Thermal expansion welded tube is a common manufacturing process used to create a variety of pipes, fittings and equipment,such as ERW steel pipe and stainless welded steel pipe. This article will introduce the manufacturing process, principles and application of thermal expansion welded tubes in engineering.
Thermal expansion welded tube manufacturing process flow
Thermal expansion welded tube is to heat the metal pipe to a certain temperature through thermal processing, and then use mechanical force to expand the diameter, thereby changing its shape and size. The manufacturing process of thermally expanded welded tubes mainly includes the following steps:
1. Material preparation: Select appropriate metal materials as raw materials for thermal expansion welded tubes. Commonly used metal materials include copper, aluminum, stainless steel, etc. Determine material specifications and dimensions based on actual needs.
2. Heating treatment: Put the metal pipe into the heating furnace for heating treatment. The selection of temperature needs to be determined based on the properties of the metal material and the required pipe expansion effect. Normally, the heating temperature should bring the metal material to a plastic state.
3. Pipe expansion operation: Put the heated metal pipe into the pipe expander for pipe expansion operation. Pipe expanders gradually expand the diameter of metal pipes by applying mechanical force. The selection of pipe expander should be determined based on the specifications of the metal pipe and the required pipe expansion effect.
4. Cooling treatment: After the pipe expansion is completed, take out the metal pipe and perform cooling treatment. Cooling treatment can be carried out by natural cooling or water cooling.
5. Inspection and trimming: Inspect the expanded metal pipe to see if its size and shape meet the requirements. If necessary, trimming and adjustments can also be made to ensure product quality.
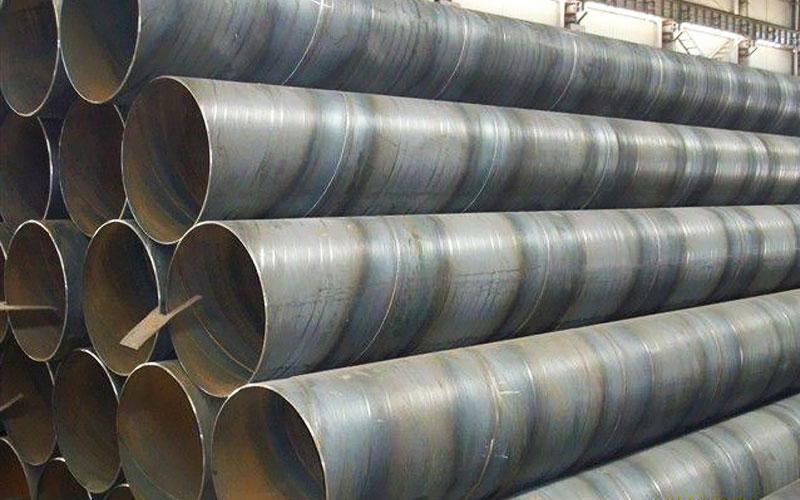
The principle of thermal expansion welded tube
The principle of thermal expansion welded tube is to utilize the thermoplastic and plastic deformation characteristics of metal materials. When a metal material is heated, its grain structure changes and its plasticity increases, so that it can be plastically deformed by applying mechanical force. By enlarging the diameter of the pipe, its shape and size can be changed to achieve the desired goal.
Application of thermal expansion welded tube
Thermal expansion welded tubes are widely used in various industries, especially in the engineering field. The following are several common applications of thermal expansion welded tubes in engineering:
1. Pipe system: Thermal expansion welded tube is often used to manufacture pipes and fittings in piping systems. Through the thermal expansion welded tube process, pipes of different specifications and materials can be connected to form a complete pipeline system.
2. Heat exchanger: Thermal expansion welded tube is also commonly used to manufacture pipes and tube bundles in heat exchangers. Thermal expansion welded tube can expand the diameter of the pipe, increase the contact area with the heat exchange medium, and improve the heat exchange efficiency.
3. Pressure vessels: Thermal expansion welded tubes can be used to manufacture pipes and shells in pressure vessels. By enlarging the diameter of the pipe, the internal volume of the container can be increased and its pressure-bearing capacity can be improved.
Thermal expansion welded tube manufacturing process flow
Thermal expansion welded tube is to heat the metal pipe to a certain temperature through thermal processing, and then use mechanical force to expand the diameter, thereby changing its shape and size. The manufacturing process of thermally expanded welded tubes mainly includes the following steps:
1. Material preparation: Select appropriate metal materials as raw materials for thermal expansion welded tubes. Commonly used metal materials include copper, aluminum, stainless steel, etc. Determine material specifications and dimensions based on actual needs.
2. Heating treatment: Put the metal pipe into the heating furnace for heating treatment. The selection of temperature needs to be determined based on the properties of the metal material and the required pipe expansion effect. Normally, the heating temperature should bring the metal material to a plastic state.
3. Pipe expansion operation: Put the heated metal pipe into the pipe expander for pipe expansion operation. Pipe expanders gradually expand the diameter of metal pipes by applying mechanical force. The selection of pipe expander should be determined based on the specifications of the metal pipe and the required pipe expansion effect.
4. Cooling treatment: After the pipe expansion is completed, take out the metal pipe and perform cooling treatment. Cooling treatment can be carried out by natural cooling or water cooling.
5. Inspection and trimming: Inspect the expanded metal pipe to see if its size and shape meet the requirements. If necessary, trimming and adjustments can also be made to ensure product quality.
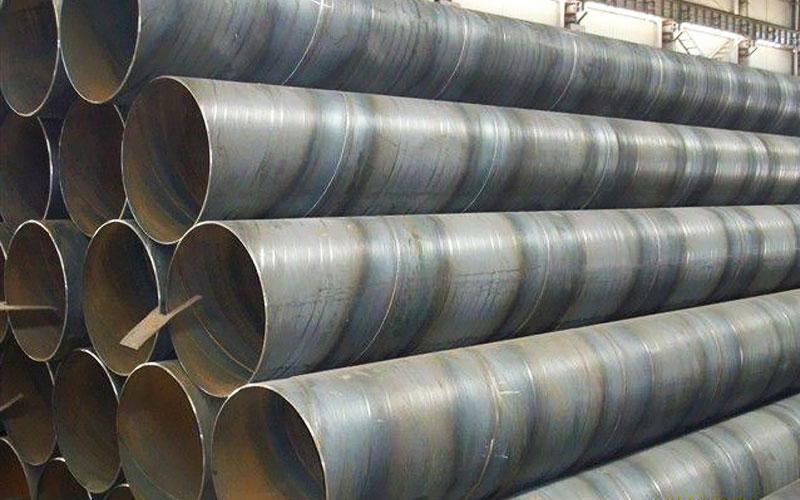
The principle of thermal expansion welded tube
The principle of thermal expansion welded tube is to utilize the thermoplastic and plastic deformation characteristics of metal materials. When a metal material is heated, its grain structure changes and its plasticity increases, so that it can be plastically deformed by applying mechanical force. By enlarging the diameter of the pipe, its shape and size can be changed to achieve the desired goal.
Application of thermal expansion welded tube
Thermal expansion welded tubes are widely used in various industries, especially in the engineering field. The following are several common applications of thermal expansion welded tubes in engineering:
1. Pipe system: Thermal expansion welded tube is often used to manufacture pipes and fittings in piping systems. Through the thermal expansion welded tube process, pipes of different specifications and materials can be connected to form a complete pipeline system.
2. Heat exchanger: Thermal expansion welded tube is also commonly used to manufacture pipes and tube bundles in heat exchangers. Thermal expansion welded tube can expand the diameter of the pipe, increase the contact area with the heat exchange medium, and improve the heat exchange efficiency.
3. Pressure vessels: Thermal expansion welded tubes can be used to manufacture pipes and shells in pressure vessels. By enlarging the diameter of the pipe, the internal volume of the container can be increased and its pressure-bearing capacity can be improved.
Previous:Steel casing coupling