oil drill pipe
The drill pipe is a steel pipe with ribbing at the end, which is used to connect the surface equipment of the drilling rig and the drilling and grinding equipment or bottom hole device at the bottom of the well. The purpose of the drill pipe is to transport the drilling mud to the drill bit and together with the drill bit raise, lower or rotate the bottom hole device. Drill pipe must be able to withstand enormous internal and external pressure, twisting, bending and vibration. In the process of oil and gas extraction and refining, drill pipe can be used many times.
The bare and raw steel pipes are made into drill pipes after several processing steps. First, through the processing of the steel pipe thickening process, the outer surface of the light pipe is bent inward, and the pipe wall of the steel pipe is thickened. The next step is threading and plating with copper for strength. A non-destructive quality control inspection is then carried out, followed by welding of the steel pipe body joint. Afterwards, the tube undergoes a welding heat treatment and welding final treatment to eliminate welding residual stress. Several other tests are performed on the finished steel pipe before Tips:The length of the drill pipe is generally about nine meters.
The role of drill pipe
1) Transmission of driving torque to the lower drilling tool
2) Transmission of drilling fluid
3) Hanging tools when dealing with underground accidents
Drill pipe manufacturing process
Heating - perforating - hot drawing - heating - sizing - straightening - testing - sawing - thickening - heat treatment - straightening - testing - bearing
Drill pipe quality control
(1) API does not clearly stipulate the chemical composition of drill pipe steel, but the content of sulfur (S) and phosphorus (P) cannot be more than 0.030%, and other elements are determined by the steel mill.Steelmaking level, process control and element ratio directly affect the purity of steel and the permeability of steel, and ultimately affect the comprehensive performance of drill pipe.
(2) The process, equipment and quality control level of the pipe rolling of the pipe body, the thickening of the pipe end and the mechanical processing of the joint (mainly thread processing) determine the geometric size of the drill pipe.
(3) The control level of heating control in the process of pipe rolling and pipe end thickening, overall heat treatment of pipe body, joint heat treatment and weld heat treatment directly affects the comprehensive mechanical properties of the finished drill pipe.Such as impact toughness, hardness distribution and fatigue resistance.
(4) The forming control level of the thickened inner transition zone at the pipe end is the main factor affecting the fatigue puncture of the drill pipe body.
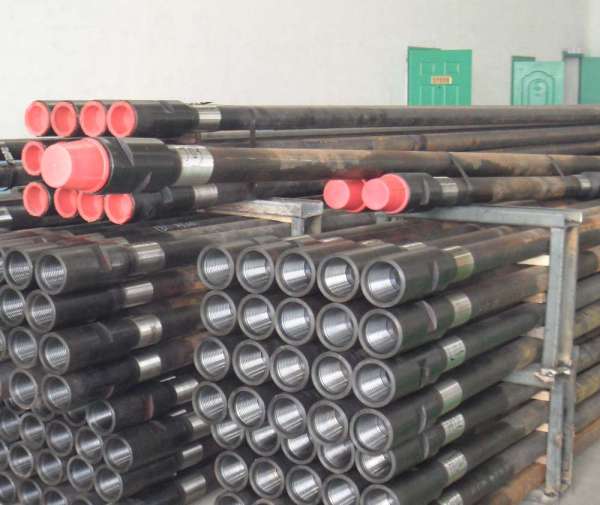
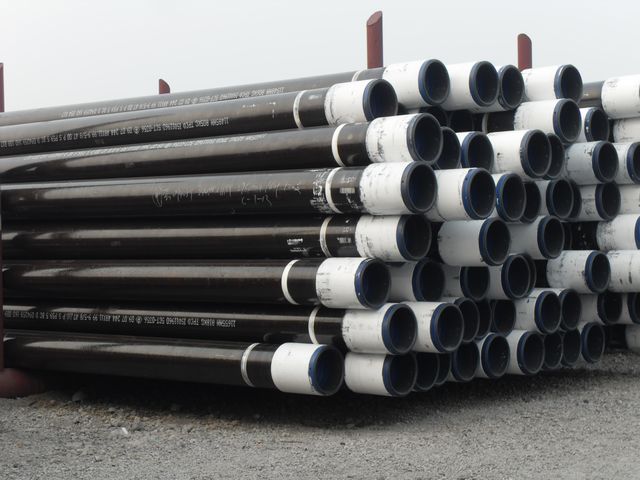
Oil Casing
The special oil pipe is mainly used for the drilling of oil and gas wells and the transportation of oil and gas. It includes oil drilling pipes, oil casings, and oil sucking pipes. Oil drill pipes are mainly used to connect drill collars and drill bits and transmit drilling power. The oil casing is mainly used to support the well wall during the drilling process and after the well completion, so as to ensure the drilling process and the normal operation of the entire oil well after the well completion. The oil pipe mainly transports the oil and gas at the bottom of the oil well to the surface. Casing can be divided into: conduit, surface casing, technical casing and oil casing according to the usage. Oil casing belongs to seamless pipe.
Oil casing is the lifeblood of keeping oil wells running. Due to different geological conditions, the downhole stress state is complex, and the comprehensive action of tension, compression, bending and torsional stress acts on the pipe body, which puts forward higher requirements on the quality of the casing itself. Once the casing itself is damaged for some reason, it may lead to the reduction of production of the entire well, or even to be scrapped.
The role of oil casing
1) Protect the drilling from contamination by shallow water layers and shallow gas layers, support wellhead equipment and maintain the weight of other layers of casing.
2) Separate the pressure at different levels so that the drilling fluid can flow normally and protect the production casing. In order to install anti-burst device, leak-proof device and tail pipe in the well.
3) Export oil and gas from subsurface reservoirs.
4) It is used to protect drilling and stratify drilling mud.
Production process of oil casing
Incoming inspection - thickening - heat treatment - quenching and tempering - phosphorus removal - straightening - blanking inspection - flaw detection and storage
Inspection of oil casing
(1) According to SY/T6194-96 regulations. The casing and its coupling are of the same steel grade. Sulfur content <0.045%, phosphorus content <0.045%.
(2) The first edition of ARISPEC5CT1988 of the American Petroleum Institute. Chemical analysis Prepare samples according to the latest version of ASTME59, and conduct chemical analysis according to the latest version of ASTME350
The drill pipe is a steel pipe with ribbing at the end, which is used to connect the surface equipment of the drilling rig and the drilling and grinding equipment or bottom hole device at the bottom of the well. The purpose of the drill pipe is to transport the drilling mud to the drill bit and together with the drill bit raise, lower or rotate the bottom hole device. Drill pipe must be able to withstand enormous internal and external pressure, twisting, bending and vibration. In the process of oil and gas extraction and refining, drill pipe can be used many times.
The bare and raw steel pipes are made into drill pipes after several processing steps. First, through the processing of the steel pipe thickening process, the outer surface of the light pipe is bent inward, and the pipe wall of the steel pipe is thickened. The next step is threading and plating with copper for strength. A non-destructive quality control inspection is then carried out, followed by welding of the steel pipe body joint. Afterwards, the tube undergoes a welding heat treatment and welding final treatment to eliminate welding residual stress. Several other tests are performed on the finished steel pipe before Tips:The length of the drill pipe is generally about nine meters.
The role of drill pipe
1) Transmission of driving torque to the lower drilling tool
2) Transmission of drilling fluid
3) Hanging tools when dealing with underground accidents
Drill pipe manufacturing process
Heating - perforating - hot drawing - heating - sizing - straightening - testing - sawing - thickening - heat treatment - straightening - testing - bearing
Drill pipe quality control
(1) API does not clearly stipulate the chemical composition of drill pipe steel, but the content of sulfur (S) and phosphorus (P) cannot be more than 0.030%, and other elements are determined by the steel mill.Steelmaking level, process control and element ratio directly affect the purity of steel and the permeability of steel, and ultimately affect the comprehensive performance of drill pipe.
(2) The process, equipment and quality control level of the pipe rolling of the pipe body, the thickening of the pipe end and the mechanical processing of the joint (mainly thread processing) determine the geometric size of the drill pipe.
(3) The control level of heating control in the process of pipe rolling and pipe end thickening, overall heat treatment of pipe body, joint heat treatment and weld heat treatment directly affects the comprehensive mechanical properties of the finished drill pipe.Such as impact toughness, hardness distribution and fatigue resistance.
(4) The forming control level of the thickened inner transition zone at the pipe end is the main factor affecting the fatigue puncture of the drill pipe body.
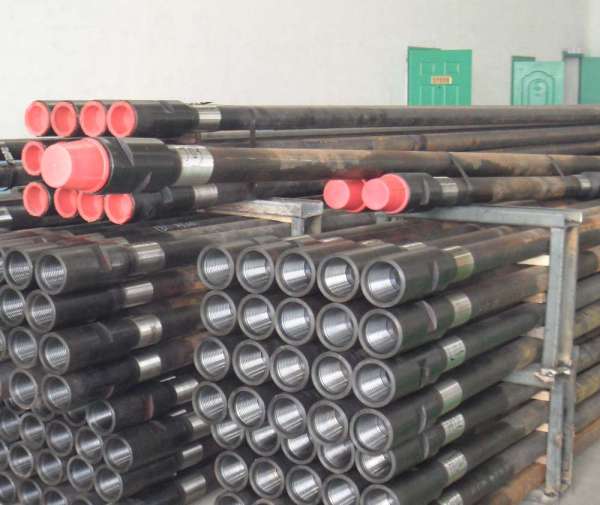
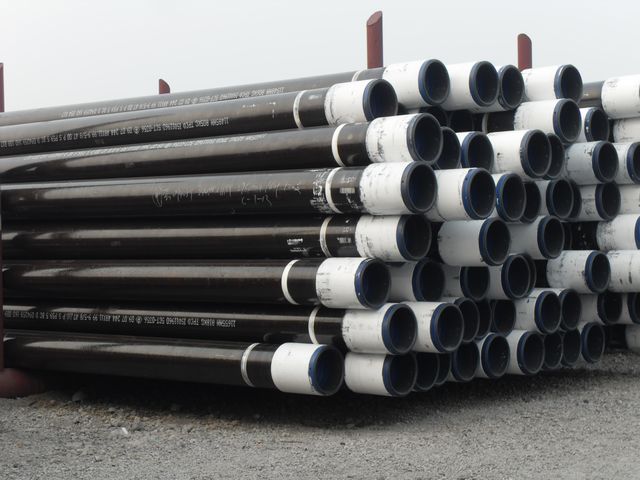
Oil Casing
The special oil pipe is mainly used for the drilling of oil and gas wells and the transportation of oil and gas. It includes oil drilling pipes, oil casings, and oil sucking pipes. Oil drill pipes are mainly used to connect drill collars and drill bits and transmit drilling power. The oil casing is mainly used to support the well wall during the drilling process and after the well completion, so as to ensure the drilling process and the normal operation of the entire oil well after the well completion. The oil pipe mainly transports the oil and gas at the bottom of the oil well to the surface. Casing can be divided into: conduit, surface casing, technical casing and oil casing according to the usage. Oil casing belongs to seamless pipe.
Oil casing is the lifeblood of keeping oil wells running. Due to different geological conditions, the downhole stress state is complex, and the comprehensive action of tension, compression, bending and torsional stress acts on the pipe body, which puts forward higher requirements on the quality of the casing itself. Once the casing itself is damaged for some reason, it may lead to the reduction of production of the entire well, or even to be scrapped.
The role of oil casing
1) Protect the drilling from contamination by shallow water layers and shallow gas layers, support wellhead equipment and maintain the weight of other layers of casing.
2) Separate the pressure at different levels so that the drilling fluid can flow normally and protect the production casing. In order to install anti-burst device, leak-proof device and tail pipe in the well.
3) Export oil and gas from subsurface reservoirs.
4) It is used to protect drilling and stratify drilling mud.
Production process of oil casing
Incoming inspection - thickening - heat treatment - quenching and tempering - phosphorus removal - straightening - blanking inspection - flaw detection and storage
Inspection of oil casing
(1) According to SY/T6194-96 regulations. The casing and its coupling are of the same steel grade. Sulfur content <0.045%, phosphorus content <0.045%.
(2) The first edition of ARISPEC5CT1988 of the American Petroleum Institute. Chemical analysis Prepare samples according to the latest version of ASTME59, and conduct chemical analysis according to the latest version of ASTME350