1.What is API 5CT H40 octg casing?
API 5CT: The American Petroleum Institute (API) 5CT is a standard that sets specifications for the technical delivery conditions of steel pipes for use in oil and gas wells, including casing, tubing, and other related products. This standard is widely recognized and adopted by the oil and gas industry globally, ensuring consistency and quality in the materials used for drilling and extraction operations.
H40 Grade: The "H40" designation in API 5CT H40 OCTG casing refers to the specific grade of steel used in manufacturing the casing. In this context, "H" designates the minimum yield strength of the material, which is 40,000 pounds per square inch (psi). The yield strength is an important mechanical property of the steel as it indicates the maximum stress that the material can undergo before permanent deformation occurs.
OCTG Casing: Oil Country Tubular Goods (OCTG) casing is a critical component used in oil and gas well construction. Casing serves several essential functions, including providing structural support to the wellbore, preventing formation collapse, isolating different formations, and facilitating the installation of various downhole tools and equipment.
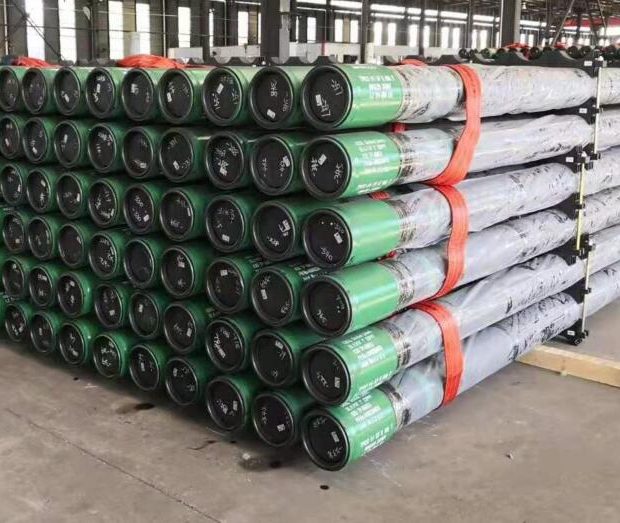
2.Manufacturing process of API 5CT H40 octg casing
The manufacturing process of API 5CT H40 OCTG casing involves several crucial steps to ensure the production of high-quality, seamless steel casing that meets the stringent standards set by the API.
(1)Steel Production
The manufacturing process commences with the production of raw steel. The steel used for OCTG casing is typically produced in electric arc furnaces or basic oxygen furnaces, where various elements are carefully controlled to achieve the required chemical composition and mechanical properties.
(2)Forming
Once the steel has been produced, it is then shaped into cylindrical billets through a hot rolling process. These billets serve as the starting material for the subsequent manufacturing steps.
(3)Piercing and Rolling
The billets are heated and pierced to form a hollow shell, which will ultimately become the seamless casing pipe. The pierced billet is then rolled to reduce its diameter and wall thickness while increasing its length. This process is repeated through multiple rolling stands to achieve the desired dimensions and properties.
(4)Heat Treatment
After the initial forming and sizing, the casing undergoes a heat treatment process to enhance its mechanical properties, such as strength and toughness. This commonly involves quenching and tempering, which helps achieve the specified yield strength and hardness.
(5)Straightening and Inspection
The casing pipe is then straightened to remove any residual distortions and ensure its dimensional accuracy. Furthermore, non-destructive testing methods, such as ultrasonic testing, electromagnetic inspection, and visual inspection, are employed to detect any surface or internal defects.
(6)Thread Cutting
To enable proper connection and sealing between casing joints, threads are cut at both ends of the casing pipe using specialized threading machines. The threads must adhere to precise dimensional and geometric specifications to ensure compatibility with other downhole components.
(7)Surface Protection
Upon completion of the manufacturing process, the casing is coated with a protective layer, such as corrosion-resistant coatings or thread compounds, to safeguard it from environmental and operational hazards encountered during drilling and production operations.
Throughout the entire manufacturing process, strict quality control measures are implemented to verify compliance with API 5CT specifications. This includes material traceability, dimensional inspections, mechanical testing, and non-destructive examinations to ensure the integrity and reliability of the finished API 5CT H40 OCTG casing.
API 5CT: The American Petroleum Institute (API) 5CT is a standard that sets specifications for the technical delivery conditions of steel pipes for use in oil and gas wells, including casing, tubing, and other related products. This standard is widely recognized and adopted by the oil and gas industry globally, ensuring consistency and quality in the materials used for drilling and extraction operations.
H40 Grade: The "H40" designation in API 5CT H40 OCTG casing refers to the specific grade of steel used in manufacturing the casing. In this context, "H" designates the minimum yield strength of the material, which is 40,000 pounds per square inch (psi). The yield strength is an important mechanical property of the steel as it indicates the maximum stress that the material can undergo before permanent deformation occurs.
OCTG Casing: Oil Country Tubular Goods (OCTG) casing is a critical component used in oil and gas well construction. Casing serves several essential functions, including providing structural support to the wellbore, preventing formation collapse, isolating different formations, and facilitating the installation of various downhole tools and equipment.
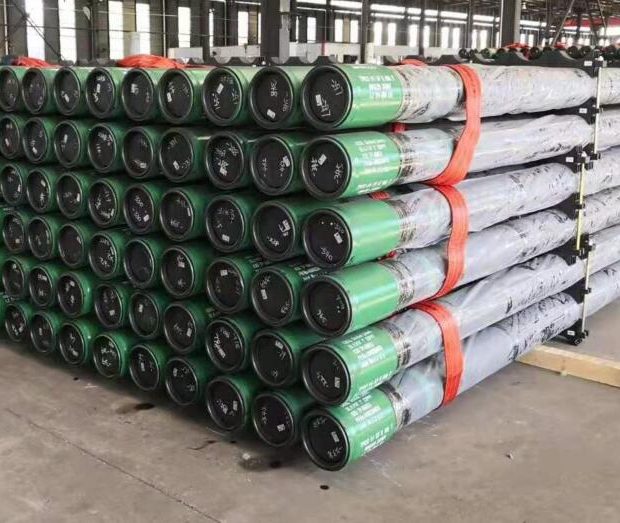
2.Manufacturing process of API 5CT H40 octg casing
The manufacturing process of API 5CT H40 OCTG casing involves several crucial steps to ensure the production of high-quality, seamless steel casing that meets the stringent standards set by the API.
(1)Steel Production
The manufacturing process commences with the production of raw steel. The steel used for OCTG casing is typically produced in electric arc furnaces or basic oxygen furnaces, where various elements are carefully controlled to achieve the required chemical composition and mechanical properties.
(2)Forming
Once the steel has been produced, it is then shaped into cylindrical billets through a hot rolling process. These billets serve as the starting material for the subsequent manufacturing steps.
(3)Piercing and Rolling
The billets are heated and pierced to form a hollow shell, which will ultimately become the seamless casing pipe. The pierced billet is then rolled to reduce its diameter and wall thickness while increasing its length. This process is repeated through multiple rolling stands to achieve the desired dimensions and properties.
(4)Heat Treatment
After the initial forming and sizing, the casing undergoes a heat treatment process to enhance its mechanical properties, such as strength and toughness. This commonly involves quenching and tempering, which helps achieve the specified yield strength and hardness.
(5)Straightening and Inspection
The casing pipe is then straightened to remove any residual distortions and ensure its dimensional accuracy. Furthermore, non-destructive testing methods, such as ultrasonic testing, electromagnetic inspection, and visual inspection, are employed to detect any surface or internal defects.
(6)Thread Cutting
To enable proper connection and sealing between casing joints, threads are cut at both ends of the casing pipe using specialized threading machines. The threads must adhere to precise dimensional and geometric specifications to ensure compatibility with other downhole components.
(7)Surface Protection
Upon completion of the manufacturing process, the casing is coated with a protective layer, such as corrosion-resistant coatings or thread compounds, to safeguard it from environmental and operational hazards encountered during drilling and production operations.
Throughout the entire manufacturing process, strict quality control measures are implemented to verify compliance with API 5CT specifications. This includes material traceability, dimensional inspections, mechanical testing, and non-destructive examinations to ensure the integrity and reliability of the finished API 5CT H40 OCTG casing.
Previous:SCH 40 vs SCH 40S