High frequency resistance welding process
High-frequency welding originated in the 1950s. It is a new welding process that uses the skin effect and adjacent effect generated by high-frequency current to connect steel plates and other metal materials. The emergence and maturity of high-frequency welding technology has directly promoted the huge development of the straight seam welded pipe industry, which is a key process in the production of ERW steel pipes. The quality of high-frequency welding directly affects the overall strength, quality level and production speed of welded pipe products
1. The basic principle of high frequency resistance welding
The so-called high frequency is relative to the AC current frequency of 50Hz, generally refers to the high frequency current of 50KHz~400KHz. When a high-frequency current passes through a metal conductor, two peculiar effects will occur: the skin effect and the proximity effect. High-frequency welding uses these two effects to weld steel pipes.
1) The skin effect means that when an alternating current of a certain frequency passes through the same conductor, the current density is not uniformly distributed on all sections of the conductor, but mainly concentrated on the surface of the conductor.That is, the density of the current on the surface of the conductor is high, and the density inside the conductor is low.
2) The proximity effect means that when high-frequency current flows in opposite directions in two adjacent conductors, the current will flow concentratedly to the edges of the two conductors that are close to each other.That is, the two conductors have an additional shorter side, and the current does not flow along the shorter route.
These two effects are the basis for realizing metal high-frequency welding. High-frequency welding uses the skin effect to concentrate the energy of high-frequency current on the surface of the steel pipe, and uses the proximity effect to control the location and range of the high-frequency current flow path. The speed of the current is very fast, and it can heat and melt the edges of the adjacent steel plates in a very short time, and realize the butt joint by extrusion.
2. Characteristics of high frequency resistance welding welding technology
1) Fast welding speed and high efficiency
2) The welding seam width is small, flat and smooth, and the appearance is beautiful
3) High weld strength and good machinability
3. The production process of electric resistance welded pipe
Slitting - Uncoiling - Strip Leveling - Head and Tail Shearing - Strip Butt Welding - Looper Storage - Forming - Welding - Deburring - Sizing - Flaw Detection - Flying Cutting - Preliminary Inspection - Steel Pipe Straightening - Pipe Section Processing - Hydrostatic Testing - Flaw Detection - Printing and Coating - Finished Products
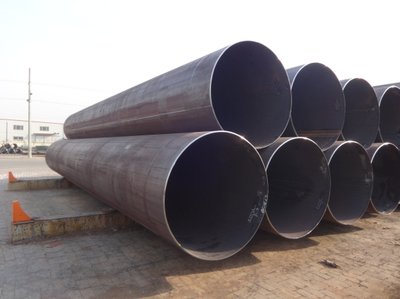
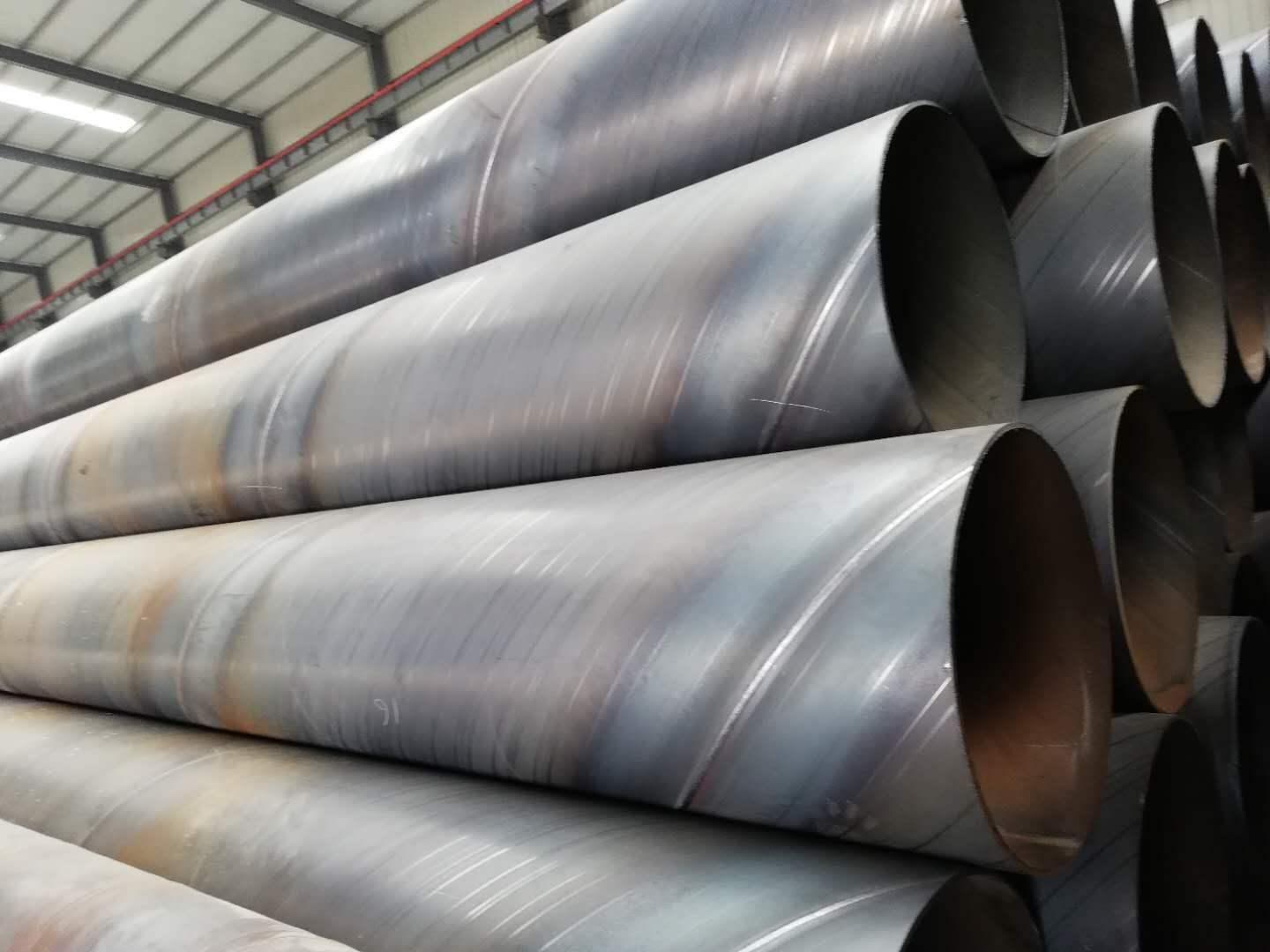
submerged arc welding process
Submerged arc welding (including submerged arc surfacing welding and electroslag surfacing welding, etc.) is a method in which the arc burns under the flux layer for welding. It is the welding process of LSAW steel pipe and SSAW steel pipe.Its inherent advantages of stable welding quality, high welding productivity, no arc and little smoke make it the main welding method in the production of important steel structures such as pressure vessels, pipe sections, box beams and columns.
1. Welding process of submerged arc welding
Submerged arc welding must do preparations before welding, including groove processing of the weldment, surface cleaning of the part to be welded, assembly of the weldment, cleaning of the surface of the welding wire, and drying of the flux.
①Bevel processing
Grooving ensures that there is no incomplete penetration or slag inclusion at the root of the weld, and reduces the amount of filler metal. The processing of the groove can use edge planing machine, mechanized or semi-mechanized gas cutting machine, carbon arc gouging and so on.
②Cleaning of the parts to be welded
Weldment cleaning is mainly to remove rust, oil and moisture, and prevent the generation of pores. Generally, sandblasting, shot peening or manual removal is used, and if necessary, the parts to be welded are baked with flame. Before welding, the groove, the 20mm area on both sides of the groove and the surface rust, oxide scale and oil stains on the part to be welded should be cleaned up.
③ Assembly of weldments
When assembling weldments, ensure that the gap is uniform, the height is flat, the amount of misalignment is small, the length of the tack weld is generally greater than 30mm, and the quality of the tack weld is consistent with the quality requirements of the main weld. Use special tooling and fixtures when necessary.For the assembly of straight seam weldments, arc-starting plates and lead-out plates should be installed at both ends of the weld, and then cut off after welding.Its purpose is to obtain the normal size of the weld section at the beginning and end of the welded joint, and it can also remove the defects that are prone to arc ignition and end.
④ Cleaning of welding materials
The welding wire and flux used in submerged arc welding have a great influence on the composition, structure and properties of the weld metal. Therefore, the oxide skin, rust and oil stains on the surface of the welding wire must be removed before welding. The flux should be protected from moisture when it is stored, and it must be dried at the specified temperature before use.
2. The main advantages of submerged arc automatic welding
(1) High productivity. The extension length of the welding wire of submerged arc welding (the length of the welding wire from the end of the contact tip to the end of the arc) is much shorter than that of the electrode of manual arc welding.Generally, it is about 50mm, and it is a light welding wire. It will not cause the redness of the electrode coating due to increasing the current. You can use a larger current (5-10 times larger than manual welding),Therefore, the penetration depth is large and the productivity is high. For butt welds below 20mm, there can be no groove and no gap, which reduces the amount of filler metal.
(2) The quality of the weld is high. The protection of the welding pool is relatively complete, and the impurities in the weld metal are less. As long as the welding process is properly selected, it is easier to obtain stable and high-quality welds.
(3) Good working conditions. In addition to reducing the labor intensity of manual operation, the arc arc is buried under the flux layer, and there is no arc radiation, so the working conditions are better. Submerged arc automatic welding is still the most commonly used welding method in industrial production. It is suitable for welding of larger batches, thicker and longer straight lines and larger diameter annular welds.
This method also has shortcomings. If it is not as flexible as manual welding, it is generally only suitable for welds with a horizontal position or a small inclination;Workpiece edge preparation and assembly quality requirements are high and labor-intensive;Since it is a submerged arc operation, the weld pool and seam formation cannot be seen, so the welding specification must be strictly controlled.
3. Process flow of spiral submerged arc welded pipe
SSAW spiral welded pipe is a welded steel tube made of strip steel coil as raw material, often warmly extruded, and welded by automatic double-wire double-sided submerged arc welding process.
1) Control the pipe diameter, misalignment and weld gap
2) The head and tail of the strip are butted by single wire or double wire submerged arc welding, and automatic submerged arc welding is used for repair welding after rolling into a steel pipe.
3) Ultrasonic flaw detection. If there is a defect, it will automatically alarm and spray the mark to eliminate the defect in time.
4) Leveling, trimming, planing, surface cleaning and conveying and pre-bending treatment.
5) Conveyor belt steel.
6) Check the mechanical properties, chemical composition, fusion condition of the weld, the surface quality of the steel pipe and the non-destructive inspection
7) Put into production.
4. Forming process of LSAW steel pipe
LSAW steel pipe is produced by pressing (rolling) a single medium and thick plate into a tube blank in a mold or a forming machine, using double-sided submerged arc welding and expanding the diameter.
1) UOE steel pipe: After the single steel plate is pre-bent at the edge, it undergoes U forming, O forming, internal welding, external welding, mechanical cold expansion and other processes.
2) JCOE steel pipe: that is, pre-welding, forming, and cold expansion after welding according to "J-C-O-E".
3) HME steel pipe: It is formed by the mandrel rolling method according to "C-C-O", and then cold expanded after welding.
High-frequency welding originated in the 1950s. It is a new welding process that uses the skin effect and adjacent effect generated by high-frequency current to connect steel plates and other metal materials. The emergence and maturity of high-frequency welding technology has directly promoted the huge development of the straight seam welded pipe industry, which is a key process in the production of ERW steel pipes. The quality of high-frequency welding directly affects the overall strength, quality level and production speed of welded pipe products
1. The basic principle of high frequency resistance welding
The so-called high frequency is relative to the AC current frequency of 50Hz, generally refers to the high frequency current of 50KHz~400KHz. When a high-frequency current passes through a metal conductor, two peculiar effects will occur: the skin effect and the proximity effect. High-frequency welding uses these two effects to weld steel pipes.
1) The skin effect means that when an alternating current of a certain frequency passes through the same conductor, the current density is not uniformly distributed on all sections of the conductor, but mainly concentrated on the surface of the conductor.That is, the density of the current on the surface of the conductor is high, and the density inside the conductor is low.
2) The proximity effect means that when high-frequency current flows in opposite directions in two adjacent conductors, the current will flow concentratedly to the edges of the two conductors that are close to each other.That is, the two conductors have an additional shorter side, and the current does not flow along the shorter route.
These two effects are the basis for realizing metal high-frequency welding. High-frequency welding uses the skin effect to concentrate the energy of high-frequency current on the surface of the steel pipe, and uses the proximity effect to control the location and range of the high-frequency current flow path. The speed of the current is very fast, and it can heat and melt the edges of the adjacent steel plates in a very short time, and realize the butt joint by extrusion.
2. Characteristics of high frequency resistance welding welding technology
1) Fast welding speed and high efficiency
2) The welding seam width is small, flat and smooth, and the appearance is beautiful
3) High weld strength and good machinability
3. The production process of electric resistance welded pipe
Slitting - Uncoiling - Strip Leveling - Head and Tail Shearing - Strip Butt Welding - Looper Storage - Forming - Welding - Deburring - Sizing - Flaw Detection - Flying Cutting - Preliminary Inspection - Steel Pipe Straightening - Pipe Section Processing - Hydrostatic Testing - Flaw Detection - Printing and Coating - Finished Products
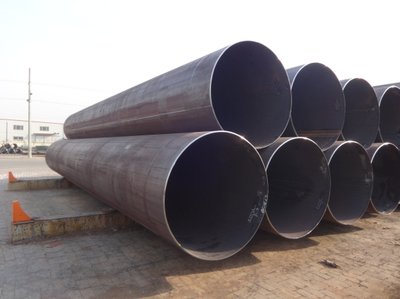
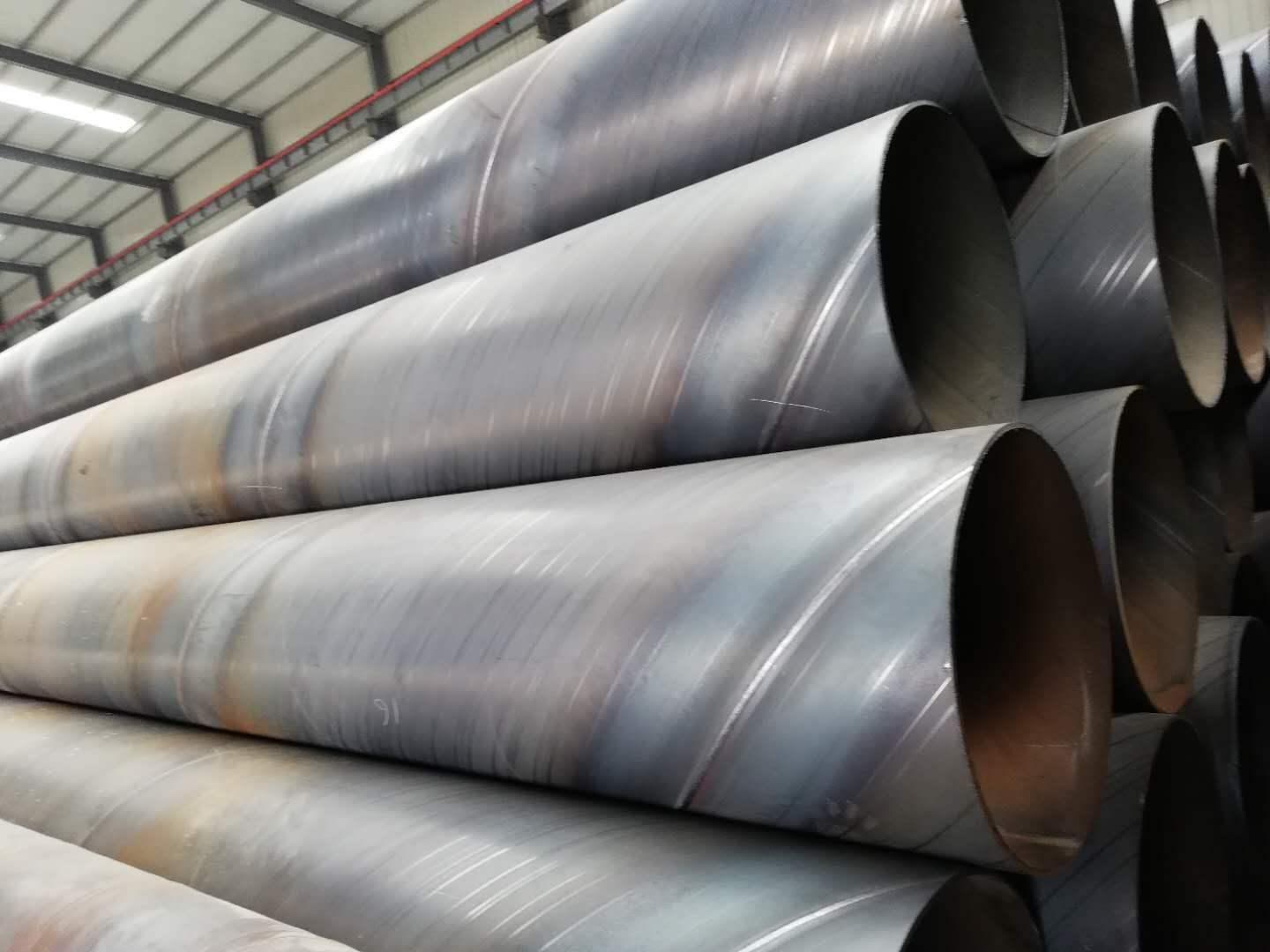
submerged arc welding process
Submerged arc welding (including submerged arc surfacing welding and electroslag surfacing welding, etc.) is a method in which the arc burns under the flux layer for welding. It is the welding process of LSAW steel pipe and SSAW steel pipe.Its inherent advantages of stable welding quality, high welding productivity, no arc and little smoke make it the main welding method in the production of important steel structures such as pressure vessels, pipe sections, box beams and columns.
1. Welding process of submerged arc welding
Submerged arc welding must do preparations before welding, including groove processing of the weldment, surface cleaning of the part to be welded, assembly of the weldment, cleaning of the surface of the welding wire, and drying of the flux.
①Bevel processing
Grooving ensures that there is no incomplete penetration or slag inclusion at the root of the weld, and reduces the amount of filler metal. The processing of the groove can use edge planing machine, mechanized or semi-mechanized gas cutting machine, carbon arc gouging and so on.
②Cleaning of the parts to be welded
Weldment cleaning is mainly to remove rust, oil and moisture, and prevent the generation of pores. Generally, sandblasting, shot peening or manual removal is used, and if necessary, the parts to be welded are baked with flame. Before welding, the groove, the 20mm area on both sides of the groove and the surface rust, oxide scale and oil stains on the part to be welded should be cleaned up.
③ Assembly of weldments
When assembling weldments, ensure that the gap is uniform, the height is flat, the amount of misalignment is small, the length of the tack weld is generally greater than 30mm, and the quality of the tack weld is consistent with the quality requirements of the main weld. Use special tooling and fixtures when necessary.For the assembly of straight seam weldments, arc-starting plates and lead-out plates should be installed at both ends of the weld, and then cut off after welding.Its purpose is to obtain the normal size of the weld section at the beginning and end of the welded joint, and it can also remove the defects that are prone to arc ignition and end.
④ Cleaning of welding materials
The welding wire and flux used in submerged arc welding have a great influence on the composition, structure and properties of the weld metal. Therefore, the oxide skin, rust and oil stains on the surface of the welding wire must be removed before welding. The flux should be protected from moisture when it is stored, and it must be dried at the specified temperature before use.
2. The main advantages of submerged arc automatic welding
(1) High productivity. The extension length of the welding wire of submerged arc welding (the length of the welding wire from the end of the contact tip to the end of the arc) is much shorter than that of the electrode of manual arc welding.Generally, it is about 50mm, and it is a light welding wire. It will not cause the redness of the electrode coating due to increasing the current. You can use a larger current (5-10 times larger than manual welding),Therefore, the penetration depth is large and the productivity is high. For butt welds below 20mm, there can be no groove and no gap, which reduces the amount of filler metal.
(2) The quality of the weld is high. The protection of the welding pool is relatively complete, and the impurities in the weld metal are less. As long as the welding process is properly selected, it is easier to obtain stable and high-quality welds.
(3) Good working conditions. In addition to reducing the labor intensity of manual operation, the arc arc is buried under the flux layer, and there is no arc radiation, so the working conditions are better. Submerged arc automatic welding is still the most commonly used welding method in industrial production. It is suitable for welding of larger batches, thicker and longer straight lines and larger diameter annular welds.
This method also has shortcomings. If it is not as flexible as manual welding, it is generally only suitable for welds with a horizontal position or a small inclination;Workpiece edge preparation and assembly quality requirements are high and labor-intensive;Since it is a submerged arc operation, the weld pool and seam formation cannot be seen, so the welding specification must be strictly controlled.
3. Process flow of spiral submerged arc welded pipe
SSAW spiral welded pipe is a welded steel tube made of strip steel coil as raw material, often warmly extruded, and welded by automatic double-wire double-sided submerged arc welding process.
1) Control the pipe diameter, misalignment and weld gap
2) The head and tail of the strip are butted by single wire or double wire submerged arc welding, and automatic submerged arc welding is used for repair welding after rolling into a steel pipe.
3) Ultrasonic flaw detection. If there is a defect, it will automatically alarm and spray the mark to eliminate the defect in time.
4) Leveling, trimming, planing, surface cleaning and conveying and pre-bending treatment.
5) Conveyor belt steel.
6) Check the mechanical properties, chemical composition, fusion condition of the weld, the surface quality of the steel pipe and the non-destructive inspection
7) Put into production.
4. Forming process of LSAW steel pipe
LSAW steel pipe is produced by pressing (rolling) a single medium and thick plate into a tube blank in a mold or a forming machine, using double-sided submerged arc welding and expanding the diameter.
1) UOE steel pipe: After the single steel plate is pre-bent at the edge, it undergoes U forming, O forming, internal welding, external welding, mechanical cold expansion and other processes.
2) JCOE steel pipe: that is, pre-welding, forming, and cold expansion after welding according to "J-C-O-E".
3) HME steel pipe: It is formed by the mandrel rolling method according to "C-C-O", and then cold expanded after welding.
Previous:Oil drill pipe VS oil casing