The submerged arc welding method is one of the main production methods of welded steel pipes. Steel pipes welded by the submerged arc welding process include straight seam submerged arc welded steel pipes (LSAW steel pipes) and spiral submerged arc welded steel pipes (SSAW steel pipes).
The principle of submerged arc welding:
Submerged arc welding uses arc heat energy for welding. Unlike manual arc welding, the wire of submerged arc welding is exposed and has no coating on it. In submerged arc welding, the flux is laid in advance on the area to be welded. The submerged arc welding wire extends into the flux, and the arc burns under the flux.
The welding wire is in contact with the workpiece and the start button is pressed. At the moment when the welding wire and the workpiece are energized, the welding wire is withdrawn, the arc ignites, the welding car moves forward, and the welding wire is continuously transported downward, maintaining the arc burning under the flux layer, and forming a welding molten pool below the arc. Around the arc, the flux melts to form a cavity. This cavity and molten pool continue to advance, while the metal behind the molten pool solidifies, forming a continuous weld. Since this process is carried out under flux, we cannot see it with the naked eye. Can be seen with the help of X-ray photography.
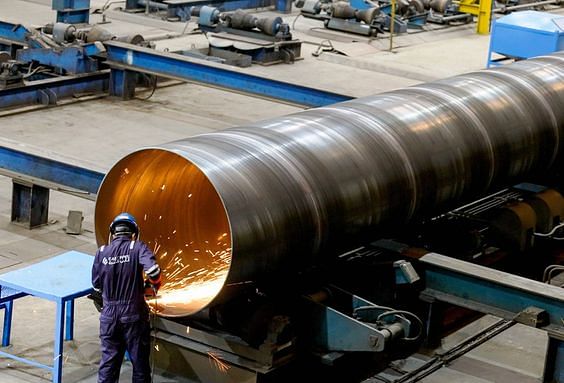
Advantages of submerged arc welding of steel pipes
1. High production efficiency, less production auxiliary time, saving time in changing welding rods;
2. The welding conditions are clean and spatter-free, saving cleaning time; the weld quality is high.
3. It also provides necessary conditions for the delivery of spiral steel pipe factories, ensuring the production time of large-volume spiral steel pipes, so it is still widely used.
Spiral seam submerged arc welded steel pipe is formed by bending the strip in a spiral shape, and using submerged arc automatic welding to weld the inner seam and outer seam to form a spiral seam steel pipe. It is widely used in the production of large diameter steel pipes for the following reasons:
1. As long as the forming angle is changed, steel pipes of various diameters can be produced from strip steel of the same width;
2. Because the neck joint is formed by continuous bending, the fixed length of the steel pipe is not limited;
3. The spiral welds are evenly distributed on the entire circumference of the steel pipe, so the dimensional accuracy of the steel pipe is high and the strength is higher than that of brown steel pipes;
4. The equipment is cheap, easy to change size, and suitable for the production of small batches and multiple varieties of steel pipes.
The principle of submerged arc welding:
Submerged arc welding uses arc heat energy for welding. Unlike manual arc welding, the wire of submerged arc welding is exposed and has no coating on it. In submerged arc welding, the flux is laid in advance on the area to be welded. The submerged arc welding wire extends into the flux, and the arc burns under the flux.
The welding wire is in contact with the workpiece and the start button is pressed. At the moment when the welding wire and the workpiece are energized, the welding wire is withdrawn, the arc ignites, the welding car moves forward, and the welding wire is continuously transported downward, maintaining the arc burning under the flux layer, and forming a welding molten pool below the arc. Around the arc, the flux melts to form a cavity. This cavity and molten pool continue to advance, while the metal behind the molten pool solidifies, forming a continuous weld. Since this process is carried out under flux, we cannot see it with the naked eye. Can be seen with the help of X-ray photography.
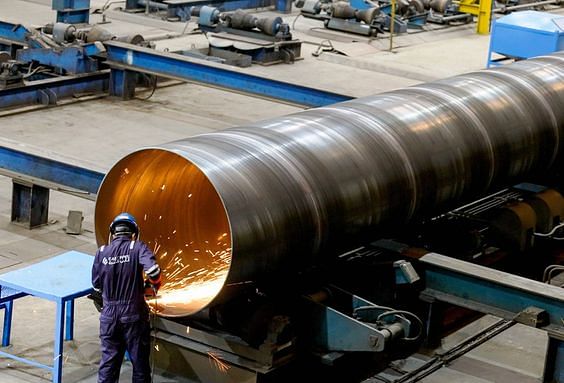
Advantages of submerged arc welding of steel pipes
1. High production efficiency, less production auxiliary time, saving time in changing welding rods;
2. The welding conditions are clean and spatter-free, saving cleaning time; the weld quality is high.
3. It also provides necessary conditions for the delivery of spiral steel pipe factories, ensuring the production time of large-volume spiral steel pipes, so it is still widely used.
Spiral seam submerged arc welded steel pipe is formed by bending the strip in a spiral shape, and using submerged arc automatic welding to weld the inner seam and outer seam to form a spiral seam steel pipe. It is widely used in the production of large diameter steel pipes for the following reasons:
1. As long as the forming angle is changed, steel pipes of various diameters can be produced from strip steel of the same width;
2. Because the neck joint is formed by continuous bending, the fixed length of the steel pipe is not limited;
3. The spiral welds are evenly distributed on the entire circumference of the steel pipe, so the dimensional accuracy of the steel pipe is high and the strength is higher than that of brown steel pipes;
4. The equipment is cheap, easy to change size, and suitable for the production of small batches and multiple varieties of steel pipes.