In the oil industry, the importance of well casing pipe is like blood vessels in the human body. It is the key channel for oil to be transported from the ground to the surface, and plays a supporting role in the normal operation of oil wells. However, in actual use, the inner and outer walls of the well casing pipe face severe corrosion tests. The internal corrosion of the well casing pipe is relatively more serious, mainly because the oil and natural gas inside it contain corrosive substances such as hydrogen sulfide, carbon dioxide, water, etc.
The external corrosion of well casing pipe is mainly soil corrosion. Soil is a complex multiphase system, in which water, oxygen, microorganisms and various electrolytes will "attack" the outer wall of the well casing pipe. Therefore, the implementation of effective anti-corrosion measures is essential to ensure the service life and safety of well casings. This article mainly introduces the common methods to prevent corrosion of these well casing pipes in different environments.
1. Selection of corrosion-resistant materials
a. Alloy steel materials
Alloy steels containing elements such as chromium (Cr), nickel (Ni), and molybdenum (Mo) are often selected as well casings due to their excellent corrosion resistance. 316 stainless steel contains 16-18% chromium, 10-14% nickel, and 2-3% molybdenum. It is often used in corrosive wells such as oil and gas wells, and its corrosion resistance is stronger than that of ordinary carbon steel.
For high-sulfur oil and gas wells, sulfur-resistant alloy steel can be selected. This material is specifically designed to resist corrosion from hydrogen sulfide (H₂S) that can cause sulfide stress corrosion cracking and other related problems.
b. Coating materials
Applying protective coatings is another common method to prevent corrosion of well casing pipes. Widely used pipe coatings include epoxy coatings and polyurethane coatings, which are applied to the surface of the pipe. The coating thickness is generally tens to hundreds of microns, depending on the specific corrosion conditions of the wellbore.
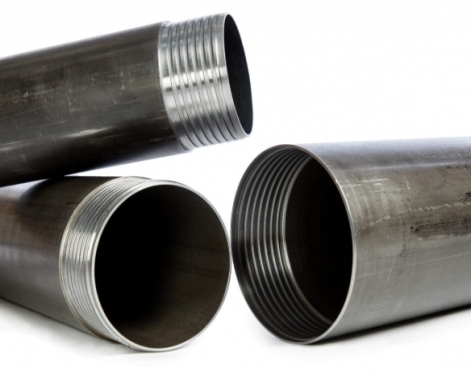
2. Use of corrosion inhibitors
Corrosion inhibitors are chemicals injected into the wellbore through the wellhead to form a protective film on the surface of the well casing. This protective film slows down the corrosion process. Corrosion inhibitors are classified according to their mechanism of action:
a. Anodic corrosion inhibitors: These inhibitors work by reducing the anodic reaction on the metal surface, thereby slowing down corrosion.
b. Cathodic corrosion inhibitors: These inhibitors prevent the cathodic reaction, thereby reducing the electrochemical corrosion process.
c. Hybrid corrosion inhibitors: They combine the properties of anodic and cathodic inhibitors to provide broad-spectrum protection.
3. Cathodic protection
a. Sacrificial anode protection
Sacrificial anodes made of materials such as magnesium alloy or aluminum alloy are installed around the well casing. These anodes are more reactive than the casing material and will corrode preferentially, providing protection to the well casing by acting as a cathode.
b. Impressed current cathodic protection (ICCP)
In an impressed current cathodic protection system, an external DC power supply and auxiliary anodes are installed near the well casing. The system can provide a constant and adjustable protection current to the casing, making it suitable for complex environments with high corrosion rates. However, the design, installation and maintenance of ICCP systems require expertise, and regular monitoring is essential to ensure their effectiveness.
4. Improving the wellbore environment
a. Water quality control
In water injection wells, it is critical to control the quality of the injected water. Measures such as filtration, deoxygenation and sterilization help reduce the levels of suspended solids, dissolved oxygen, bacteria and other contaminants that can cause corrosion.
b. Reducing Hydrogen Sulfide and Carbon Dioxide
For wells with high levels of hydrogen sulfide (H₂S) and carbon dioxide (CO₂), these gases can be removed from the produced fluid using technologies such as gas-liquid separation. Alternatively, chemical absorption can be used to absorb H₂S and CO₂, reducing their concentrations and preventing casing corrosion.
5. Regular Inspection and Maintenance
a. Corrosion Detection
To assess the condition of well casing pipe, various corrosion detection methods can be used, such as ultrasonic testing, magnetic particle testing, and radiographic testing. These methods help determine the extent of corrosion and whether further anti-corrosion measures or maintenance measures are required.
b. Maintenance Measures
When minor corrosion is detected, appropriate maintenance measures can be taken. For surface corrosion, repairs may include rust removal and repainting. For severe localized corrosion, repair welding or other methods can be used to restore the integrity of the pipe. After repair, the welded area should undergo another round of inspection to ensure the quality and corrosion resistance of the repaired section.
Regular inspection and maintenance are essential to extend the service life of well casing pipe. Establishing a comprehensive maintenance profile and tracking the results of each inspection and repair helps ensure timely intervention and supports an effective corrosion prevention strategy.
Read more: Well Casing Pipe: Functions, Characteristics and Applications
The external corrosion of well casing pipe is mainly soil corrosion. Soil is a complex multiphase system, in which water, oxygen, microorganisms and various electrolytes will "attack" the outer wall of the well casing pipe. Therefore, the implementation of effective anti-corrosion measures is essential to ensure the service life and safety of well casings. This article mainly introduces the common methods to prevent corrosion of these well casing pipes in different environments.
1. Selection of corrosion-resistant materials
a. Alloy steel materials
Alloy steels containing elements such as chromium (Cr), nickel (Ni), and molybdenum (Mo) are often selected as well casings due to their excellent corrosion resistance. 316 stainless steel contains 16-18% chromium, 10-14% nickel, and 2-3% molybdenum. It is often used in corrosive wells such as oil and gas wells, and its corrosion resistance is stronger than that of ordinary carbon steel.
For high-sulfur oil and gas wells, sulfur-resistant alloy steel can be selected. This material is specifically designed to resist corrosion from hydrogen sulfide (H₂S) that can cause sulfide stress corrosion cracking and other related problems.
b. Coating materials
Applying protective coatings is another common method to prevent corrosion of well casing pipes. Widely used pipe coatings include epoxy coatings and polyurethane coatings, which are applied to the surface of the pipe. The coating thickness is generally tens to hundreds of microns, depending on the specific corrosion conditions of the wellbore.
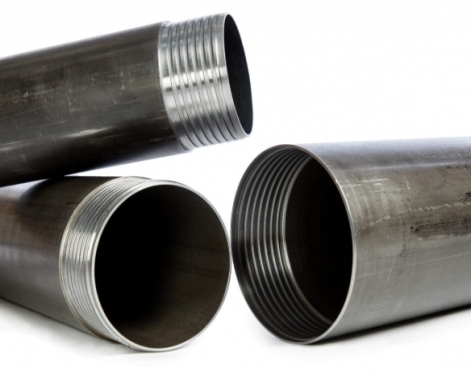
2. Use of corrosion inhibitors
Corrosion inhibitors are chemicals injected into the wellbore through the wellhead to form a protective film on the surface of the well casing. This protective film slows down the corrosion process. Corrosion inhibitors are classified according to their mechanism of action:
a. Anodic corrosion inhibitors: These inhibitors work by reducing the anodic reaction on the metal surface, thereby slowing down corrosion.
b. Cathodic corrosion inhibitors: These inhibitors prevent the cathodic reaction, thereby reducing the electrochemical corrosion process.
c. Hybrid corrosion inhibitors: They combine the properties of anodic and cathodic inhibitors to provide broad-spectrum protection.
3. Cathodic protection
a. Sacrificial anode protection
Sacrificial anodes made of materials such as magnesium alloy or aluminum alloy are installed around the well casing. These anodes are more reactive than the casing material and will corrode preferentially, providing protection to the well casing by acting as a cathode.
b. Impressed current cathodic protection (ICCP)
In an impressed current cathodic protection system, an external DC power supply and auxiliary anodes are installed near the well casing. The system can provide a constant and adjustable protection current to the casing, making it suitable for complex environments with high corrosion rates. However, the design, installation and maintenance of ICCP systems require expertise, and regular monitoring is essential to ensure their effectiveness.
4. Improving the wellbore environment
a. Water quality control
In water injection wells, it is critical to control the quality of the injected water. Measures such as filtration, deoxygenation and sterilization help reduce the levels of suspended solids, dissolved oxygen, bacteria and other contaminants that can cause corrosion.
b. Reducing Hydrogen Sulfide and Carbon Dioxide
For wells with high levels of hydrogen sulfide (H₂S) and carbon dioxide (CO₂), these gases can be removed from the produced fluid using technologies such as gas-liquid separation. Alternatively, chemical absorption can be used to absorb H₂S and CO₂, reducing their concentrations and preventing casing corrosion.
5. Regular Inspection and Maintenance
a. Corrosion Detection
To assess the condition of well casing pipe, various corrosion detection methods can be used, such as ultrasonic testing, magnetic particle testing, and radiographic testing. These methods help determine the extent of corrosion and whether further anti-corrosion measures or maintenance measures are required.
b. Maintenance Measures
When minor corrosion is detected, appropriate maintenance measures can be taken. For surface corrosion, repairs may include rust removal and repainting. For severe localized corrosion, repair welding or other methods can be used to restore the integrity of the pipe. After repair, the welded area should undergo another round of inspection to ensure the quality and corrosion resistance of the repaired section.
Regular inspection and maintenance are essential to extend the service life of well casing pipe. Establishing a comprehensive maintenance profile and tracking the results of each inspection and repair helps ensure timely intervention and supports an effective corrosion prevention strategy.
Read more: Well Casing Pipe: Functions, Characteristics and Applications