1.What is Spiral Weld Pipe?
Spiral weld pipe, also known as helical welded pipe, is a type of steel pipe characterized by its unique manufacturing process and structural design. In essence, spiral weld pipes are crafted by continuously forming a steel strip into a spiral shape and welding the edges together along the seam. SSAW steel pipe (spiral submerged arc welded steel pipe) is a type pipe of spiral weld pipe.2.What is ERW Pipe?
Electric Resistance Welded (ERW) pipe is a type of steel pipe manufactured through the process of electric resistance welding. This method involves passing a high-frequency electrical current through the edges of a steel strip, causing them to heat up and form a weld seam.3.Spiral Weld vs ERW Pipe
(1)Manufacturing Process
A.ERW Pipe Manufacturing Process:Electric Resistance Welded (ERW) pipes are produced using a relatively straightforward yet efficient manufacturing process. It begins with a flat steel strip that is unwound from coils and passes through a series of rollers to ensure uniform thickness. The strip then enters the welding chamber, where high-frequency electrical currents are applied to the edges of the strip. This localized heating causes the edges to melt and fuse together, forming a continuous weld seam. Finally, the welded pipe is cut to the desired length and undergoes various finishing processes, such as straightening and inspection.
B.Spiral Weld Pipe Manufacturing Process:
Spiral weld pipes are crafted using a more intricate manufacturing process known as spiral welding. It starts with a flat steel strip that is fed into a machine equipped with forming rolls. As the strip progresses through the machine, it is gradually formed into a spiral shape, with each turn overlapping the previous one. Simultaneously, the edges of the strip are welded together using either submerged arc welding (SAW) or continuous welding techniques. This results in a seamless and robust weld seam that runs the length of the pipe.
Comparative Analysis:
When comparing the manufacturing processes of ERW and Spiral Weld pipes, several factors come into play. Firstly, the ERW process is more straightforward and requires fewer steps compared to spiral welding. This contributes to faster production times and lower manufacturing costs for ERW pipes. Additionally, ERW pipes exhibit excellent dimensional accuracy and uniformity, thanks to the precise control offered by the welding process.
On the other hand, spiral welding allows for the creation of pipes with larger diameters and thicker walls compared to ERW pipes. This makes spiral weld pipes well-suited for applications requiring robust structural integrity and high-pressure containment. Furthermore, the continuous weld seam in spiral weld pipes provides enhanced resistance to bending and torsional stresses, making them ideal for installations in challenging terrain.
(2) Pressure Resistance
A.ERW Pipe Pressure Resistance:Electric Resistance Welded (ERW) pipes are renowned for their exceptional pressure resistance capabilities. The seamless weld seam created during the manufacturing process ensures uniform strength and integrity along the entire length of the pipe. This makes ERW pipes suitable for applications requiring reliable containment of high-pressure fluids, such as water distribution systems and oil and gas pipelines.
B.Spiral Weld Pipe Pressure Resistance:
Similarly, Spiral Weld pipes boast impressive pressure resistance characteristics. The continuous weld seam that runs along the spiral shape of the pipe provides robust structural support and enhances its ability to withstand internal pressure. Spiral weld pipes are commonly utilized in applications where high-pressure containment is critical, such as underground drainage systems and industrial piping networks.
Comparative Analysis:
When comparing the pressure resistance of ERW and Spiral Weld pipes, both types demonstrate commendable performance in high-pressure environments. The seamless weld seam in ERW pipes ensures consistent strength and reliability, while the helical weld seam in spiral weld pipes provides added reinforcement against internal pressure.
However, it's worth noting that spiral weld pipes offer certain advantages in specific scenarios. The helical design distributes stress more evenly along the length of the pipe, reducing the risk of localized failures under extreme pressure conditions. Additionally, spiral weld pipes can accommodate larger diameters and thicker walls compared to ERW pipes, further enhancing their pressure resistance capabilities.
(3) Performance
A.Performance Attributes of ERW Pipes:Dimensional Accuracy
ERW pipes are known for their precise dimensional accuracy, thanks to the uniformity achieved during the manufacturing process. This ensures compatibility with fittings and reduces the need for adjustments during installation.
Smooth Internal Surface
The electric resistance welding process results in a smooth internal surface finish, minimizing frictional losses and facilitating efficient fluid flow. This makes ERW pipes suitable for applications requiring high flow rates and minimal pressure drop.
Consistent Quality
ERW pipes exhibit consistent quality and structural integrity throughout their length. The seamless weld seam ensures uniform strength, reducing the risk of defects or weak points that could compromise performance.
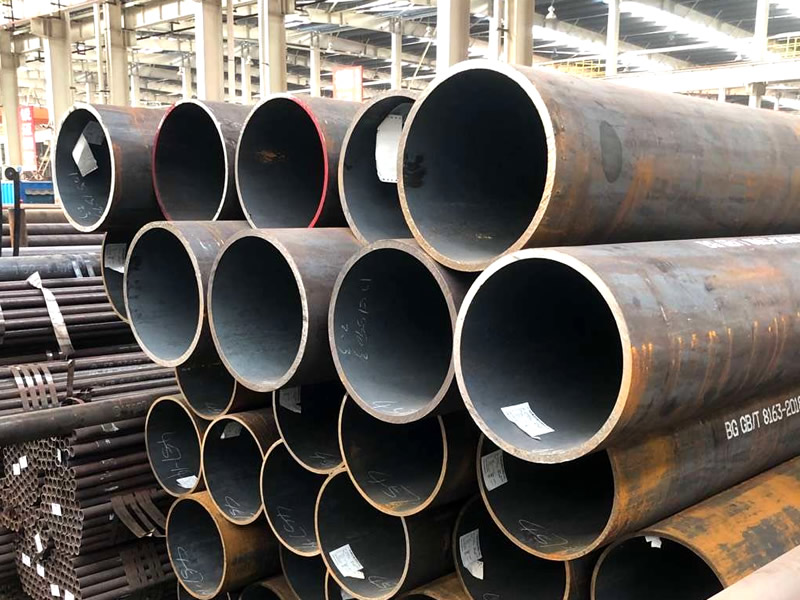
Versatility
ERW pipes are highly versatile and can be produced in a wide range of sizes, wall thicknesses, and grades to suit diverse application requirements. This adaptability makes them suitable for various industries and sectors.
B.Performance Attributes of Spiral Weld Pipes:
Enhanced Structural Integrity
Spiral weld pipes boast enhanced structural integrity due to the helical design of the weld seam. This provides added reinforcement against bending, torsional stresses, and external loads, making them suitable for installations in challenging terrain.
Large Diameter Capability
Spiral weld pipes can accommodate larger diameters and thicker walls compared to ERW pipes, making them ideal for applications requiring robust structural support and high-pressure containment.
Uniform Stress Distribution
The helical weld seam in spiral weld pipes distributes stress more evenly along the length of the pipe, reducing the risk of localized failures under extreme conditions. This ensures reliable performance and long-term durability in demanding environments.
(4)Cost
A.Manufacturing CostsThe manufacturing process of ERW pipes is relatively straightforward and efficient, resulting in lower production costs compared to Spiral Weld pipes. However, Spiral Weld pipes can accommodate larger diameters and thicker walls, which may offset the higher manufacturing costs.
B.Material Costs
The cost of raw materials, such as steel coils, significantly impacts the overall cost of both ERW and Spiral Weld pipes. Price fluctuations in the steel market can influence material costs and ultimately affect the pricing of the pipes.
C.Production Efficiency
ERW pipes offer higher production efficiency and faster manufacturing times due to the simplicity of the welding process. This can translate to lower labor costs and increased productivity compared to Spiral Weld pipes.
D.Transportation and Handling
The transportation and handling costs associated with ERW and Spiral Weld pipes depend on factors such as pipe size, weight, and distance traveled. Larger diameter Spiral Weld pipes may incur higher transportation costs due to their size and weight.
E.Installation Costs
The installation process for both ERW and Spiral Weld pipes involves similar procedures, including excavation, trenching, and pipe laying. However, the larger diameter and thicker walls of Spiral Weld pipes may require specialized equipment and additional labor, potentially increasing installation costs.
4.Application Considerations and Conclusion
In this final section, we'll discuss important considerations when selecting between Electric Resistance Welded (ERW) and Spiral Welded pipes for specific applications and provide a concluding summary of key points.(1)Factors to Consider
A.Pipe Size and DiameterThe size and diameter requirements of the project play a crucial role in determining the most suitable pipe type. ERW pipes may be more cost-effective for smaller diameter applications, while Spiral Weld pipes offer advantages in larger diameter installations.
B.Pressure Rating
Consider the pressure rating required for the application, as both ERW and Spiral Weld pipes exhibit commendable pressure resistance capabilities. Spiral Weld pipes are particularly well-suited for high-pressure environments due to their robust construction.C.Environmental Conditions
uate the environmental conditions of the installation site, including soil type, terrain, and exposure to corrosive elements. Spiral Weld pipes offer enhanced resistance to external stresses and corrosion, making them suitable for challenging environments.D.Budget Constraints
Take into account budget constraints and project limitations when selecting between ERW and Spiral Weld pipes. While ERW pipes may offer cost advantages in certain scenarios, Spiral Weld pipes provide long-term durability and performance benefits.(2)Summary of Key Differences and Advantages:
A.ERW Pipes
Known for their precise dimensional accuracy, smooth internal surface finish, and cost-effectiveness. Suitable for a wide range of applications, including water distribution systems, structural frameworks, and HVAC systems.
B.Spiral Weld Pipes
Boast enhanced structural integrity, resistance to high-pressure environments, and long-term durability. Ideal for applications requiring robust structural support, such as oil and gas pipelines, underground drainage systems, and industrial piping networks.
(3)Recommendations:
A.uate Project Requirements
Assess project requirements, including pipe size, pressure rating, environmental conditions, and budget constraints.
B.Select the Most Suitable Pipe
Based on the uation, select the most suitable pipe type that meets the project specifications and performance criteria.
C.Consult with Experts
Consider consulting with pipe manufacturers, engineers, and industry experts to ensure the optimal selection of pipe type for the project.
5.Conclusion
In conclusion, the choice between Electric Resistance Welded (ERW) and Spiral Welded pipes depends on various factors, including project requirements, environmental conditions, and budget constraints. Both types of pipes offer unique advantages and are suitable for different applications. By carefully uating these factors and consulting with experts, engineers and contractors can make informed decisions when selecting the most suitable pipe type for their projects.
Previous:sheet pile soilless beton
Next:OCTG pipe meaning