A welded tube making line, also known as a tube mill, is a crucial component in the manufacturing process of welded steel tubes and pipes. These machines are designed to transform flat strips or coils of steel into high-quality welded tubes of various sizes and shapes. The production process involves several stages, including material preparation, forming, welding, sizing, cutting, and finishing. In this comprehensive guide, we will delve into the key components, processes, and functionalities of a welded tube making line.
1.Overview of the Production Process
The production process of a welded tube making line can be summarized in the following stages:
(1)Uncoiling and Straightening
The process begins with uncoiling the steel strip or coil to feed it into the tube mill. This is followed by straightening the strip to ensure uniformity and precision during subsequent operations.
(2)Forming
The steel strip is then passed through a series of forming stands, where it is gradually shaped into a cylindrical form using sets of rolls and forming stands. This process imparts the desired cross-sectional profile to the tube.
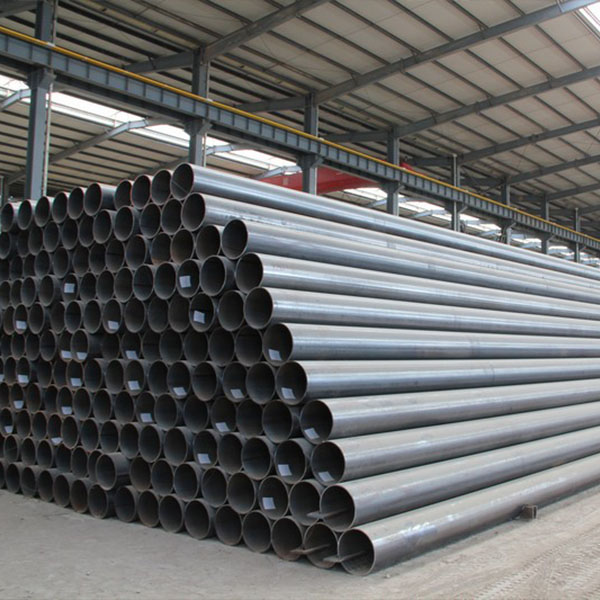
(3)Welding
Once the tube is formed, the edges of the strip are heated and fused together to create a continuous weld. Various welding techniques such as high-frequency induction welding or TIG welding may be employed based on the specific requirements.
(4)Sizing and Shaping
After welding, the tube passes through sizing stands that help to achieve the final dimensions and wall thickness. Sizing and shaping operations are critical for ensuring dimensional accuracy and consistency.
(5)Cut-off and Finishing
The continuous tube is cut into individual lengths as per the required specifications. Additional finishing processes such as end facing, deburring, and surface treatment may also be carried out to meet quality standards.
2.Key Components of a Welded Tube Making Line
A typical welded tube making line comprises several essential components that work together to produce high-quality welded tubes. Some of the key components include:
(1)Uncoiler
This component feeds the steel strip or coil into the tube mill by unwinding the material in a controlled manner. It ensures a continuous supply of raw material for the production process.
(2)Forming Stands
Forming stands consist of a series of roll sets that gradually shape the steel strip into a tubular form. These rolls are designed to provide the required diameter, wall thickness, and roundness to the tube.
(3)Welding Section
The welding section utilizes advanced welding techniques to join the edges of the steel strip, creating a continuous weld along the length of the tube. This section includes systems for edge preparation, heating, and welding.
(4)Sizing Section
The sizing section of the tube mill consists of multiple sets of rolls that accurately size and shape the welded tube to meet the specified dimensions. This stage plays a crucial role in achieving the desired tolerances and surface finish.
(5)Cut-off Unit
The cut-off unit is responsible for cutting the continuous tube into individual lengths according to the desired specifications. Various cutting methods such as cold saw cutting or flying cutoff may be employed for precise and efficient tube cutting.
(6)Finishing Equipment
Finishing equipment such as end facers, deburring tools, and surface treatment units are utilized to refine the end product, ensuring smooth edges, clean surfaces, and the required surface finish.
(7)Functionalities and Control Systems
Modern welded tube making lines are equipped with advanced functionalities and control systems to optimize production efficiency and product quality. Some of the key functionalities and control systems include:
a.Automation and Integration
Automated systems control the entire tube making process, from material handling to final product inspection. Integration with computerized control systems allows for real-time monitoring and adjustment of various parameters.
b.Precision Tooling
Precision tooling and quick-change systems enable rapid adjustments for different tube sizes and profiles, minimizing downtime and enhancing flexibility in production.
c.Welding Technology
Utilization of advanced welding technologies such as high-frequency induction welding, laser welding, or plasma welding ensures robust and high-quality welds with minimal heat-affected zones.
d.Quality Control and Inspection
Inline inspection systems, including ultrasonic testing, eddy current testing, and laser measurement devices, are integrated to monitor weld integrity, dimensions, and surface characteristics for adherence to quality standards.
e.Data Acquisition and Analysis
Data acquisition systems capture vital process data, which is then analyzed to optimize production parameters, identify trends, and detect potential issues for proactive maintenance.
1.Overview of the Production Process
The production process of a welded tube making line can be summarized in the following stages:
(1)Uncoiling and Straightening
The process begins with uncoiling the steel strip or coil to feed it into the tube mill. This is followed by straightening the strip to ensure uniformity and precision during subsequent operations.
(2)Forming
The steel strip is then passed through a series of forming stands, where it is gradually shaped into a cylindrical form using sets of rolls and forming stands. This process imparts the desired cross-sectional profile to the tube.
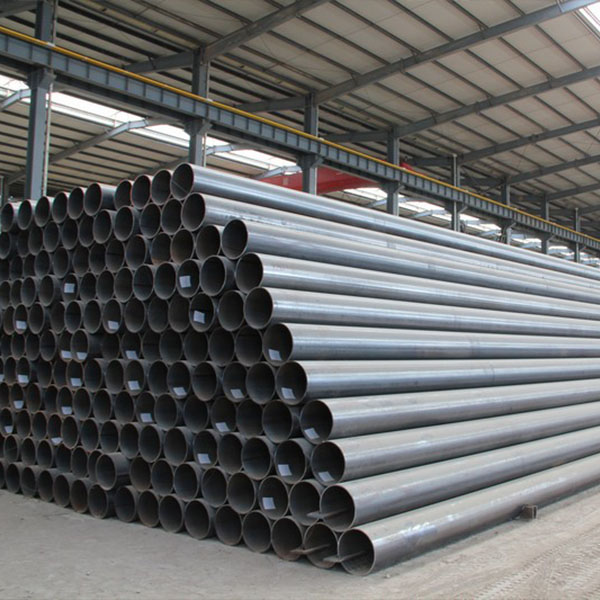
(3)Welding
Once the tube is formed, the edges of the strip are heated and fused together to create a continuous weld. Various welding techniques such as high-frequency induction welding or TIG welding may be employed based on the specific requirements.
(4)Sizing and Shaping
After welding, the tube passes through sizing stands that help to achieve the final dimensions and wall thickness. Sizing and shaping operations are critical for ensuring dimensional accuracy and consistency.
(5)Cut-off and Finishing
The continuous tube is cut into individual lengths as per the required specifications. Additional finishing processes such as end facing, deburring, and surface treatment may also be carried out to meet quality standards.
2.Key Components of a Welded Tube Making Line
A typical welded tube making line comprises several essential components that work together to produce high-quality welded tubes. Some of the key components include:
(1)Uncoiler
This component feeds the steel strip or coil into the tube mill by unwinding the material in a controlled manner. It ensures a continuous supply of raw material for the production process.
(2)Forming Stands
Forming stands consist of a series of roll sets that gradually shape the steel strip into a tubular form. These rolls are designed to provide the required diameter, wall thickness, and roundness to the tube.
(3)Welding Section
The welding section utilizes advanced welding techniques to join the edges of the steel strip, creating a continuous weld along the length of the tube. This section includes systems for edge preparation, heating, and welding.
(4)Sizing Section
The sizing section of the tube mill consists of multiple sets of rolls that accurately size and shape the welded tube to meet the specified dimensions. This stage plays a crucial role in achieving the desired tolerances and surface finish.
(5)Cut-off Unit
The cut-off unit is responsible for cutting the continuous tube into individual lengths according to the desired specifications. Various cutting methods such as cold saw cutting or flying cutoff may be employed for precise and efficient tube cutting.
(6)Finishing Equipment
Finishing equipment such as end facers, deburring tools, and surface treatment units are utilized to refine the end product, ensuring smooth edges, clean surfaces, and the required surface finish.
(7)Functionalities and Control Systems
Modern welded tube making lines are equipped with advanced functionalities and control systems to optimize production efficiency and product quality. Some of the key functionalities and control systems include:
a.Automation and Integration
Automated systems control the entire tube making process, from material handling to final product inspection. Integration with computerized control systems allows for real-time monitoring and adjustment of various parameters.
b.Precision Tooling
Precision tooling and quick-change systems enable rapid adjustments for different tube sizes and profiles, minimizing downtime and enhancing flexibility in production.
c.Welding Technology
Utilization of advanced welding technologies such as high-frequency induction welding, laser welding, or plasma welding ensures robust and high-quality welds with minimal heat-affected zones.
d.Quality Control and Inspection
Inline inspection systems, including ultrasonic testing, eddy current testing, and laser measurement devices, are integrated to monitor weld integrity, dimensions, and surface characteristics for adherence to quality standards.
e.Data Acquisition and Analysis
Data acquisition systems capture vital process data, which is then analyzed to optimize production parameters, identify trends, and detect potential issues for proactive maintenance.