The welding of the straight seam steel pipe adopts the milling method. In addition to traditional JCO and UO technologies, some manufacturers have adopted more advanced progressive forming (PFP) technology, roll bending forming (RBE) technology. According to the production process, straight seam steel pipes can be divided into electric resistance welded pipes (ERW pipes) and submerged arc welded straight seam steel pipes (LSAW steel pipes).
During production, strict process standards need to be installed.
1. Determine the raw material. The raw materials are strip coils, welding wire and flux. All raw materials are subject to strict physical and chemical inspections before input.
2. Welding technology. The technology used in the production is divided into single-wire or double-wire submerged arc welding, and automatic submerged arc welding is used for repair welding after rolling into steel pipes.
3. Molding. Before forming, the strip steel needs to be leveled, trimmed, planed, surface cleaned, transported and pre-bent. At the same time, in order to ensure the smooth conveying of strip steel, it is necessary to use electric contact pressure gauges to control the pressure of the pressing oil cylinders on both sides of the conveyor. When forming, external control or internal control roll forming can be used.
4. When using the weld gap control device, the weld gap needs to meet the welding requirements, and the pipe diameter, misalignment and weld gap must also be implemented in strict accordance with the standards. Both internal welding and external welding are performed by American Lincoln welding machine for single-wire or double-wire submerged arc welding, so as to ensure the welding quality.
5. The welded seams are all inspected by the online continuous ultrasonic automatic damage instrument to ensure 100% non-destructive testing coverage of the welds and prevent the production of defective products.
After the production of longitudinal welded pipe is completed, it must be moved. Without the bag, the finish will have nicks and scratches which will affect the look of the finish.
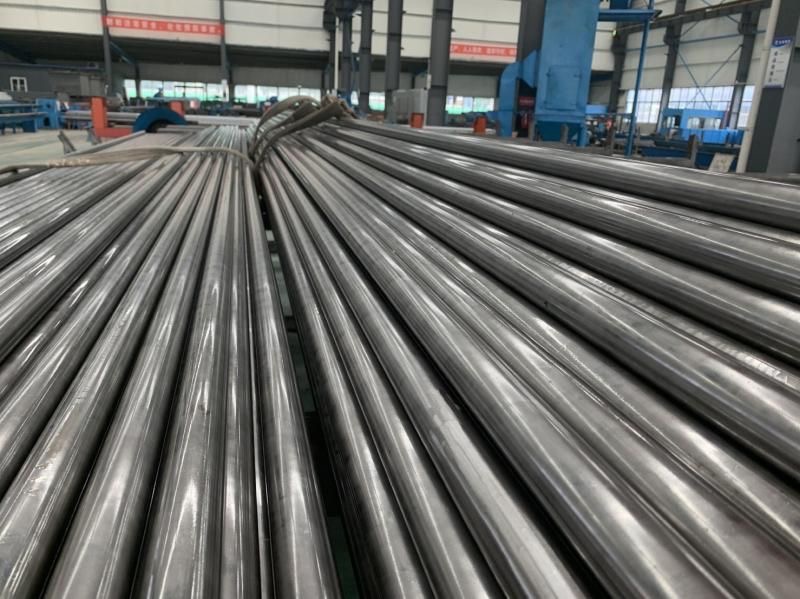
Control of soldering temperature
The welding temperature of straight seam steel pipe is mainly affected by the high-frequency eddy current heat power. When the heat input is insufficient, the heated weld edge will not reach the welding temperature. Finally, adjust the position of the high-frequency induction loop. The farther the induction ring is from the pressure roller, the longer the effective heating time and the larger the area affected by heat. When welding straight seam pipe, the voltage and welding speed need to be adjusted to a certain extent, and there is no need to adjust the parameters after modifying the parameters.The welding standards for repairing straight seam steel pipes are as follows:
1. The surface defects of longitudinally welded steel pipes must be completely eliminated.
2. The total length of the repair weld of each steel pipe of the longitudinally welded steel pipe shall be less than or equal to 5% of the total length of the longitudinally welded steel pipe.
3. The multi-weld defects of longitudinally welded steel pipes with a length less than 100mm should be repaired as a continuous single weld. A single weld of longitudinally welded steel pipes shall be repaired at least twice, and the length of the repaired weld shall be at least 50 mm.
4. The number of repair welds for straight seam welded steel pipes shall not exceed two times each time.
During production, strict process standards need to be installed.
1. Determine the raw material. The raw materials are strip coils, welding wire and flux. All raw materials are subject to strict physical and chemical inspections before input.
2. Welding technology. The technology used in the production is divided into single-wire or double-wire submerged arc welding, and automatic submerged arc welding is used for repair welding after rolling into steel pipes.
3. Molding. Before forming, the strip steel needs to be leveled, trimmed, planed, surface cleaned, transported and pre-bent. At the same time, in order to ensure the smooth conveying of strip steel, it is necessary to use electric contact pressure gauges to control the pressure of the pressing oil cylinders on both sides of the conveyor. When forming, external control or internal control roll forming can be used.
4. When using the weld gap control device, the weld gap needs to meet the welding requirements, and the pipe diameter, misalignment and weld gap must also be implemented in strict accordance with the standards. Both internal welding and external welding are performed by American Lincoln welding machine for single-wire or double-wire submerged arc welding, so as to ensure the welding quality.
5. The welded seams are all inspected by the online continuous ultrasonic automatic damage instrument to ensure 100% non-destructive testing coverage of the welds and prevent the production of defective products.
After the production of longitudinal welded pipe is completed, it must be moved. Without the bag, the finish will have nicks and scratches which will affect the look of the finish.
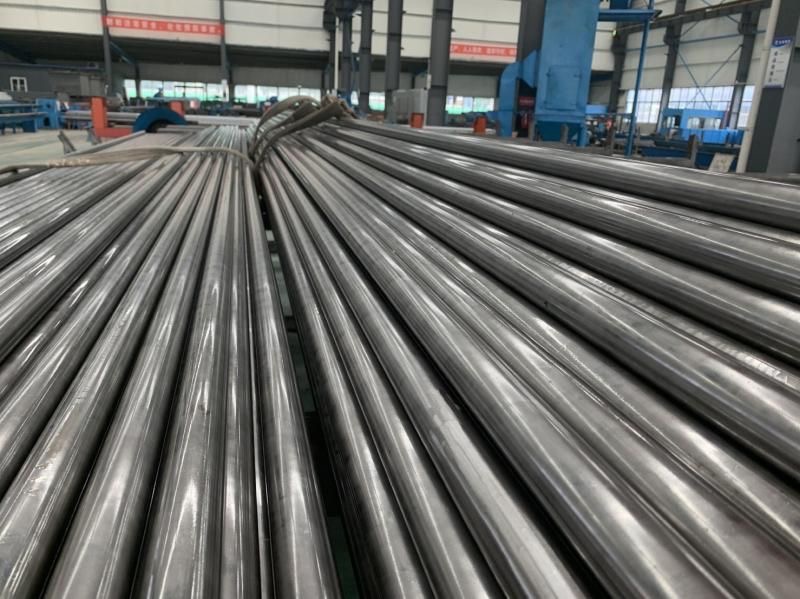
Control of soldering temperature
The welding temperature of straight seam steel pipe is mainly affected by the high-frequency eddy current heat power. When the heat input is insufficient, the heated weld edge will not reach the welding temperature. Finally, adjust the position of the high-frequency induction loop. The farther the induction ring is from the pressure roller, the longer the effective heating time and the larger the area affected by heat. When welding straight seam pipe, the voltage and welding speed need to be adjusted to a certain extent, and there is no need to adjust the parameters after modifying the parameters.The welding standards for repairing straight seam steel pipes are as follows:
1. The surface defects of longitudinally welded steel pipes must be completely eliminated.
2. The total length of the repair weld of each steel pipe of the longitudinally welded steel pipe shall be less than or equal to 5% of the total length of the longitudinally welded steel pipe.
3. The multi-weld defects of longitudinally welded steel pipes with a length less than 100mm should be repaired as a continuous single weld. A single weld of longitudinally welded steel pipes shall be repaired at least twice, and the length of the repaired weld shall be at least 50 mm.
4. The number of repair welds for straight seam welded steel pipes shall not exceed two times each time.
Previous:Alloy pipe VS carbon steel pipe