"Thermal shock resistance" refers to the ability of a material to resist cracking, deformation or performance degradation when it undergoes rapid and drastic temperature changes. For seamless steel pipes, thermal shock resistance is very important, especially in the following application scenarios:
Boilers and heat exchangers: There is a huge difference between the temperature of the fluid inside the pipeline and the external environment or the temperature of the fluid on the other side, or the temperature changes suddenly when the system starts and stops.
High-temperature chemical equipment: transports high-temperature media and may face sudden cooling.
Power station pipelines: steam pipelines, superheaters, reheaters, etc., which are subject to high pressure, high temperature and temperature fluctuations.
Thermal shock resistance of seamless steel pipe
Seamless steel pipes have structural advantages because they do not have a weak point such as a weld and can better cope with overall thermal stress. However, their specific thermal shock resistance mainly depends on the material (chemical composition) of the steel, the production process, the heat treatment status, and the size and geometry of the pipe.
When a steel pipe is subjected to thermal shock, thermal stress will be generated inside the pipe. This is caused by uneven expansion or contraction due to different temperature change rates in different parts. If this thermal stress exceeds the yield strength or tensile strength of the material, it will cause plastic deformation, microcracks and even macro fractures.
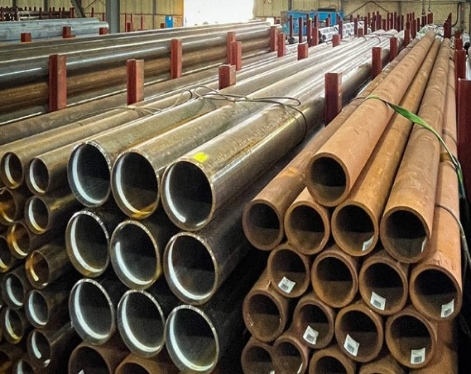
Factors affecting the thermal shock resistance of seamless steel pipes
To improve the thermal shock resistance of seamless steel pipes, it is usually necessary to consider the following aspects:
1. Material composition
Low coefficient of thermal expansion: The lower the coefficient of thermal expansion of a material, the smaller the dimensional change when the temperature changes, and the less thermal stress is generated.
High thermal conductivity: The higher the thermal conductivity of a material, the faster the heat is conducted inside the tube wall and the more evenly the temperature is distributed, thereby reducing local temperature differences and thermal stress. The thermal conductivity of carbon steel is usually higher than that of stainless steel.
High strength and toughness: Even if thermal stress occurs, if the material has sufficient strength and good toughness, it can absorb and disperse these stresses and resist the initiation and expansion of cracks.
Adding alloy elements: chromium (Cr), molybdenum (Mo), nickel (Ni), vanadium (V), tungsten (W), titanium (Ti) and other alloy elements can significantly improve the high temperature strength, creep resistance, oxidation resistance and corrosion resistance of steel, thereby indirectly improving its stability in complex thermal environments. For example, alloy steels (such as P11, P22, P91) and stainless steels (such as 304H, 316H, 310S, 321H, 347H) are widely used in heat shock resistant occasions due to their special high temperature performance and corrosion resistance.
2. Microstructure
Uniform and fine grain structure helps to improve the toughness and crack propagation resistance of the material.
Avoid structural defects and stress concentration areas.
3. Production process and heat treatment
Reasonable cold working and heat treatment: through normalizing, quenching, tempering, solution treatment, etc., the microstructure of steel can be optimized, internal stress can be eliminated, and the balance between strength and toughness can be adjusted, thereby improving its resistance to thermal shock. For example, quenching and tempering can significantly improve the comprehensive mechanical properties of steel.
Surface quality: Smooth internal and external surfaces can reduce stress concentration points and reduce the risk of crack initiation.
4. Tube geometry
Wall thickness: Too much wall thickness will lead to uneven heat transfer, large temperature difference between inside and outside during rapid heating or cooling, and greater thermal stress. Therefore, in situations where good thermal shock resistance is required, relatively thin-walled pipes are sometimes selected, or materials with higher thermal conductivity are selected.
Complex shapes: Sharp geometric features or sudden changes in size can easily lead to stress concentrations.
How to select and improve the thermal shock resistance of seamless steel pipes?
In practical applications, choosing seamless steel pipes with good thermal shock resistance usually means:
Choose alloy steel or stainless steel of specific material: for example, various T/TP series grades (such as TP304H, TP316H, TP321H, P22, P91, etc.) under ASTM A213 / ASME SA213 standards commonly used in boilers and heat exchangers are designed for high temperature, high pressure and thermal shock conditions.
Strictly control the production process and heat treatment: ensure that the internal structure of the steel pipe is uniform and defect-free, and the mechanical properties meet the standard requirements.
Consider design factors: When designing the system, drastic temperature changes and local stress concentration should be avoided as much as possible. Thermal shock to the steel pipe can be reduced by preheating, slow cooling, and setting expansion joints.
In short, the "heat shock resistance" performance of seamless steel pipes is not a single indicator, but is determined by multiple factors such as its material, manufacturing process and design. Under high temperature or temperature change risk working conditions, high-performance seamless steel pipes specially designed and produced for such conditions must be selected.
Read more: How to Accurately Control the Wall Thickness and Diameter of Seamless Pipes?
Boilers and heat exchangers: There is a huge difference between the temperature of the fluid inside the pipeline and the external environment or the temperature of the fluid on the other side, or the temperature changes suddenly when the system starts and stops.
High-temperature chemical equipment: transports high-temperature media and may face sudden cooling.
Power station pipelines: steam pipelines, superheaters, reheaters, etc., which are subject to high pressure, high temperature and temperature fluctuations.
Thermal shock resistance of seamless steel pipe
Seamless steel pipes have structural advantages because they do not have a weak point such as a weld and can better cope with overall thermal stress. However, their specific thermal shock resistance mainly depends on the material (chemical composition) of the steel, the production process, the heat treatment status, and the size and geometry of the pipe.
When a steel pipe is subjected to thermal shock, thermal stress will be generated inside the pipe. This is caused by uneven expansion or contraction due to different temperature change rates in different parts. If this thermal stress exceeds the yield strength or tensile strength of the material, it will cause plastic deformation, microcracks and even macro fractures.
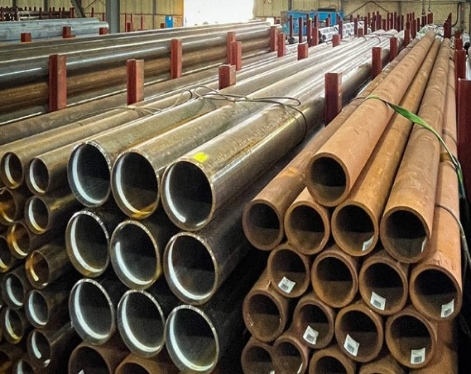
Factors affecting the thermal shock resistance of seamless steel pipes
To improve the thermal shock resistance of seamless steel pipes, it is usually necessary to consider the following aspects:
1. Material composition
Low coefficient of thermal expansion: The lower the coefficient of thermal expansion of a material, the smaller the dimensional change when the temperature changes, and the less thermal stress is generated.
High thermal conductivity: The higher the thermal conductivity of a material, the faster the heat is conducted inside the tube wall and the more evenly the temperature is distributed, thereby reducing local temperature differences and thermal stress. The thermal conductivity of carbon steel is usually higher than that of stainless steel.
High strength and toughness: Even if thermal stress occurs, if the material has sufficient strength and good toughness, it can absorb and disperse these stresses and resist the initiation and expansion of cracks.
Adding alloy elements: chromium (Cr), molybdenum (Mo), nickel (Ni), vanadium (V), tungsten (W), titanium (Ti) and other alloy elements can significantly improve the high temperature strength, creep resistance, oxidation resistance and corrosion resistance of steel, thereby indirectly improving its stability in complex thermal environments. For example, alloy steels (such as P11, P22, P91) and stainless steels (such as 304H, 316H, 310S, 321H, 347H) are widely used in heat shock resistant occasions due to their special high temperature performance and corrosion resistance.
2. Microstructure
Uniform and fine grain structure helps to improve the toughness and crack propagation resistance of the material.
Avoid structural defects and stress concentration areas.
3. Production process and heat treatment
Reasonable cold working and heat treatment: through normalizing, quenching, tempering, solution treatment, etc., the microstructure of steel can be optimized, internal stress can be eliminated, and the balance between strength and toughness can be adjusted, thereby improving its resistance to thermal shock. For example, quenching and tempering can significantly improve the comprehensive mechanical properties of steel.
Surface quality: Smooth internal and external surfaces can reduce stress concentration points and reduce the risk of crack initiation.
4. Tube geometry
Wall thickness: Too much wall thickness will lead to uneven heat transfer, large temperature difference between inside and outside during rapid heating or cooling, and greater thermal stress. Therefore, in situations where good thermal shock resistance is required, relatively thin-walled pipes are sometimes selected, or materials with higher thermal conductivity are selected.
Complex shapes: Sharp geometric features or sudden changes in size can easily lead to stress concentrations.
How to select and improve the thermal shock resistance of seamless steel pipes?
In practical applications, choosing seamless steel pipes with good thermal shock resistance usually means:
Choose alloy steel or stainless steel of specific material: for example, various T/TP series grades (such as TP304H, TP316H, TP321H, P22, P91, etc.) under ASTM A213 / ASME SA213 standards commonly used in boilers and heat exchangers are designed for high temperature, high pressure and thermal shock conditions.
Strictly control the production process and heat treatment: ensure that the internal structure of the steel pipe is uniform and defect-free, and the mechanical properties meet the standard requirements.
Consider design factors: When designing the system, drastic temperature changes and local stress concentration should be avoided as much as possible. Thermal shock to the steel pipe can be reduced by preheating, slow cooling, and setting expansion joints.
In short, the "heat shock resistance" performance of seamless steel pipes is not a single indicator, but is determined by multiple factors such as its material, manufacturing process and design. Under high temperature or temperature change risk working conditions, high-performance seamless steel pipes specially designed and produced for such conditions must be selected.
Read more: How to Accurately Control the Wall Thickness and Diameter of Seamless Pipes?