Spiral steel pipe (SSAW pipe) is a steel strip made of low-carbon carbon structural steel or low-alloy structural steel, rolled into a tubular shape according to a certain forming angle, and then welded and sewn. Spiral welded pipes are mainly used for the transmission pipelines of petroleum crude oil and natural gas, and their specifications are expressed by the outer diameter multiplied by the wall thickness. Spiral welded pipe plays an important role in gas transmission and transportation.
Welding defect and process analysis of spiral steel pipe
1. Pore defects
In the actual operation of spiral steel pipes, in the welding of metals, the most frequent defect is the defect of air holes. If there is moisture or rust in the welded part, the probability of serious porosity defects in this part will suddenly increase. Especially at the welded groove, this part is the most prone to porosity defects. In addition, during soldering, if the flux is damp or contains impurities, porosity defects are prone to occur. After the occurrence of porosity defect welding, the available area of the place to be welded will naturally shrink. At the same time, the existence of porosity defect welding will also cause greater damage to the strength of metal components and reduce the compactness of the metal. Therefore, in metal welding, the inspection of welding with porosity defects is a very important link.
2. Slag inclusion defect
In the process of welding, it is certain that a certain amount of slag will be produced. The slag that appears in these weldings is easy to remain in the weld, which in turn leads to the occurrence of slag inclusion defects. There is a close relationship between the generation of slag and the cause of slag inclusion defects. In the welding of spiral steel pipes, the basic electrode is affected by an excessively long arc during the welding of spiral steel pipes. In addition, there are interferences such as inaccurate polarity and electrode misalignment. When passing through a certain welding gap, various slags also enter the weld, which eventually leads to the generation of slag inclusion defects.
3. Undercut defect
During welding, there are often depressions at the edge of metal welding, and this depression is an undercut defect. In metal welding, due to the excessive current used in welding, at the same time, due to the influence of various comprehensive reasons such as extremely fast transport speed and relatively long arc during welding, various degrees of undercut defects will occur. In addition, when the welding track is not complete, the actual welding position tends to develop to the deep layer of the metal. However, as a filler metal, the supplement to the gap is not perfect, and in this case, it is also easy to cause the occurrence of undercut defects. Once the undercut defect occurs, it will inevitably have a certain adverse effect on the welded parts, which will further affect the quality of the weld. Therefore, in the spiral steel pipe, during the metal welding process, it is necessary to avoid the occurrence of undercut defects as much as possible.
4. Incomplete penetration and incomplete fusion defects
During the welding process, some parts are not completely penetrated, which leads to the root position of the welded joint, which is prone to various incomplete penetration phenomena. In the welding of spiral steel pipes, between the weldment used for welding and the weld metal, or the middle part of the weldment and the weld. There is incomplete penetration, and this phenomenon of incomplete penetration can be called incomplete fusion defect. For spiral steel pipes, in the actual metal welding process, whether it is lack of fusion or incomplete penetration, it is a manifestation of more serious welding defects.
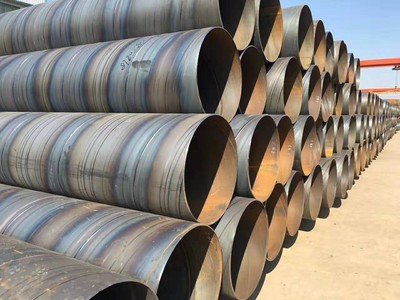
Control of Welding Process Defects of Spiral Steel Pipe
1. Solve the defect of stomata
In order to further solve the air hole defects in the welding of spiral steel pipes, it is necessary to eliminate the causes of air hole defects in a targeted manner. Starting from the current and speed of metal welding, for the occurrence of welding problems, strict quality inspection of welded parts is required. For the materials used in welding, according to the storage method of the materials used in welding, reasonable preservation should be carried out before actual welding. For the welded part, check it to further reduce the occurrence and appearance of porosity defects.
2. Solve the defect of slag inclusion
In actual welding, the size of the welding groove must be correctly selected. Pay attention to the rationality of welding current and welding speed, and pay special attention to the swing position of the strip. Pay attention to the condition of the welding joint of multi-layer welding, and clean up the welding slag in time. For the welding rods used in actual welding, attention should also be paid to the selection of quality. If there is an eccentric core in the welding rod, it cannot be used.
3. Undercut defect solution
Welding current is very important and critical to welding quality. The operation method of welding also needs to be paid attention to. In the metal welding of spiral steel pipe, the length of the arc and the angle of the electrode need to be paid attention to. Choose reasonable argon arc welding process parameters, and strictly control the speed at the beginning of welding.
4. Solve the defects of incomplete penetration and infusion
In order to further avoid the phenomenon of incomplete penetration and reduce the occurrence of incomplete fusion defects, it is necessary to correctly select the size of the welding groove. For the welding speed and current, it is also necessary to have a reasonable grasp. For the oxidation of the welding groove, it is necessary to pay attention to it in time, clean up the oxide scale in time, regularly observe the fusion situation on both sides of the groove, and provide timely remedies for problems found.
Welding defect and process analysis of spiral steel pipe
1. Pore defects
In the actual operation of spiral steel pipes, in the welding of metals, the most frequent defect is the defect of air holes. If there is moisture or rust in the welded part, the probability of serious porosity defects in this part will suddenly increase. Especially at the welded groove, this part is the most prone to porosity defects. In addition, during soldering, if the flux is damp or contains impurities, porosity defects are prone to occur. After the occurrence of porosity defect welding, the available area of the place to be welded will naturally shrink. At the same time, the existence of porosity defect welding will also cause greater damage to the strength of metal components and reduce the compactness of the metal. Therefore, in metal welding, the inspection of welding with porosity defects is a very important link.
2. Slag inclusion defect
In the process of welding, it is certain that a certain amount of slag will be produced. The slag that appears in these weldings is easy to remain in the weld, which in turn leads to the occurrence of slag inclusion defects. There is a close relationship between the generation of slag and the cause of slag inclusion defects. In the welding of spiral steel pipes, the basic electrode is affected by an excessively long arc during the welding of spiral steel pipes. In addition, there are interferences such as inaccurate polarity and electrode misalignment. When passing through a certain welding gap, various slags also enter the weld, which eventually leads to the generation of slag inclusion defects.
3. Undercut defect
During welding, there are often depressions at the edge of metal welding, and this depression is an undercut defect. In metal welding, due to the excessive current used in welding, at the same time, due to the influence of various comprehensive reasons such as extremely fast transport speed and relatively long arc during welding, various degrees of undercut defects will occur. In addition, when the welding track is not complete, the actual welding position tends to develop to the deep layer of the metal. However, as a filler metal, the supplement to the gap is not perfect, and in this case, it is also easy to cause the occurrence of undercut defects. Once the undercut defect occurs, it will inevitably have a certain adverse effect on the welded parts, which will further affect the quality of the weld. Therefore, in the spiral steel pipe, during the metal welding process, it is necessary to avoid the occurrence of undercut defects as much as possible.
4. Incomplete penetration and incomplete fusion defects
During the welding process, some parts are not completely penetrated, which leads to the root position of the welded joint, which is prone to various incomplete penetration phenomena. In the welding of spiral steel pipes, between the weldment used for welding and the weld metal, or the middle part of the weldment and the weld. There is incomplete penetration, and this phenomenon of incomplete penetration can be called incomplete fusion defect. For spiral steel pipes, in the actual metal welding process, whether it is lack of fusion or incomplete penetration, it is a manifestation of more serious welding defects.
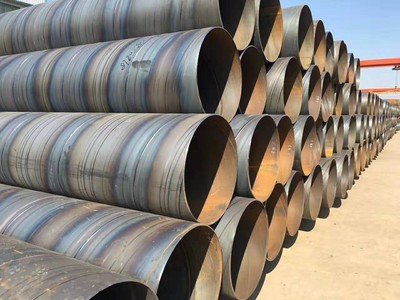
Control of Welding Process Defects of Spiral Steel Pipe
1. Solve the defect of stomata
In order to further solve the air hole defects in the welding of spiral steel pipes, it is necessary to eliminate the causes of air hole defects in a targeted manner. Starting from the current and speed of metal welding, for the occurrence of welding problems, strict quality inspection of welded parts is required. For the materials used in welding, according to the storage method of the materials used in welding, reasonable preservation should be carried out before actual welding. For the welded part, check it to further reduce the occurrence and appearance of porosity defects.
2. Solve the defect of slag inclusion
In actual welding, the size of the welding groove must be correctly selected. Pay attention to the rationality of welding current and welding speed, and pay special attention to the swing position of the strip. Pay attention to the condition of the welding joint of multi-layer welding, and clean up the welding slag in time. For the welding rods used in actual welding, attention should also be paid to the selection of quality. If there is an eccentric core in the welding rod, it cannot be used.
3. Undercut defect solution
Welding current is very important and critical to welding quality. The operation method of welding also needs to be paid attention to. In the metal welding of spiral steel pipe, the length of the arc and the angle of the electrode need to be paid attention to. Choose reasonable argon arc welding process parameters, and strictly control the speed at the beginning of welding.
4. Solve the defects of incomplete penetration and infusion
In order to further avoid the phenomenon of incomplete penetration and reduce the occurrence of incomplete fusion defects, it is necessary to correctly select the size of the welding groove. For the welding speed and current, it is also necessary to have a reasonable grasp. For the oxidation of the welding groove, it is necessary to pay attention to it in time, clean up the oxide scale in time, regularly observe the fusion situation on both sides of the groove, and provide timely remedies for problems found.