OCTG casing running technology is a key link in oil and gas well construction. It is mainly used to isolate fluids in different formations to ensure the safety and production efficiency of the wellhead. This article will introduce the main measures of casing running technology, including casing selection, casing running technology, pressure control during casing running and cement cementing.
OCTG casing selection
OCTG casing is an important piece of equipment when running down a well. Choosing the right OCTG casing is of great significance to the integrity and safety of the wellhead. The selection of casing mainly considers the following aspects:
1. Strength and corrosion resistance: The casing needs to be strong enough to withstand the pressure from the formation and the liquid in the well, and at the same time have good corrosion resistance and be able to resist chemical corrosion in the formation.
2. Size and connection method: The size of the casing needs to be selected according to the diameter and depth of the wellbore to ensure that the casing and the wellbore can fully fit. In addition, the connection method of the casing also needs to be considered. Common connection methods include threaded connection and welded connection.
3. Sealing performance: The casing needs to have good sealing performance and can effectively isolate fluids in different formations.
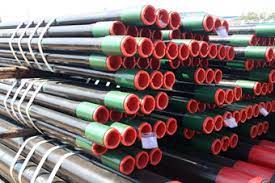
The OCTG casing running process involves the operation and control of wellhead equipment, and reasonable technical measures need to be designed to ensure the safe running of casing.
1. Design of the suspension device: The suspension device is the key equipment in the casing running process. It carries the weight of the casing and controls the casing running speed. The design of the suspension device needs to consider factors such as the quality, length and running speed of the casing to ensure that the suspension device can stably control the running of the casing.
2. Control of the running speed: The control of the casing running speed needs to be adjusted according to the shape and conditions of the wellbore. Too fast a running speed may cause impact force and cause damage to the casing, and too slow a running speed may cause damage to the casing. Increases operating time and costs. Therefore, the control of the descent speed needs to be reasonably adjusted according to the actual situation.
3. Pipeline cleaning and lubrication: Before running the casing, the well hole needs to be cleaned to ensure that there are no debris and residues in the well hole to prevent the casing from getting stuck or blocked. In addition, the casing needs to be lubricated to reduce friction and facilitate insertion.
Pressure control
Strict pressure control is required during casing running to prevent accidents at the wellhead.
1. Pressure monitoring: During the casing running process, it is necessary to monitor the pressure changes at the wellhead in real time.Commonly used pressure monitoring methods include pressure sensors and pressure gauges.
2. Pressure balance: In order to maintain the balance of the wellhead and avoid excessive pressure changes during casing running, measures such as adjusting mud density and operating wellhead equipment can be taken to achieve pressure balance.
3. Blast protection: During the casing running process, blast protection measures need to be taken to avoid explosion accidents at the wellhead. Common explosion protection measures include setting up explosion protectors, conducting safety inspections, and using explosion-proof tools.
Cement cementing
After the casing is completed, cement cementing is required to fix the wellhead, prevent cross-contamination, and block the formation.
1. Cement slurry design: The design of cement slurry needs to meet the requirements of cementing, including pressure support, sealing formation and fixed casing. The design of cement slurry mainly considers the density, fluidity, setting time and high temperature resistance of cement slurry.
2. Cementing operations: Cementing operations include the injection, exhausting and solidification of cement slurry. The injection process requires controlled flow and pressure to ensure that the cement slurry can completely fill the wellbore and fit tightly into the casing. The curing process requires maintaining a certain temperature and humidity to accelerate the solidification and hardening of cement.
OCTG casing selection
OCTG casing is an important piece of equipment when running down a well. Choosing the right OCTG casing is of great significance to the integrity and safety of the wellhead. The selection of casing mainly considers the following aspects:
1. Strength and corrosion resistance: The casing needs to be strong enough to withstand the pressure from the formation and the liquid in the well, and at the same time have good corrosion resistance and be able to resist chemical corrosion in the formation.
2. Size and connection method: The size of the casing needs to be selected according to the diameter and depth of the wellbore to ensure that the casing and the wellbore can fully fit. In addition, the connection method of the casing also needs to be considered. Common connection methods include threaded connection and welded connection.
3. Sealing performance: The casing needs to have good sealing performance and can effectively isolate fluids in different formations.
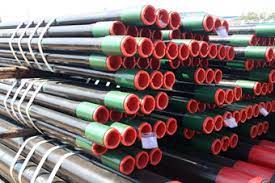
The OCTG casing running process involves the operation and control of wellhead equipment, and reasonable technical measures need to be designed to ensure the safe running of casing.
1. Design of the suspension device: The suspension device is the key equipment in the casing running process. It carries the weight of the casing and controls the casing running speed. The design of the suspension device needs to consider factors such as the quality, length and running speed of the casing to ensure that the suspension device can stably control the running of the casing.
2. Control of the running speed: The control of the casing running speed needs to be adjusted according to the shape and conditions of the wellbore. Too fast a running speed may cause impact force and cause damage to the casing, and too slow a running speed may cause damage to the casing. Increases operating time and costs. Therefore, the control of the descent speed needs to be reasonably adjusted according to the actual situation.
3. Pipeline cleaning and lubrication: Before running the casing, the well hole needs to be cleaned to ensure that there are no debris and residues in the well hole to prevent the casing from getting stuck or blocked. In addition, the casing needs to be lubricated to reduce friction and facilitate insertion.
Pressure control
Strict pressure control is required during casing running to prevent accidents at the wellhead.
1. Pressure monitoring: During the casing running process, it is necessary to monitor the pressure changes at the wellhead in real time.Commonly used pressure monitoring methods include pressure sensors and pressure gauges.
2. Pressure balance: In order to maintain the balance of the wellhead and avoid excessive pressure changes during casing running, measures such as adjusting mud density and operating wellhead equipment can be taken to achieve pressure balance.
3. Blast protection: During the casing running process, blast protection measures need to be taken to avoid explosion accidents at the wellhead. Common explosion protection measures include setting up explosion protectors, conducting safety inspections, and using explosion-proof tools.
Cement cementing
After the casing is completed, cement cementing is required to fix the wellhead, prevent cross-contamination, and block the formation.
1. Cement slurry design: The design of cement slurry needs to meet the requirements of cementing, including pressure support, sealing formation and fixed casing. The design of cement slurry mainly considers the density, fluidity, setting time and high temperature resistance of cement slurry.
2. Cementing operations: Cementing operations include the injection, exhausting and solidification of cement slurry. The injection process requires controlled flow and pressure to ensure that the cement slurry can completely fill the wellbore and fit tightly into the casing. The curing process requires maintaining a certain temperature and humidity to accelerate the solidification and hardening of cement.