Welding crack is the most common serious defect in steel pipe welding (such as seamless pipe, welded steel tube). Under the joint action of welding stress and other brittle factors, the bonding force of metal atoms in the local area of the welded joint is destroyed and the gap formed by the new interface is formed. It is characterized by a sharp notch and a large aspect ratio. Cracks affect the safe use of welded steel pipes and are very dangerous process defects.
Welding cracks not only occur during the welding process, some have a certain incubation period, and some occur during the reheating process after welding. Welding cracks can be classified in different ways according to their location, size, cause of formation and mechanism. According to the conditions of crack formation, it can be divided into four categories: hot crack, cold crack, reheat crack and lamellar tear.
Hot crack
It is mostly produced at high temperatures close to the solidus line and has the characteristics of distribution along the grain boundary; but sometimes it can also be formed along the "polygonal boundary" at a temperature lower than the solidus line. Hot cracks usually occur in the weld metal, but may also form in the welded metal (base metal) near the welding fusion line. According to the characteristics of its formation process, it can be divided into the following three situations.
(1) Crystalline cracks
Produced in the "brittle temperature" interval at the end of the weld metal crystallization process, at this time there is a thin liquid layer between the grains. Therefore, the plasticity of the metal is extremely low, and when the tensile deformation caused by the uneven shrinkage of cooling exceeds the allowable value, the liquid layer cracks along the grain boundary. The main metallurgical measures to eliminate crystallization cracks are to adjust the composition, refine the grains, and strictly control the impurity elements that form low melting point eutectics, etc., so as to improve the plasticity of the material in the brittle temperature range. In addition, the internal tensile deformation in this temperature range should be minimized from the design and process.
(2) Liquefaction cracks
It is mainly produced in the base metal near the weld fusion line, and sometimes in the first weld bead of multi-layer welding. The reason for the formation is due to the local melting along the grain boundary in the metal outside the weld fusion line under the action of welding heat, and the cracking of the liquefied layer along the grain boundary caused by subsequent cooling and shrinkage. The principle of preventing such cracks is to strictly control the impurity content, reasonably select welding materials, and minimize the effect of welding heat.
(3) Multilateral cracks
formed at temperatures below the solidus. Its characteristic is that it is distributed along the "polygonal boundary" and has no obvious relationship with the primary crystallization grain boundary. The way to eliminate this defect is to add alloy elements that can increase the activation energy of polygonization, such as adding W, Mo, Ta, etc. to Ni-Cr alloys; on the other hand, it is to reduce overheating and welding stress during welding.
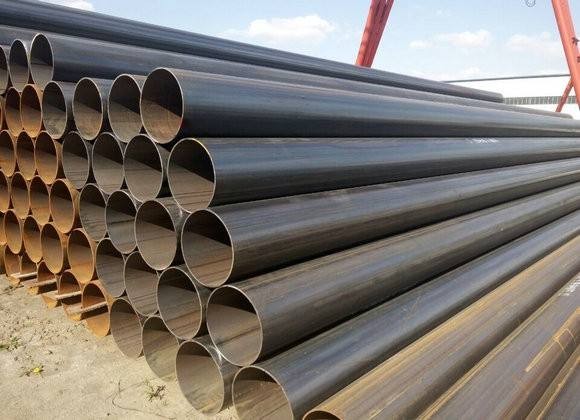
Cold crack
According to the main cause, it can be divided into quenching cracks, hydrogen-induced delayed cracks and deformation cracks.
(1) Quenching crack
Cracks occur near the martensitic transformation point (Ms) of the steel pipe or below 200°C. It mainly occurs in medium and high-carbon steel pipes, low-alloy high-strength steel pipes, and titanium alloy steel pipes, etc., and the main parts are in the heat-affected zone and the weld metal. The crack direction is intergranular or transgranular.
The main factors that form cold cracks are:
①The hydrogen content of the steel pipe is high;
② Brittle tissue or tissue sensitive to hydrogen embrittlement;
③ Welding restraint stress (or strain).
(2) Hydrogen-induced delayed cracking
During the welding process, the hydrogen dissolved in the weld metal diffuses and segregates to the heat-affected zone, especially enriches in the triaxial tensile stress concentration zone that is easy to crack, causing hydrogen embrittlement. That is to reduce the critical stress of the metal at the opening position (or crack front), and when the local stress here exceeds the critical stress, it will cause cracking.
Preventive measures include:
① Reduce the hydrogen content in the weld, such as using low-hydrogen electrodes, strictly drying welding materials, etc.;
②Reasonable preheating and afterheating;
③ Choose raw materials with low carbon equivalent;
④ Reduce restraint stress and avoid stress concentration.
(3) Deformation cracks
The formation of such cracks is not necessarily due to the high hydrogen content. In the case of strain concentration in multi-layer welds or fillet welds, the tensile strain exceeds the plastic deformation capacity of the metal.
Reheat crack
Produced in the reheating process of some low-alloy high-strength steel pipes, pearlitic heat-resistant steel pipes, austenitic stainless steel pipes, and nickel-based alloy steel pipes after welding. Such cracks have the characteristics of intergranular cracking, and all occur in the coarse-grained zone of the heat-affected zone with severe stress concentration. In order to prevent the occurrence of such cracks, firstly, materials with low reheating crack sensitivity should be selected during design, and secondly, internal stress and stress concentration problems near the fracture area should be minimized in terms of technology.
Lamellar tear
Mainly occurs in thick plate fillet welding. It is characterized by being parallel to the surface of the steel plate and developing in a stepped shape along the rolling direction. Such cracks are often not limited to the heat-affected zone, but can also appear in the base metal away from the surface. The main reason is that due to the layered distribution of non-metallic inclusions in the metal, the plasticity of the steel plate along the thickness direction is lower than that along the rolling direction. In addition, due to the large welding stress in the direction of plate thickness during fillet welding of thick plates, lamellar tearing is caused. To prevent such defects, the quantity and distribution of inclusions should be strictly controlled during the metallurgical process. In addition, improving the joint design and welding process also has a certain effect.
Welding cracks not only occur during the welding process, some have a certain incubation period, and some occur during the reheating process after welding. Welding cracks can be classified in different ways according to their location, size, cause of formation and mechanism. According to the conditions of crack formation, it can be divided into four categories: hot crack, cold crack, reheat crack and lamellar tear.
Hot crack
It is mostly produced at high temperatures close to the solidus line and has the characteristics of distribution along the grain boundary; but sometimes it can also be formed along the "polygonal boundary" at a temperature lower than the solidus line. Hot cracks usually occur in the weld metal, but may also form in the welded metal (base metal) near the welding fusion line. According to the characteristics of its formation process, it can be divided into the following three situations.
(1) Crystalline cracks
Produced in the "brittle temperature" interval at the end of the weld metal crystallization process, at this time there is a thin liquid layer between the grains. Therefore, the plasticity of the metal is extremely low, and when the tensile deformation caused by the uneven shrinkage of cooling exceeds the allowable value, the liquid layer cracks along the grain boundary. The main metallurgical measures to eliminate crystallization cracks are to adjust the composition, refine the grains, and strictly control the impurity elements that form low melting point eutectics, etc., so as to improve the plasticity of the material in the brittle temperature range. In addition, the internal tensile deformation in this temperature range should be minimized from the design and process.
(2) Liquefaction cracks
It is mainly produced in the base metal near the weld fusion line, and sometimes in the first weld bead of multi-layer welding. The reason for the formation is due to the local melting along the grain boundary in the metal outside the weld fusion line under the action of welding heat, and the cracking of the liquefied layer along the grain boundary caused by subsequent cooling and shrinkage. The principle of preventing such cracks is to strictly control the impurity content, reasonably select welding materials, and minimize the effect of welding heat.
(3) Multilateral cracks
formed at temperatures below the solidus. Its characteristic is that it is distributed along the "polygonal boundary" and has no obvious relationship with the primary crystallization grain boundary. The way to eliminate this defect is to add alloy elements that can increase the activation energy of polygonization, such as adding W, Mo, Ta, etc. to Ni-Cr alloys; on the other hand, it is to reduce overheating and welding stress during welding.
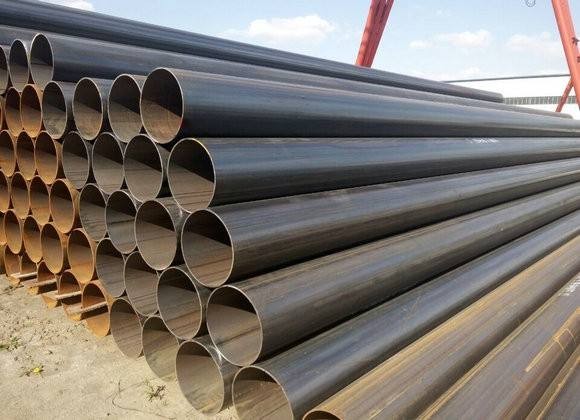
Cold crack
According to the main cause, it can be divided into quenching cracks, hydrogen-induced delayed cracks and deformation cracks.
(1) Quenching crack
Cracks occur near the martensitic transformation point (Ms) of the steel pipe or below 200°C. It mainly occurs in medium and high-carbon steel pipes, low-alloy high-strength steel pipes, and titanium alloy steel pipes, etc., and the main parts are in the heat-affected zone and the weld metal. The crack direction is intergranular or transgranular.
The main factors that form cold cracks are:
①The hydrogen content of the steel pipe is high;
② Brittle tissue or tissue sensitive to hydrogen embrittlement;
③ Welding restraint stress (or strain).
(2) Hydrogen-induced delayed cracking
During the welding process, the hydrogen dissolved in the weld metal diffuses and segregates to the heat-affected zone, especially enriches in the triaxial tensile stress concentration zone that is easy to crack, causing hydrogen embrittlement. That is to reduce the critical stress of the metal at the opening position (or crack front), and when the local stress here exceeds the critical stress, it will cause cracking.
Preventive measures include:
① Reduce the hydrogen content in the weld, such as using low-hydrogen electrodes, strictly drying welding materials, etc.;
②Reasonable preheating and afterheating;
③ Choose raw materials with low carbon equivalent;
④ Reduce restraint stress and avoid stress concentration.
(3) Deformation cracks
The formation of such cracks is not necessarily due to the high hydrogen content. In the case of strain concentration in multi-layer welds or fillet welds, the tensile strain exceeds the plastic deformation capacity of the metal.
Reheat crack
Produced in the reheating process of some low-alloy high-strength steel pipes, pearlitic heat-resistant steel pipes, austenitic stainless steel pipes, and nickel-based alloy steel pipes after welding. Such cracks have the characteristics of intergranular cracking, and all occur in the coarse-grained zone of the heat-affected zone with severe stress concentration. In order to prevent the occurrence of such cracks, firstly, materials with low reheating crack sensitivity should be selected during design, and secondly, internal stress and stress concentration problems near the fracture area should be minimized in terms of technology.
Lamellar tear
Mainly occurs in thick plate fillet welding. It is characterized by being parallel to the surface of the steel plate and developing in a stepped shape along the rolling direction. Such cracks are often not limited to the heat-affected zone, but can also appear in the base metal away from the surface. The main reason is that due to the layered distribution of non-metallic inclusions in the metal, the plasticity of the steel plate along the thickness direction is lower than that along the rolling direction. In addition, due to the large welding stress in the direction of plate thickness during fillet welding of thick plates, lamellar tearing is caused. To prevent such defects, the quantity and distribution of inclusions should be strictly controlled during the metallurgical process. In addition, improving the joint design and welding process also has a certain effect.