1.Pressure test of black steel pipe for gas
During the pressure test of the black steel pipe for gas system, a U-shaped pressure gauge can be connected to the gas cock and the air inlet valve can be closed. Observe the pressure gauge reading. If the water column drops, there is a leak. Open the valve, release the gas, and use soapy water to check whether there are any leaks in the joints, flanges, valves, and gas meters to accurately find the leaks.
2. Direct observation
Direct observation during leak detection operations should cooperate with each other and coordinate the movements of hands, eyes, nose, and ears. Use your eyes to check whether there are soap bubbles bulging out of the interface coated with soapy water. If there is a gas smell, put your nose close to the interface and smell it directly. When the leakage is large, the soapy water can be blown away quickly without foaming. It can be heard with the ears. If there is a "clicking" sound, you can conclude that there is an air leak. In addition to listening to the smell on the back of the gas meter and other places where soap water is not easy to apply, you can also reach out and touch the back of the gas meter to test. When the leakage is serious, you can usually feel the leakage location with the back of your hand.
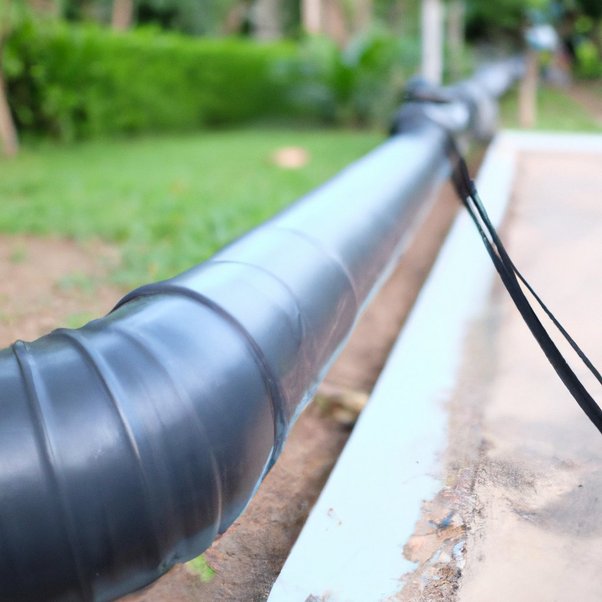
3. Leak detection drilling
First use professional testing equipment to find out the direction of black steel pipe for gas, then drill a hole in the ground at a certain distance (usually 2-6m), and use a sense of smell or a leak detector to check. When a gas leak is discovered, re-encrypt the hole, determine the more accurate leak point based on the intensity of the smell, and then break ground to find it. Guangzhou Gutejia has a very professional team that can conduct directional inspection of natural gas pipelines with very good results.
4. Dig a hole
Dig a hole where the black steel pipe or joint is, expose the pipe or joint, and check for leaks. The selection of pits should be analyzed in conjunction with various factors affecting pipeline leakage. If the pipeline passes through a roadway and sidewalk, a pit should be selected in the roadway, or it should be investigated whether other construction departments are working nearby. After digging the pit, even if no leakage point is found, the location of the leakage point can be roughly determined based on the intensity of the gas smell in the pit, thereby narrowing the search scope.
5. Block the ball and check for leaks
First drill 3 wire holes on the black steel pipe section with suspected leakage (ball installation holes on both sides, pressure measuring hole in the middle, the suspected leakage point is between the two ball installation holes), and then remove one end of the pressure measuring hose from the pressure measuring hole. The hole extends into the leak detection pipe section between the two balls, and then a ball is fed into each of the two ball-loading holes. After each ball is inflated and blocked, the pipe section to be tested forms a closed space. The pressure change of the measured pipe section can be known through the pressure measuring hose and U-shaped pressure gauge. If the pressure is relieved, you can also inflate air (preferably inert gas such as nitrogen) into the closed pipe section through a pressure measuring hose to increase the pressure, and observe the pressure changes. This allows for trial and error until the leak is identified. If the pressure is well stabilized during the test, it can be confirmed that the leakage point is not in the pipe section between the two balls, and you should continue to drill and block the balls to search.
During the pressure test of the black steel pipe for gas system, a U-shaped pressure gauge can be connected to the gas cock and the air inlet valve can be closed. Observe the pressure gauge reading. If the water column drops, there is a leak. Open the valve, release the gas, and use soapy water to check whether there are any leaks in the joints, flanges, valves, and gas meters to accurately find the leaks.
2. Direct observation
Direct observation during leak detection operations should cooperate with each other and coordinate the movements of hands, eyes, nose, and ears. Use your eyes to check whether there are soap bubbles bulging out of the interface coated with soapy water. If there is a gas smell, put your nose close to the interface and smell it directly. When the leakage is large, the soapy water can be blown away quickly without foaming. It can be heard with the ears. If there is a "clicking" sound, you can conclude that there is an air leak. In addition to listening to the smell on the back of the gas meter and other places where soap water is not easy to apply, you can also reach out and touch the back of the gas meter to test. When the leakage is serious, you can usually feel the leakage location with the back of your hand.
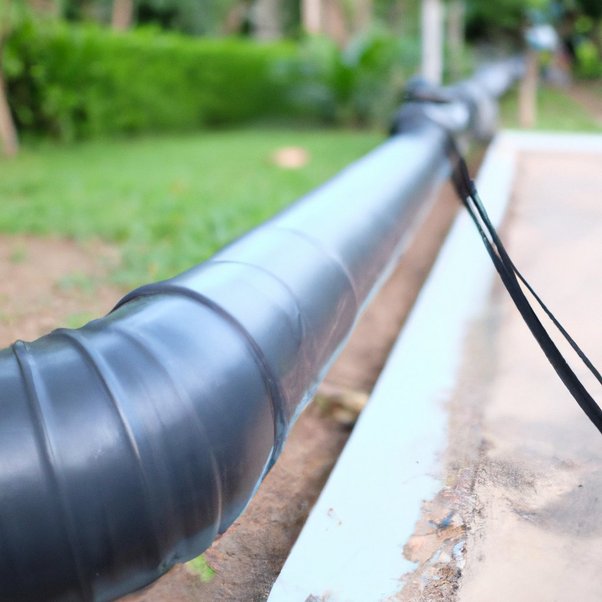
3. Leak detection drilling
First use professional testing equipment to find out the direction of black steel pipe for gas, then drill a hole in the ground at a certain distance (usually 2-6m), and use a sense of smell or a leak detector to check. When a gas leak is discovered, re-encrypt the hole, determine the more accurate leak point based on the intensity of the smell, and then break ground to find it. Guangzhou Gutejia has a very professional team that can conduct directional inspection of natural gas pipelines with very good results.
4. Dig a hole
Dig a hole where the black steel pipe or joint is, expose the pipe or joint, and check for leaks. The selection of pits should be analyzed in conjunction with various factors affecting pipeline leakage. If the pipeline passes through a roadway and sidewalk, a pit should be selected in the roadway, or it should be investigated whether other construction departments are working nearby. After digging the pit, even if no leakage point is found, the location of the leakage point can be roughly determined based on the intensity of the gas smell in the pit, thereby narrowing the search scope.
5. Block the ball and check for leaks
First drill 3 wire holes on the black steel pipe section with suspected leakage (ball installation holes on both sides, pressure measuring hole in the middle, the suspected leakage point is between the two ball installation holes), and then remove one end of the pressure measuring hose from the pressure measuring hole. The hole extends into the leak detection pipe section between the two balls, and then a ball is fed into each of the two ball-loading holes. After each ball is inflated and blocked, the pipe section to be tested forms a closed space. The pressure change of the measured pipe section can be known through the pressure measuring hose and U-shaped pressure gauge. If the pressure is relieved, you can also inflate air (preferably inert gas such as nitrogen) into the closed pipe section through a pressure measuring hose to increase the pressure, and observe the pressure changes. This allows for trial and error until the leak is identified. If the pressure is well stabilized during the test, it can be confirmed that the leakage point is not in the pipe section between the two balls, and you should continue to drill and block the balls to search.