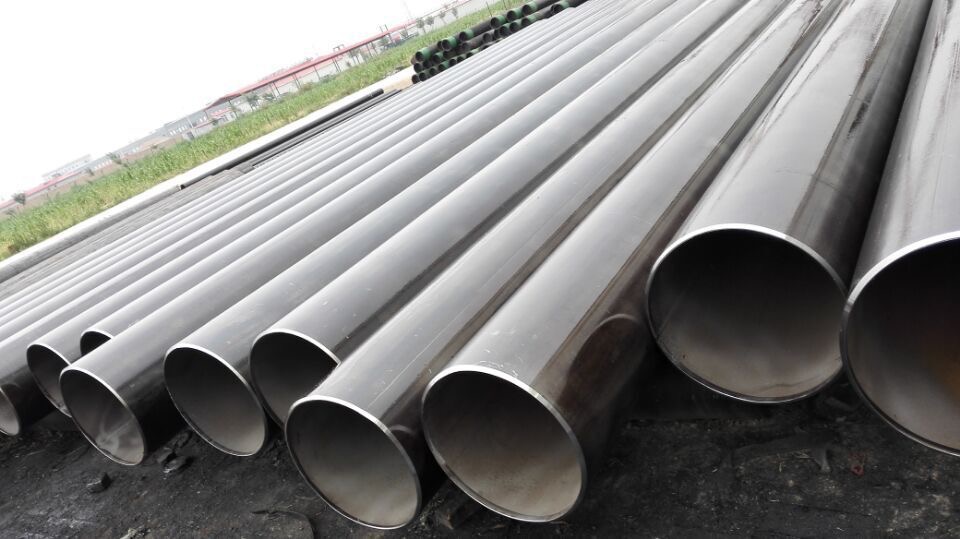
Common steel pipe quality defects
1. Base metal defects include: interlayers, surface cracks, surface indentations, and severe corrosion.
2. Weld defects include: long-pass cracks, local periodic cracks, irregular intermittent cracks, invisible cracks, and lap joints that appear after flattening, straightening or hydraulic testing.
Eddy current testing method
Among the aforementioned quality defects of steel pipes, interlayers, intermittent cracks, etc. are discontinuous defects in the longitudinal direction of the steel pipe, and self-comparison probes can be used for self-comparison detection.Long-pass cracks, lap joints and other defects can be detected by other comparison probes
Self-comparison detection: Use the two line circumferences along the longitudinal direction of the steel pipe to be tested to continuously detect the front and rear differences in the longitudinal direction of the steel pipe. It is very sensitive to the discontinuous defects in the longitudinal direction of the steel pipe such as interlayers, intermittent cracks, etc., but for long-pass cracks, such as the opening part without welding, only the beginning and end of the crack can be measured, and there is no response to other parts of the crack.
Other comparison detection: Using two detection coils, the standard sample tube and the online tested steel tube are continuously compared respectively, and defects such as long-pass cracks and lap welding can be detected.
In order to accurately detect all the quality defects of electric resistance welded pipes, both self-comparison and other-comparison probes are used on the welded pipe production line, and the self-comparison detection unit and the other-comparison detection unit are respectively connected.The steel pipe is continuously detected online, and the alarm signal is processed by the automatic sorting mechanism to realize online automatic detection and sorting.
Eddy current flaw detection is based on the principle of electromagnetic induction, which makes the steel pipe pass through a detection coil excited by a current of a specific frequency.When there is a defect on the surface or near surface of the steel pipe, the eddy current near it will change, which will change the impedance or induced voltage of the coil. The eddy current flaw detector is used to analyze this change, determine the defect and issue an alarm signal. Because eddy current flaw detection is easy to realize on-line detection, especially the alarm signal can be sent to the automatic control line of the production line for processing, and the automatic online sorting can be realized. Therefore, eddy current flaw detection has been widely used in welded pipe production lines.
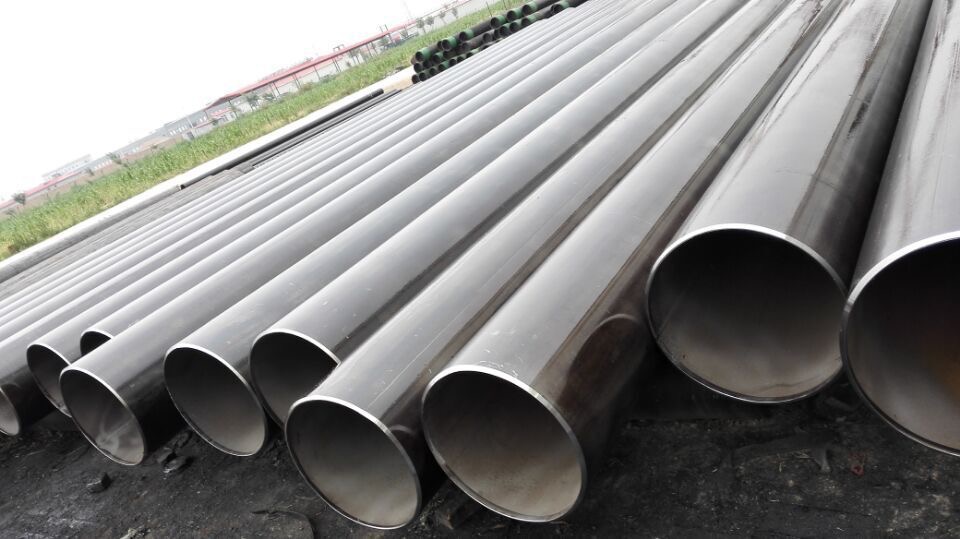
Common steel pipe quality defects
1. Base metal defects include: interlayers, surface cracks, surface indentations, and severe corrosion.
2. Weld defects include: long-pass cracks, local periodic cracks, irregular intermittent cracks, invisible cracks, and lap joints that appear after flattening, straightening or hydraulic testing.
Eddy current testing method
Among the aforementioned quality defects of steel pipes, interlayers, intermittent cracks, etc. are discontinuous defects in the longitudinal direction of the steel pipe, and self-comparison probes can be used for self-comparison detection.Long-pass cracks, lap joints and other defects can be detected by other comparison probes
Self-comparison detection: Use the two line circumferences along the longitudinal direction of the steel pipe to be tested to continuously detect the front and rear differences in the longitudinal direction of the steel pipe. It is very sensitive to the discontinuous defects in the longitudinal direction of the steel pipe such as interlayers, intermittent cracks, etc., but for long-pass cracks, such as the opening part without welding, only the beginning and end of the crack can be measured, and there is no response to other parts of the crack.
Other comparison detection: Using two detection coils, the standard sample tube and the online tested steel tube are continuously compared respectively, and defects such as long-pass cracks and lap welding can be detected.
In order to accurately detect all the quality defects of electric resistance welded pipes, both self-comparison and other-comparison probes are used on the welded pipe production line, and the self-comparison detection unit and the other-comparison detection unit are respectively connected.The steel pipe is continuously detected online, and the alarm signal is processed by the automatic sorting mechanism to realize online automatic detection and sorting.