The weld seam of the high-frequency electric resistance welded pipe (ERW pipe) is formed by melting the base material of the steel strip body, and its mechanical strength is better than that of ordinary welded pipes. Smooth appearance, high precision, low cost and small weld reinforcement, which is beneficial to the coating of 3PE anti-corrosion coating. The welding method of high frequency welded steel pipe and submerged arc welded pipe (SSAW pipe or LSAW pipe) is significantly different. Since welding is completed instantaneously at high speed, the difficulty of ensuring welding quality is much higher than that of submerged arc welding.
The influence of operation on welding quality in high frequency welded pipe production
1 heat input
When the input heat is insufficient, the heated edge cannot reach the welding temperature, and still maintains a solid structure and cannot be welded, forming welding cracks. When the input heat is large, the edge to be heated exceeds the welding temperature and is prone to overheating, even overburning, and cracking after being stressed. When the input heat is too large, the welding temperature is too high, causing the weld to break down, causing molten metal to splash and forming holes. The melting and welding temperature is generally 1350~1400°C.
2 welding pressure
Welding pressure is one of the main parameters of the welding process. After the two edges of the tube blank are heated to the welding temperature, common metal grains are formed under the action of extrusion force, that is, mutual crystallization and welding. The size of the welding pressure affects the strength and toughness of the weld. If the welding pressure applied is small, the metal welding edges cannot be fully pressed, and the non-metallic inclusions and metal oxides remaining in the weld are not easy to discharge due to the low pressure, the strength of the weld is reduced, and it is easy to crack after being stressed. When the pressure is too high, most of the metal that reaches the welding temperature is extruded, which not only reduces the strength of the weld, but also produces defects such as excessive internal and external burrs or lap welding. Therefore, the optimum welding pressure corresponding to it should be obtained in practice according to different varieties and specifications. According to practical experience, the unit welding pressure is generally 20~40MPa.
3 welding speed
The welding speed is also one of the main parameters of the welding process, which is related to the heating system, the deformation speed of the weld and the mutual crystallization speed. In the case of high-frequency welded pipes, the welding quality improves with the increase of welding speed. This is because the shortening of the heating time narrows the width of the edge heating zone and shortens the time for forming metal oxides. If the welding speed is reduced, not only the heating zone becomes wider, but also the width of the melting zone changes with the input heat, resulting in larger internal burrs. In low-speed welding, less heat input makes welding difficult, and defects are likely to occur if the specified value is not met.
4 opening angle
The opening angle refers to the angle between the two edges of the tube blank before the extrusion roller. The size of the opening angle is related to the stability of the firing process and has a great influence on the welding quality.
When the opening angle is reduced, the distance between the edges is also reduced, so that the proximity effect is strengthened. Under the same conditions, the heating temperature of the edge can be increased, thereby increasing the welding speed. If the opening angle is too small, the distance from the meeting point to the centerline of the squeeze roller will be lengthened, resulting in the edge not being squeezed at the highest temperature, which will reduce the welding quality and increase the power consumption.
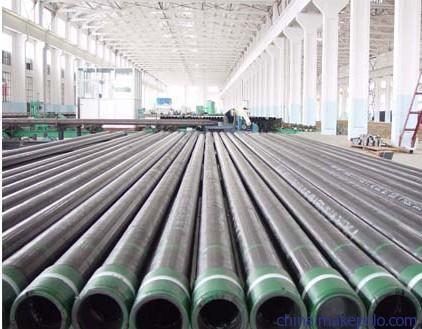
5 Placement of sensors and resistors
(1) Placement of the sensor
The placement of the sensor has a great influence on the welding quality. When it is far away from the center line of the extrusion roller, the effective heating time is long and the heat-affected zone is wide, which reduces the weld strength. Conversely, insufficient edge heating also reduces the strength of the weld. The sensor should be placed concentrically with the tube, and the distance between its front end and the centerline of the extrusion roller is about equal to or less than the tube diameter (small tube is 1.5 times the tube diameter) for the best condition.
(2) Placement of the resistor
The placement position of the impedance (magnetic rod) not only has a great influence on the welding speed, but also has an influence on the welding quality.
6 Geometric size and shape requirements of tube blanks
(1) Geometric dimensions of welded pipe blanks
The width and thickness of the tube blank have large deviations, which will change the heating temperature and extrusion amount of the edge. Qualified products must require the width and thickness of the tube blank to be within the tolerance range.
(2) The shape and connection form of the tube blank
If there are deflection, camber and corrugation on the edge of the tube blank, it will deviate from the center of the pass when passing through the forming machine, causing both sides of the strip to bend. Poor adjustment of rolls will also cause defects such as strip deviation or tube billet distortion, which will affect the welding quality or cause welding failure at all.
When the two ends of the tube blank are welded, the full thickness of the two ends should be connected, and the two edges of the tube blank should not only be straight but also parallel. When slitting the strip steel, the gap between the cutting blades of the disk is too large or the blade wears seriously, resulting in excessive burrs on the edge of the strip steel, and cracks after welding are also prone to occur.
7 Strip edge quality
The quality of the edge of the strip will affect the heating result of the high-frequency induction, thereby affecting the quality of the weld. After the tube blank is formed, the two edges of the strip should be parallel, otherwise there will be a sharp corner effect, which will affect the quality of the weld.
The influence of operation on welding quality in high frequency welded pipe production
1 heat input
When the input heat is insufficient, the heated edge cannot reach the welding temperature, and still maintains a solid structure and cannot be welded, forming welding cracks. When the input heat is large, the edge to be heated exceeds the welding temperature and is prone to overheating, even overburning, and cracking after being stressed. When the input heat is too large, the welding temperature is too high, causing the weld to break down, causing molten metal to splash and forming holes. The melting and welding temperature is generally 1350~1400°C.
2 welding pressure
Welding pressure is one of the main parameters of the welding process. After the two edges of the tube blank are heated to the welding temperature, common metal grains are formed under the action of extrusion force, that is, mutual crystallization and welding. The size of the welding pressure affects the strength and toughness of the weld. If the welding pressure applied is small, the metal welding edges cannot be fully pressed, and the non-metallic inclusions and metal oxides remaining in the weld are not easy to discharge due to the low pressure, the strength of the weld is reduced, and it is easy to crack after being stressed. When the pressure is too high, most of the metal that reaches the welding temperature is extruded, which not only reduces the strength of the weld, but also produces defects such as excessive internal and external burrs or lap welding. Therefore, the optimum welding pressure corresponding to it should be obtained in practice according to different varieties and specifications. According to practical experience, the unit welding pressure is generally 20~40MPa.
3 welding speed
The welding speed is also one of the main parameters of the welding process, which is related to the heating system, the deformation speed of the weld and the mutual crystallization speed. In the case of high-frequency welded pipes, the welding quality improves with the increase of welding speed. This is because the shortening of the heating time narrows the width of the edge heating zone and shortens the time for forming metal oxides. If the welding speed is reduced, not only the heating zone becomes wider, but also the width of the melting zone changes with the input heat, resulting in larger internal burrs. In low-speed welding, less heat input makes welding difficult, and defects are likely to occur if the specified value is not met.
4 opening angle
The opening angle refers to the angle between the two edges of the tube blank before the extrusion roller. The size of the opening angle is related to the stability of the firing process and has a great influence on the welding quality.
When the opening angle is reduced, the distance between the edges is also reduced, so that the proximity effect is strengthened. Under the same conditions, the heating temperature of the edge can be increased, thereby increasing the welding speed. If the opening angle is too small, the distance from the meeting point to the centerline of the squeeze roller will be lengthened, resulting in the edge not being squeezed at the highest temperature, which will reduce the welding quality and increase the power consumption.
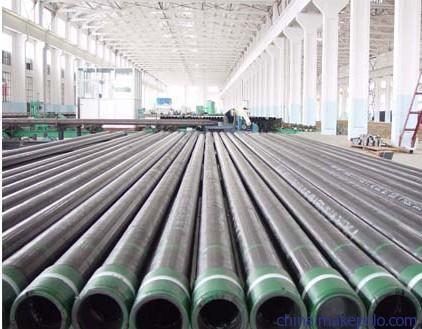
5 Placement of sensors and resistors
(1) Placement of the sensor
The placement of the sensor has a great influence on the welding quality. When it is far away from the center line of the extrusion roller, the effective heating time is long and the heat-affected zone is wide, which reduces the weld strength. Conversely, insufficient edge heating also reduces the strength of the weld. The sensor should be placed concentrically with the tube, and the distance between its front end and the centerline of the extrusion roller is about equal to or less than the tube diameter (small tube is 1.5 times the tube diameter) for the best condition.
(2) Placement of the resistor
The placement position of the impedance (magnetic rod) not only has a great influence on the welding speed, but also has an influence on the welding quality.
6 Geometric size and shape requirements of tube blanks
(1) Geometric dimensions of welded pipe blanks
The width and thickness of the tube blank have large deviations, which will change the heating temperature and extrusion amount of the edge. Qualified products must require the width and thickness of the tube blank to be within the tolerance range.
(2) The shape and connection form of the tube blank
If there are deflection, camber and corrugation on the edge of the tube blank, it will deviate from the center of the pass when passing through the forming machine, causing both sides of the strip to bend. Poor adjustment of rolls will also cause defects such as strip deviation or tube billet distortion, which will affect the welding quality or cause welding failure at all.
When the two ends of the tube blank are welded, the full thickness of the two ends should be connected, and the two edges of the tube blank should not only be straight but also parallel. When slitting the strip steel, the gap between the cutting blades of the disk is too large or the blade wears seriously, resulting in excessive burrs on the edge of the strip steel, and cracks after welding are also prone to occur.
7 Strip edge quality
The quality of the edge of the strip will affect the heating result of the high-frequency induction, thereby affecting the quality of the weld. After the tube blank is formed, the two edges of the strip should be parallel, otherwise there will be a sharp corner effect, which will affect the quality of the weld.