After the installation of seamless pipes is completed and the pressure test passes, purging work is generally carried out to ensure the internal cleanliness of the pipes. The following are the regulations and requirements for seamless pipe purging:
First, a corresponding purging plan should be prepared before purging seamless pipes. Generally include:
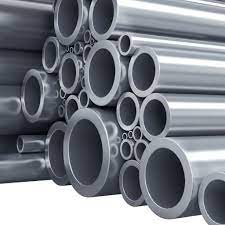
Second, the seamless pipe purging and cleaning method is determined based on the usage requirements of the seamless pipe, the working medium, the pipeline loop, the actual on-site conditions and the degree of oil pollution on the inner surface of the seamless pipe. The method selection should comply with the following construction specifications:
① The pipes to be cleaned are: liquid or gas pipes with a nominal diameter greater than or equal to 600mm.
② Seamless pipes flushed with water are: liquid seamless pipes with a nominal diameter less than 600mm.
③ The seamless pipes purged by compressed air are: gas seamless pipes with a nominal diameter less than 600mm.
④ Steam seamless pipes must be purged with steam. Steam cannot purge non-thermal seamless pipes.
Third, seamless pipe purging sequence and cleaning and discharge requirements:
① Before purging seamless pipes, equipment and seamless pipes that are not allowed to be purged should be isolated, the firmness of seamless pipe supports and hangers should be carefully checked, and any objectionable parts should be fixed.
② Purge in the order of main pipe, branch pipe, and drainage pipe. Clean and discharge oil pollution and do not discharge it anywhere to avoid polluting the environment. The dirt removed by purging shall not enter the seamless pipe that has been purged. After the seamless pipe has passed the purging, other operations that affect the cleaning inside the pipe are not allowed.
③ During steam purging, no flammable objects should be placed on or near the seamless pipe. A safety alert area should be set up during purging, and people are strictly prohibited from standing at the purging port.
Fourth, after the seamless pipe has passed the purge, the "Seamless Pipe System Purge and Cleaning Inspection Record" and the "Seamless Pipe Concealed Engineering (Sealing) Record" should be filled in and jointly inspected by the construction unit, construction unit and supervision unit. sign to confirm.
The following are two seamless pipe purging methods
1. Air purge
① In process seamless pipes, all seamless pipes that transport gas media are generally air purged.
② Air purging should use the large compressor of the production device, or use the large container in the device to store air for intermittent purging; the purging pressure should not exceed the design pressure of the container and seamless pipe, and the flow rate should not be less than 20m /s.
⑤ The angle between the purge port and the ground should be between 30 degrees and 45 degrees. The purge port pipe section and the purged port pipe section must be gently butt welded. The purge port diameter meets the requirements.
⑥ The length of each purge should not exceed 500 meters. When the length of the seamless pipe exceeds 500 meters, it should be purged in sections.
2.Steam purging
① Steam purging is suitable for conveying power steam seamless pipes or thermal seamless pipes. Non-thermal seamless pipes are not suitable for steam purging because problems such as thermal expansion are not considered in the design.
② Steam purging should be carried out with large flow of steam, and the flow rate should not be less than 30m/s.
③ Before steam purging, the pipes should be warmed, drained in time, and the thermal displacement of the seamless pipes should be checked.
First, a corresponding purging plan should be prepared before purging seamless pipes. Generally include:
①Purge procedure, purge method, purge medium, and purge seamless pipe layout;
② Operation and control methods for the pressure, flow rate and flow rate of the purge medium;
③Inspection methods and qualification standards;
④ Safety protection measures, emergency plans, etc. formulated for seamless pipe purging.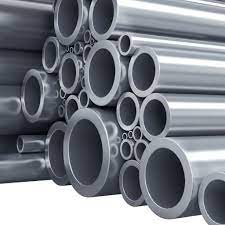
Second, the seamless pipe purging and cleaning method is determined based on the usage requirements of the seamless pipe, the working medium, the pipeline loop, the actual on-site conditions and the degree of oil pollution on the inner surface of the seamless pipe. The method selection should comply with the following construction specifications:
① The pipes to be cleaned are: liquid or gas pipes with a nominal diameter greater than or equal to 600mm.
② Seamless pipes flushed with water are: liquid seamless pipes with a nominal diameter less than 600mm.
③ The seamless pipes purged by compressed air are: gas seamless pipes with a nominal diameter less than 600mm.
④ Steam seamless pipes must be purged with steam. Steam cannot purge non-thermal seamless pipes.
Third, seamless pipe purging sequence and cleaning and discharge requirements:
① Before purging seamless pipes, equipment and seamless pipes that are not allowed to be purged should be isolated, the firmness of seamless pipe supports and hangers should be carefully checked, and any objectionable parts should be fixed.
② Purge in the order of main pipe, branch pipe, and drainage pipe. Clean and discharge oil pollution and do not discharge it anywhere to avoid polluting the environment. The dirt removed by purging shall not enter the seamless pipe that has been purged. After the seamless pipe has passed the purging, other operations that affect the cleaning inside the pipe are not allowed.
③ During steam purging, no flammable objects should be placed on or near the seamless pipe. A safety alert area should be set up during purging, and people are strictly prohibited from standing at the purging port.
Fourth, after the seamless pipe has passed the purge, the "Seamless Pipe System Purge and Cleaning Inspection Record" and the "Seamless Pipe Concealed Engineering (Sealing) Record" should be filled in and jointly inspected by the construction unit, construction unit and supervision unit. sign to confirm.
The following are two seamless pipe purging methods
1. Air purge
① In process seamless pipes, all seamless pipes that transport gas media are generally air purged.
② Air purging should use the large compressor of the production device, or use the large container in the device to store air for intermittent purging; the purging pressure should not exceed the design pressure of the container and seamless pipe, and the flow rate should not be less than 20m /s.
③When purging oil-free seamless pipes, oil-free compressed air should be used.
④ The inspection method for air purging is to install a white cloth or a target plate coated with white paint at the exhaust port of the purged seamless pipe to check that there is no rust, dirt, or other dirt on the target plate within 5 minutes. To be qualified.⑤ The angle between the purge port and the ground should be between 30 degrees and 45 degrees. The purge port pipe section and the purged port pipe section must be gently butt welded. The purge port diameter meets the requirements.
⑥ The length of each purge should not exceed 500 meters. When the length of the seamless pipe exceeds 500 meters, it should be purged in sections.
2.Steam purging
① Steam purging is suitable for conveying power steam seamless pipes or thermal seamless pipes. Non-thermal seamless pipes are not suitable for steam purging because problems such as thermal expansion are not considered in the design.
② Steam purging should be carried out with large flow of steam, and the flow rate should not be less than 30m/s.
③ Before steam purging, the pipes should be warmed, drained in time, and the thermal displacement of the seamless pipes should be checked.
④ Steam purging should follow the steps of flowing steam - slowly heating the pipe - constant temperature for 1 hour - purging - stopping the air to cool down - rewarming the pipe to raise the temperature, constant temperature, and purge for the second time. This cycle is generally no less than 3 times.
⑤ Medium and high-pressure steam seamless pipes and steam turbine inlet seamless pipes should be inspected with a smooth aluminum target plate and a wooden target plate for low-pressure steam. The target plate should be placed at the steam outlet and there should be no dirt on the target plate. To be qualified.