Analyze the defects and hazards of welded tubes welding, study the causes of welded tubes welding quality defects, and take effective control measures to achieve high reliability and high safety of welded tubes welding quality, and help safe development of petrochemical enterprises.
1. Defects and hazards in welding of welded pipes
(1) Common defects in welded tubes welding
Pipe surface defects: surface cracks, undercuts, surface pores, welding nodules, welding deformation, wrong edges, etc. Internal defects in pipeline welding: internal pores, slag inclusions, incomplete welding, lack of fusion, etc.
(2) The hazards of welding defects in welded tubes
Reducing the welding strength of pipeline welding interfaces will affect the appearance and forming quality of pipeline welds, and may cause leakage and material blockage in welded tubes.
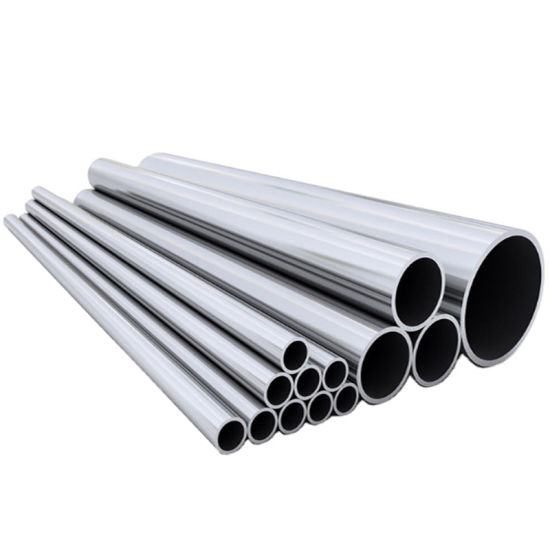
2. Factors affecting the welding quality of welded pipes
(1) The pipeline welding process is improperly selected.
(2) Pipeline welding workers lack quality awareness, lack welding technical capabilities, and fail to strictly implement welding process requirements.
(3) Pipeline welding equipment has not been regularly calibrated, and there is a lack of corresponding welding equipment maintenance plans. For example, various performance parameters and instrument parameters on the welding equipment are inaccurate.
(4) The pipeline welding construction environment does not meet the welding conditions. For example, the welding voltage and current are unstable, and the construction weather temperature is low in winter, which will also affect the quality of pipeline welding.
3. External defects of pipeline welding and their causes
(1) Surface cracks: gaps left by the welding surface of the pipeline. Improper matching of pipeline materials and welding materials, or irregular pipeline welding process operations, leading to cracks on the surface of the pipe.
(2) Undercut: refers to the irregular notch in the base metal caused by welding at the weld toe. It is mostly due to improper selection of pipeline welding process parameters or incorrect welding operation methods of the welder, resulting in grooves or depressions along the direction of the fusion line on the base metal of the pipeline.
(3) Surface pores: refers to the pores left on the surface of the pipe. It is greatly affected by the pipeline welding process.
(4) Weld burr: During pipe welding, the molten metal flows to the unmelted base metal or the metal burr formed on the weld. The selected welding process parameters of the pipeline or the welding operation of the welder do not meet the requirements of the pipeline welding specifications, resulting in welding burrs.
(5) Welding deformation: During pipe welding, rapid non-equilibrium heating and cooling cause welding residual deformation of the structure. Due to the heating by welding, the pipe material expands, and then cools, and the pipe material shrinks. The plastic deformation of the material produced during the rapid changes in heating and cooling remains after the pipe welding is completed.
(6) Wrong sides: Two identical objects are not on the same plane after welding, one side is higher and the other is lower. This was caused by the lax inspection of entry pipelines, the welders’ inadequate understanding of the welding process regulations and their lack of proficiency in executing them.
4. Internal defects of pipeline welding and their causes:
(1) Internal pores: When the molten metal solidifies, the gas in it cannot escape and remains, forming cavities. During the pipeline welding process, the gas generated by the welding material itself or external gas enters the molten pool and fails to escape the molten pool in time before it solidifies and remains in the weld.
(2) Incomplete penetration: The root of the joint is not completely penetrated during pipe welding, or the depth of butt weld deposition does not meet the design requirements. It is caused by improper selection of pipeline welding process parameters, lack of standardization of pipeline bevel processing, or incorrect welding operation methods by welders.
(3) Lack of fusion: a defect in which the weld metal and the base metal, or the layers of the weld metal, are not combined together. The pipeline welding process parameters do not meet the requirements, or the cleaning of the grooves and interlayer parts does not meet the welding requirements.
(4) Slag inclusion: There are defects caused by slag in the weld metal. It is caused by improper selection of pipeline welding process parameters, incorrect welding operation methods by the welder, or failure to remove the slag from the pipeline welding joint.
5. Countermeasures for welding quality control of welded pipes
(1) Establish a complete pipeline welding quality management system
①Welding material control: Strictly control the purchase, acceptance, storage and use of welding materials.
②Welding equipment control: Prepare maintenance and calibration plans, calibrate and verify welding equipment on time and as required.
③Welding process control: Complete the welding process assessment according to the technical standards and design requirements of petrochemical construction projects.
④ Based on the conditions of the construction site, formulate pipeline welding process regulations, welding process cards and welding operation instructions, etc.
⑤Control of welding personnel: Hold certificates to work, weld in strict accordance with the process, and continuously improve the welding ability of welders.
⑥Welding environment control: When the welding environment affects normal pipeline welding, the welder should take effective protective measures in time or stop welding immediately.
(2) Strengthen the application of non-destructive testing technology
①Improve routine non-destructive testing applications
According to the material, size, structure, etc. of the inspection pipeline, documents such as non-destructive inspection technology construction plans, process regulations, and process cards are prepared. The professional and technical person in charge should provide technical explanations to the inspection personnel, require the inspection personnel to abide by relevant laws, regulations and inspection standards, guide the inspection personnel to correctly carry out non-destructive inspection of pipelines, and ensure the scientificity and accuracy of the inspection results.
In response to pipeline welding defects, inspectors should conduct careful analysis to find out pipeline welding defects and hidden dangers, and report the inspection results in a timely manner to achieve the purpose of pipeline welding quality control and ensure the safe operation of welded tubes. Innovative application of new non-destructive testing technologies By actively innovating new non-destructive testing technologies, we can achieve faster and more efficient welded tubes inspection results and ensure the safety and reliability of pipeline welding quality.
(3) Establish an information platform for pipeline welding quality management
①Establish an information platform for optimizing welding processes
Establish a pipeline welding process assessment information database and organize and classify welding process assessment reports for various materials and structures.
②Establish a welder file management platform
The welder file management platform should cover information such as welder number, welder certificate number, level, validity period, and pipeline welding completion status during the process. It should also include auxiliary modules such as quarterly assessment of welders, annual assessment, and skills training.
③Establish a database of information on the entire pipeline welding process
The database includes: non-destructive testing methods, pipeline construction acceptance specifications, welding methods, welding materials, welding joint types, welding defects, reasons for failure, inspection ratio, welder personnel and other information.
1. Defects and hazards in welding of welded pipes
(1) Common defects in welded tubes welding
Pipe surface defects: surface cracks, undercuts, surface pores, welding nodules, welding deformation, wrong edges, etc. Internal defects in pipeline welding: internal pores, slag inclusions, incomplete welding, lack of fusion, etc.
(2) The hazards of welding defects in welded tubes
Reducing the welding strength of pipeline welding interfaces will affect the appearance and forming quality of pipeline welds, and may cause leakage and material blockage in welded tubes.
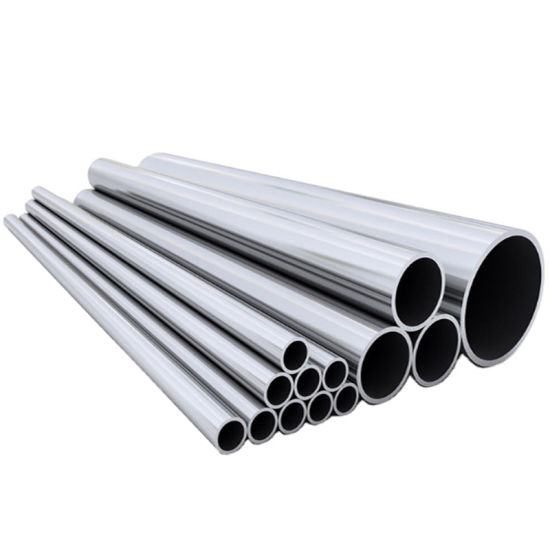
2. Factors affecting the welding quality of welded pipes
(1) The pipeline welding process is improperly selected.
(2) Pipeline welding workers lack quality awareness, lack welding technical capabilities, and fail to strictly implement welding process requirements.
(3) Pipeline welding equipment has not been regularly calibrated, and there is a lack of corresponding welding equipment maintenance plans. For example, various performance parameters and instrument parameters on the welding equipment are inaccurate.
(4) The pipeline welding construction environment does not meet the welding conditions. For example, the welding voltage and current are unstable, and the construction weather temperature is low in winter, which will also affect the quality of pipeline welding.
3. External defects of pipeline welding and their causes
(1) Surface cracks: gaps left by the welding surface of the pipeline. Improper matching of pipeline materials and welding materials, or irregular pipeline welding process operations, leading to cracks on the surface of the pipe.
(2) Undercut: refers to the irregular notch in the base metal caused by welding at the weld toe. It is mostly due to improper selection of pipeline welding process parameters or incorrect welding operation methods of the welder, resulting in grooves or depressions along the direction of the fusion line on the base metal of the pipeline.
(3) Surface pores: refers to the pores left on the surface of the pipe. It is greatly affected by the pipeline welding process.
(4) Weld burr: During pipe welding, the molten metal flows to the unmelted base metal or the metal burr formed on the weld. The selected welding process parameters of the pipeline or the welding operation of the welder do not meet the requirements of the pipeline welding specifications, resulting in welding burrs.
(5) Welding deformation: During pipe welding, rapid non-equilibrium heating and cooling cause welding residual deformation of the structure. Due to the heating by welding, the pipe material expands, and then cools, and the pipe material shrinks. The plastic deformation of the material produced during the rapid changes in heating and cooling remains after the pipe welding is completed.
(6) Wrong sides: Two identical objects are not on the same plane after welding, one side is higher and the other is lower. This was caused by the lax inspection of entry pipelines, the welders’ inadequate understanding of the welding process regulations and their lack of proficiency in executing them.
4. Internal defects of pipeline welding and their causes:
(1) Internal pores: When the molten metal solidifies, the gas in it cannot escape and remains, forming cavities. During the pipeline welding process, the gas generated by the welding material itself or external gas enters the molten pool and fails to escape the molten pool in time before it solidifies and remains in the weld.
(2) Incomplete penetration: The root of the joint is not completely penetrated during pipe welding, or the depth of butt weld deposition does not meet the design requirements. It is caused by improper selection of pipeline welding process parameters, lack of standardization of pipeline bevel processing, or incorrect welding operation methods by welders.
(3) Lack of fusion: a defect in which the weld metal and the base metal, or the layers of the weld metal, are not combined together. The pipeline welding process parameters do not meet the requirements, or the cleaning of the grooves and interlayer parts does not meet the welding requirements.
(4) Slag inclusion: There are defects caused by slag in the weld metal. It is caused by improper selection of pipeline welding process parameters, incorrect welding operation methods by the welder, or failure to remove the slag from the pipeline welding joint.
5. Countermeasures for welding quality control of welded pipes
(1) Establish a complete pipeline welding quality management system
①Welding material control: Strictly control the purchase, acceptance, storage and use of welding materials.
②Welding equipment control: Prepare maintenance and calibration plans, calibrate and verify welding equipment on time and as required.
③Welding process control: Complete the welding process assessment according to the technical standards and design requirements of petrochemical construction projects.
④ Based on the conditions of the construction site, formulate pipeline welding process regulations, welding process cards and welding operation instructions, etc.
⑤Control of welding personnel: Hold certificates to work, weld in strict accordance with the process, and continuously improve the welding ability of welders.
⑥Welding environment control: When the welding environment affects normal pipeline welding, the welder should take effective protective measures in time or stop welding immediately.
(2) Strengthen the application of non-destructive testing technology
①Improve routine non-destructive testing applications
According to the material, size, structure, etc. of the inspection pipeline, documents such as non-destructive inspection technology construction plans, process regulations, and process cards are prepared. The professional and technical person in charge should provide technical explanations to the inspection personnel, require the inspection personnel to abide by relevant laws, regulations and inspection standards, guide the inspection personnel to correctly carry out non-destructive inspection of pipelines, and ensure the scientificity and accuracy of the inspection results.
In response to pipeline welding defects, inspectors should conduct careful analysis to find out pipeline welding defects and hidden dangers, and report the inspection results in a timely manner to achieve the purpose of pipeline welding quality control and ensure the safe operation of welded tubes. Innovative application of new non-destructive testing technologies By actively innovating new non-destructive testing technologies, we can achieve faster and more efficient welded tubes inspection results and ensure the safety and reliability of pipeline welding quality.
(3) Establish an information platform for pipeline welding quality management
①Establish an information platform for optimizing welding processes
Establish a pipeline welding process assessment information database and organize and classify welding process assessment reports for various materials and structures.
②Establish a welder file management platform
The welder file management platform should cover information such as welder number, welder certificate number, level, validity period, and pipeline welding completion status during the process. It should also include auxiliary modules such as quarterly assessment of welders, annual assessment, and skills training.
③Establish a database of information on the entire pipeline welding process
The database includes: non-destructive testing methods, pipeline construction acceptance specifications, welding methods, welding materials, welding joint types, welding defects, reasons for failure, inspection ratio, welder personnel and other information.