The flattening test of ERW welded pipes can effectively and quickly uate the quality of welds and raw materials. With the continuous improvement of smelting and rolling technology and the continuous advancement of pipe making levels, as well as the use of ERW welded pipes in harsh environments such as low temperature, high pressure, and corrosion resistance, higher requirements are now demanded for the flattening test of ERW welded pipes. From API SPEC5L This is also evident in the changes in the acceptance criteria for flattening tests in the "Specification for Pipeline Steel Pipes" 42 Edition 1 and API SPEC 5L 43 Edition 2. Manufacturers of ERW welded pipes face particular necessity to study the causes of weld cracking in the flattening test of welded pipes and formulate corresponding preventive measures.
Higher requirements, but still basic and general requirements. For high-toughness raw materials, only when there are serious defects in the weld, such as pre-arc, cold welding, over-burning, and raw material edge bumps, the weld should be flattened at 90° to 2/2 of the original outer diameter of the steel pipe. 3 or 1/2, the weld will crack. These defects are less likely to occur and are easily discovered during ultrasonic flaw detection. When there are small inclusions in the weld that affect the impact toughness, cracking of the weld may occur only when the two opposite walls of the steel pipe are flattened to a close fit. The probability of these weld inclusions appearing is higher. According to
The API SPEC 5L standard requires ultrasonic inspection and is difficult to detect.
In order to effectively uate the quality of the weld using the flattening test, the weld inclusion crack index can be used to uate the weld quality. The weld inclusion crack index refers to the number or length of cracks per unit length caused by inclusions that cause the weld to crack when the ERW welded pipe weld is flattened at 90° until the two opposite pipe walls of the steel pipe fit together, expressed in units/m Or expressed in mm/m. Because the weld inclusion crack index determines the weld quality quickly, simply, and conveniently, it can provide a basis for process adjustment in a timely manner. In addition to using the existing flattening test equipment in the factory, other specialized instruments and equipment are no longer needed, which is easy to be managed. Factory adopted.
Welded pipe manufacturers can determine different inclusion crack indexes according to the different use environments of welded pipes as the factory's internal control standards. At present, the causes of inclusions and their influencing factors are studied.
The percentage of the inclusion area at the weld fracture to the weld area or the number of inclusions per unit area is often used to uate the weld quality. In fact, the results of using the weld inclusion crack index and using the percentage of the inclusion area at the weld fracture to the weld area or the number of inclusions per unit area to uate the weld quality are consistent.
MnO +SiO₂ = MnOSiO₂, the melting point of MnOSiO₂ is 1270℃, and it is easily discharged from the weld.
(1) After milling by the edge milling machine, the edge of the steel strip is relatively straight, and the molten metal is discharged smoothly; while after the edge is cut by the disc shear, the edge of the steel strip forms a small arc on one side of the corner due to the shearing force. The corners on the other side are prone to burrs. During welding, it is easy to produce double peaks at the arc, which is not conducive to the discharge of molten metal and oxides. The burrs generated make the internal current larger, resulting in uneven heating on the inside and outside. The difference in impact toughness of the edge welds between the two steel strips also proves this point.
(2) Bruised and rust-stained edges of the steel strip hinder molten metal discharge and cause weld inclusions.
(3) Uneven wall thickness, burrs and bulges can easily cause fluctuations in welding current and affect welding quality. Therefore, the edge of the steel strip must be fully formed, the edge must be straight, smooth, burr-free and the wall thickness must be uniform.
In V-type butt joints, the inner side of the steel pipe is contacted and welded first, and the inner welding current is higher than the outer wall welding current, making the inner side temperature higher than the outer wall welding temperature. In V-shaped butt joints, more heat input is required. The inner and outer walls of the I-shaped butt steel pipe are in contact at the same time, so the temperature is relatively uniform. Inverted V-shaped butt jointing is exactly the opposite of V-shaped butt jointing. The outer wall of the steel pipe is contacted and welded first, and the outer wall welding current is higher than the inner welding current, making the outer wall temperature higher than the inner wall.
V-shaped contact is easily formed due to the comprehensive reasons of the outer stretching and inner compression of the steel strip before entering the closed hole, the diameter reduction after entering the closed hole, and the difference in inner and outer circumference after forming the tube blank. The V-shaped size must be controlled during actual production. If the V shape is too large, the inner side will contact for a longer time than the outer side, the outer wall current will be smaller, and the temperature difference between the inner and outer sides will be large, which can easily cause welding defects. The butt joint shape of the weld can be determined by using the difference in the rise angle of the inner and outer metal streamlines or the difference in the meshing point positions of the inner and outer steel strips.
Tests have shown that for a given raw material, different V-shaped butt joint shapes have a greater impact on the crack index of weld inclusions. For a given machine, the V-angle of the V-joint can be adjusted by adjusting the closed pass and welded squeeze rollers. For specific units, raw materials and steel pipe specifications, steel pipe manufacturers can determine and optimize the shape of the V-shaped joint through the inclusion crack index.
The smaller the amount of extrusion, the smaller the rise angle of metal streamlines, and the greater the possibility of inclusions in the weld; the greater the amount of extrusion, the larger the rise angle of metal streamlines, and the more molten metal and oxides will be extruded. If the extrusion If the pressure is too large, too much molten metal will be extruded, and it will be difficult for the weld to form common grains. The reasonable amount of extrusion can be controlled by the metal streamline lifting angle and the fusion line width. Generally, the metal streamline lifting angle is controlled at 60°~70°, and the width of the fusion line in the middle of the weld is 0.02~0.12mm.
Steel strips with significant band-like structures or high sulfur content should have the metal streamline lift angle appropriately reduced.
When the sulfur content is high, low-melting eutectic materials are easily formed. The low-melting eutectic material or brittle hard phase is subjected to the shear force during welding, heating and extrusion, and cracks along the metal streamline to form hook-shaped cracks. When the weld is flattened, the heat-affected zone cracks along hook-shaped cracks. In addition, the heat treatment of the weld seam also has a certain impact on the cracking resistance of the weld seam in the flattening test.
1.Weld inclusion crack index
Flattening and cracking of ERW welded pipe welds are caused by insufficient strength, toughness or ductility of the weld. The API SPEC 5L43 version of "Specification for Pipeline Steel Pipes" has proposed acceptance standards for flattening tests compared to the 42nd version.Higher requirements, but still basic and general requirements. For high-toughness raw materials, only when there are serious defects in the weld, such as pre-arc, cold welding, over-burning, and raw material edge bumps, the weld should be flattened at 90° to 2/2 of the original outer diameter of the steel pipe. 3 or 1/2, the weld will crack. These defects are less likely to occur and are easily discovered during ultrasonic flaw detection. When there are small inclusions in the weld that affect the impact toughness, cracking of the weld may occur only when the two opposite walls of the steel pipe are flattened to a close fit. The probability of these weld inclusions appearing is higher. According to
The API SPEC 5L standard requires ultrasonic inspection and is difficult to detect.
In order to effectively uate the quality of the weld using the flattening test, the weld inclusion crack index can be used to uate the weld quality. The weld inclusion crack index refers to the number or length of cracks per unit length caused by inclusions that cause the weld to crack when the ERW welded pipe weld is flattened at 90° until the two opposite pipe walls of the steel pipe fit together, expressed in units/m Or expressed in mm/m. Because the weld inclusion crack index determines the weld quality quickly, simply, and conveniently, it can provide a basis for process adjustment in a timely manner. In addition to using the existing flattening test equipment in the factory, other specialized instruments and equipment are no longer needed, which is easy to be managed. Factory adopted.
Welded pipe manufacturers can determine different inclusion crack indexes according to the different use environments of welded pipes as the factory's internal control standards. At present, the causes of inclusions and their influencing factors are studied.
The percentage of the inclusion area at the weld fracture to the weld area or the number of inclusions per unit area is often used to uate the weld quality. In fact, the results of using the weld inclusion crack index and using the percentage of the inclusion area at the weld fracture to the weld area or the number of inclusions per unit area to uate the weld quality are consistent.
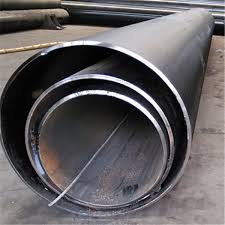
2 Causes of weld inclusions and countermeasures to reduce them
Cracks in the weld flattening test often originate from weld microcracks, hard and brittle phase inclusions, coarse grains, etc. To reduce weld flattening and cracking, the toughness of the weld must be improved and the inclusions in the weld must be reduced.2.1 Chemical composition of raw materials
First of all, we must improve the purity of raw materials, reduce the content of P and S, and reduce the content of inclusions. Secondly, the Mn/Si ratio in the raw materials affects the crack index of weld inclusions. During high-frequency welding, low-melting point substances are more likely to be extruded from the edge of the steel strip. During high-frequency heating, Fe at the edge of the steel strip is oxidized into FeO, and Mn, Si and FeO in the molten metal react to form MnO and SiO₂. The following reaction occurs between MnO and SiO₂:MnO +SiO₂ = MnOSiO₂, the melting point of MnOSiO₂ is 1270℃, and it is easily discharged from the weld.
2.2 Edge condition of raw materials
The edge condition of the steel strip affects the discharge of molten oxides from the weld.(1) After milling by the edge milling machine, the edge of the steel strip is relatively straight, and the molten metal is discharged smoothly; while after the edge is cut by the disc shear, the edge of the steel strip forms a small arc on one side of the corner due to the shearing force. The corners on the other side are prone to burrs. During welding, it is easy to produce double peaks at the arc, which is not conducive to the discharge of molten metal and oxides. The burrs generated make the internal current larger, resulting in uneven heating on the inside and outside. The difference in impact toughness of the edge welds between the two steel strips also proves this point.
(2) Bruised and rust-stained edges of the steel strip hinder molten metal discharge and cause weld inclusions.
(3) Uneven wall thickness, burrs and bulges can easily cause fluctuations in welding current and affect welding quality. Therefore, the edge of the steel strip must be fully formed, the edge must be straight, smooth, burr-free and the wall thickness must be uniform.
2.3 Docking shape
Theoretically, through the design of the roll pass and guide ring, ERW welded pipes can form three butt shapes, namely V-shaped butt, I-shaped butt and inverted V-shaped butt.In V-type butt joints, the inner side of the steel pipe is contacted and welded first, and the inner welding current is higher than the outer wall welding current, making the inner side temperature higher than the outer wall welding temperature. In V-shaped butt joints, more heat input is required. The inner and outer walls of the I-shaped butt steel pipe are in contact at the same time, so the temperature is relatively uniform. Inverted V-shaped butt jointing is exactly the opposite of V-shaped butt jointing. The outer wall of the steel pipe is contacted and welded first, and the outer wall welding current is higher than the inner welding current, making the outer wall temperature higher than the inner wall.
V-shaped contact is easily formed due to the comprehensive reasons of the outer stretching and inner compression of the steel strip before entering the closed hole, the diameter reduction after entering the closed hole, and the difference in inner and outer circumference after forming the tube blank. The V-shaped size must be controlled during actual production. If the V shape is too large, the inner side will contact for a longer time than the outer side, the outer wall current will be smaller, and the temperature difference between the inner and outer sides will be large, which can easily cause welding defects. The butt joint shape of the weld can be determined by using the difference in the rise angle of the inner and outer metal streamlines or the difference in the meshing point positions of the inner and outer steel strips.
Tests have shown that for a given raw material, different V-shaped butt joint shapes have a greater impact on the crack index of weld inclusions. For a given machine, the V-angle of the V-joint can be adjusted by adjusting the closed pass and welded squeeze rollers. For specific units, raw materials and steel pipe specifications, steel pipe manufacturers can determine and optimize the shape of the V-shaped joint through the inclusion crack index.
2.4 Welding extrusion amount
The smaller the amount of extrusion, the smaller the rise angle of metal streamlines, and the greater the possibility of inclusions in the weld; the greater the amount of extrusion, the larger the rise angle of metal streamlines, and the more molten metal and oxides will be extruded. If the extrusion If the pressure is too large, too much molten metal will be extruded, and it will be difficult for the weld to form common grains. The reasonable amount of extrusion can be controlled by the metal streamline lifting angle and the fusion line width. Generally, the metal streamline lifting angle is controlled at 60°~70°, and the width of the fusion line in the middle of the weld is 0.02~0.12mm.Steel strips with significant band-like structures or high sulfur content should have the metal streamline lift angle appropriately reduced.
2.5 Other influencing factors
To reduce cracking in the heat-affected zone when ERW welded pipes are flattened, the strip structure and inclusions of the steel strip must be reduced. The banded structure is caused by component segregation. The dendrite segregation formed on the continuous casting slab forms strip segregation after rolling. Carbon-rich and alloying element-rich and carbon-poor and alloying element-poor strips are distributed alternately. When cooling from the austenite zone and phase transformation occurs, ferrite preferentially occurs in the carbon-poor and alloying element-poor zone with a higher critical point. The formation of ferrite further repels carbon into the carbon-rich and alloying element-rich zone, and finally transform into a carbon-rich tissue zone. The carbon-rich tissue zone is often accompanied by sulfides, oxides, etc., making it highly hard and brittle.When the sulfur content is high, low-melting eutectic materials are easily formed. The low-melting eutectic material or brittle hard phase is subjected to the shear force during welding, heating and extrusion, and cracks along the metal streamline to form hook-shaped cracks. When the weld is flattened, the heat-affected zone cracks along hook-shaped cracks. In addition, the heat treatment of the weld seam also has a certain impact on the cracking resistance of the weld seam in the flattening test.
In conclusion
The crack index of weld inclusions can be used as a parameter for pipe making processes, forming the basis for optimization and the control standards for pipe production quality. Improving the purity of steel, rationally designing the chemical composition, reducing band structures and inclusions in the steel, and reasonably controlling the pipe making process parameters can effectively reduce the crack index of weld inclusions and improve the flattening resistance of ERW welded pipes cracking properties.
Next:Mild steel erw pipe