Welded tube refers to the steel tube made of steel plates or steels that is welded after curling. Generally, the ruler is 6 meters. It has the advantages of simple production technology, high production efficiency, and many varieties. So what are the influencing factors during processing process?
The main parameters of welded tube processing process include welding thermal output, welding work pressure, welding rate, tensor angle size, direction and size of the electromagnetic induction coil, and the direction of characteristic impedances. These parameters have a great impact on the development of welded tube products, production efficiency, and production capacity of generator sets. Controlling various main parameters can make manufacturers get rich economic benefits.
1. Welding heat input
During the welding of welded tubes, the welding power determines amount of welding input heat. When the external conditions are certain and the input heat is insufficient, the edge of heated band steel cannot reach welding temperature, and it still maintains a solid -state tissue to form cold. Welding can not even melt.
During the test, this unf waters are usually manifested as unqualified testing tests, steel tubes burst during water pressure tests, or weld cracking when steel tubes are straight, which is a serious defect. In addition, the welding thermal input will also be affected by the quality of steel edge. For example, when the steel edge has burrs, the burrs before entering the squeezing roller will cause welding power loss, which will cause the welding power loss and reduce thermal input volume to reduce the heat input volume. Small, thereby forming an unbound or cold welding. When the input heat is too high, the edge of heated band steel exceeds the welding temperature, and it produces overheating or even over -burning. After the welding seam is stressed, it will crack. Sometimes, the welded metal splashing is caused by welding seams to form a hole.
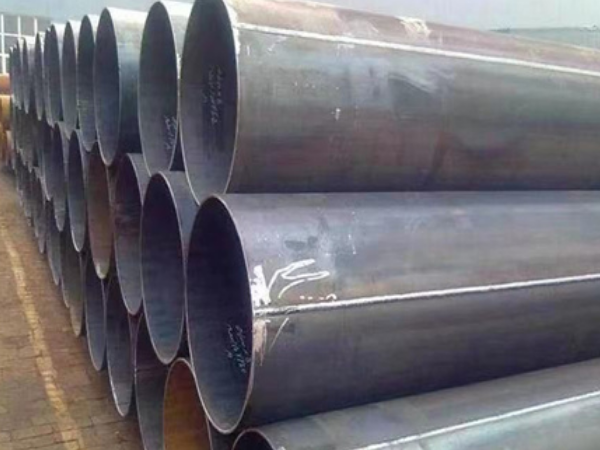
2. Welding pressure (reduced diameter)
The welding pressure is the main parameter of welding process. After the strip edge has been heated to welding temperature, the metal atoms are combined with each other under the action of extrusion rollers to form weld. The welding pressure size affects the strength and toughness of weld. If the welding pressure applied is small, the welding edges cannot be fully melted, and the metal oxides remaining in the weld cannot be discharged to form mixed, resulting in a great decrease in the tensile strength of weld. Most of the metals that reach welding temperature will be squeezed out, which not only reduces strength and toughness of weld, but also produces defects such as excessive inner and outer burrs or welding. The welding pressure is measured and judged by the change in the steel pipe dimension , the size and shape of burrs before and after squeeze roller.
3. Welding speed
The welding speed is also the main parameter of welding process, which is related to the heating system, the deformation speed of weld, and crystallization speed of the metal atomic atom. For high -frequency welding, the welding quality increases with speed of welding speed. This is because shortening of heating time makes the width of edge heating area narrowing, shortening the time for forming metal oxides; That is, welded heat affects the wider area, and the width of melting area changes with changes in the input heat, and the inner burrs formed are also large. The width of the melting line at different welding speeds. Low speed welding, due to the corresponding input heat to reduce will lead to welding difficulties, while the quality of plate edge and other external factors, such as the impact of magnetic impedance, the size of opening angle, etc., can easily cause a series of defects. Therefore high frequency welding, should be in the unit capacity and welding equipment allowed under the conditions of product specifications as far as possible to choose a faster welding speed for production.
4. Open angle
The opening angle, also known as the weld V angle, is the angle between edges of strip in front of extrusion roll. The size of opening angle is mainly determined by position and thickness of guide roller. The size of V horn has a greater impact on welding stability and welding quality. When reducing the V horn, the edge distance of steel will be reduced, which will strengthen the neighbor effect of high -frequency current, which can reduce welding power or increase welding speed and increase productivity. Too small opening corners will cause early welding, that is, the welding point is squeezed and fused when temperature is not reached. It is easy to form deficiency such as miscellaneous and cold welding in the weld, reducing the quality of weld. Increasing the V-angle increases power consumption, but under certain conditions ensures the stability of strip edge heating, reduces heat loss at the edge and reduces heat affected zone. In actual production, in order to ensure quality of welds, the V angle is generally controlled at 4 ° ~ 5 °.
5. The size and location of sensor ring
The induction rot is an important tool in high -frequency induction welding, and its size and position directly affect the efficiency of processing. The width of the induction ring is based on the outer diameter of the steel tube. If the inductive ring is too wide, the inductance will decrease, the voltage of the sensor will be reduced, and the output power will be reduced; the induction ring is too narrow, the output power increases, but the power loss of the back and the induction ring will also Increase. The width of the general induction ring is more appropriate for 1 to 1.5D (D is the outer diameter of the steel tube).
6. The role and location of impedance
Impedance rods are used to reduce the flow of high frequency currents to steel tube back. At the same time, concentrating current and the V angle of heating steel belt is ensured to ensure that the heat will not be lost due to heating tube. If the cooling is not in place, the magnetic rod will exceed its residential temperature (about 300 ° C) and get magnetized. If there is no impedance, the current and induced heat will be scattered around entire tube, which will increase welding power and cause tube to overheat. There is a thermal effect of an impeded device in the tube. The positioning position of the impedance has a great impact on welding speed and welding quality.