Driving pile foundations is an important process in engineering construction. However, due to the wide variety of pile foundations, such as steel sheet piles and steel pipe piles, the construction techniques of various pile foundations are greatly different, and the construction stratum structure is complex, so pile foundation construction is very prone to quality problems. Therefore, during the pile foundation construction process, relevant requirements should be strictly followed. At the same time, if problems are found, appropriate measures should be taken in time to deal with them.
Preventive and Cure Measures for Broken Pipe Piles
① When making concrete pipe piles, ensure the aggregate gradation and concrete workability, and the concrete pouring time and interval time should not be greater than the initial setting time of concrete. At the same time, the piles should also ensure that they meet the requirements for strength and straightness.
② For pile foundations with quicksand layers, admixtures with low density, good viscosity and strong wall-fixing ability should be added, such as bentonite, hydroxycellulose, chromium iron lignin sulfonate sodium salt, coal alkali agent, sodium carbonate, etc. To enhance the bonding properties of mud.
③ Excessive pile density should be avoided, and the spacing between vibrating piles should not be greater than 4 times the pile diameter. However, if the pile spacing is less than 3.5 times the pile diameter, the time interval for adjacent pile construction should be controlled.
Preventive and Cure Measures for Grout Leakage from Pipe Piles
① The amount of clay should be appropriately increased, the density of the mud should be adjusted, and the clay should be used to backfill the surroundings of the casing tightly to prevent leakage of slurry at the joints at the bottom of the cylinder. Kelier chemical mud contains leakage plugging agent, which can effectively prevent slurry leakage in the sand layer.
② A slow drilling construction method should be adopted before and after the drill bit passes through the casing to reduce the height of the hammer lift and ensure the mud wall protection effect, thereby avoiding excessive vibration that may cause liquefaction of the sand layer and leakage of slurry.
③ When slurry leakage is found in pipe piles, if the slurry leakage at the joints is not serious, cotton or batting can be used to block the joints to seal the joints; if the water leakage is serious, the casing must be dug out and re-buried after the repairs are complete.
Prevention and control measures for piling pipe necking
① The condition of the soil layer should be determined before drilling. If there is a weak layer or plastic soil, the hole should be swept to expand the hole diameter; if there is a soil layer with adverse geological conditions such as water expansion, the water loss rate should be less than 3~ 5mL/30min mud is used to protect the wall to reduce water loss.
② The extubation speed should be controlled. It should be 1m/min for general soil layers and 0.3~0.8m/min for the junction of soft soil layers and soft and hard soil layers.
③ During the construction process, the drill bits should be checked in time. If wear occurs, the drill bits with more wear should be repaired and expanded to reach the designed pile diameter.
Preventive and cure measures for pipe pile collapse
① When embedding the casing, clay should be tamped at the bottom and around the casing, and backfilled evenly around the casing. At the same time, the joints between the casings should be sealed to ensure the stability of the casing.
② When punching holes in loose silt soil or quicksand, mud or high-quality mud with a larger relative density, viscosity, and colloid ratio should be used, and the footage speed should be controlled.
③When lifting the drill bit and lowering the steel cage, insert it vertically into the center of the hole and keep it vertical to prevent touching the hole wall.
During pile foundation construction, the pile position is often deflected due to uneven construction sites, hard obstacles encountered during pile sinking, unstable drilling rig chassis, uneven settlement during drilling, etc.
Prevention and control measures for partial piles
① After laying out the lines, the points placed must be protected to avoid pile position deviation due to rolling by the drilling rig. Piling construction should be carried out after verifying the pile position and calibrating it with the surrounding piles.
② The piling site should be compacted and leveled, and the pile cap, pile body and pile tip should be ensured to be in a vertical line. Piling can only be driven after passing the inspection. At the same time, when sinking the pile, hammer it gently and slowly to ensure that the pile connection is vertical.
③If you encounter obstacles such as old foundations and large rocks in the shallow part that cannot be removed, you should first use a drill to drill through the obstacles, and then implant the piles into the holes for pile sinking, and the verticality of the drilled holes will deviate No more than 0.5% of hole depth.
1. Common problems in pipe pile foundation construction
(1)Broken pile
During pile foundation construction, the pile body often breaks due to insufficient strength of the concrete used to make the pile; deviations in the position of the pile lifting point or fulcrum; encountering hard obstacles when sinking the pile; excessive hammering force or too many times when sinking the pile, etc. Phenomenon.Preventive and Cure Measures for Broken Pipe Piles
① When making concrete pipe piles, ensure the aggregate gradation and concrete workability, and the concrete pouring time and interval time should not be greater than the initial setting time of concrete. At the same time, the piles should also ensure that they meet the requirements for strength and straightness.
② For pile foundations with quicksand layers, admixtures with low density, good viscosity and strong wall-fixing ability should be added, such as bentonite, hydroxycellulose, chromium iron lignin sulfonate sodium salt, coal alkali agent, sodium carbonate, etc. To enhance the bonding properties of mud.
③ Excessive pile density should be avoided, and the spacing between vibrating piles should not be greater than 4 times the pile diameter. However, if the pile spacing is less than 3.5 times the pile diameter, the time interval for adjacent pile construction should be controlled.
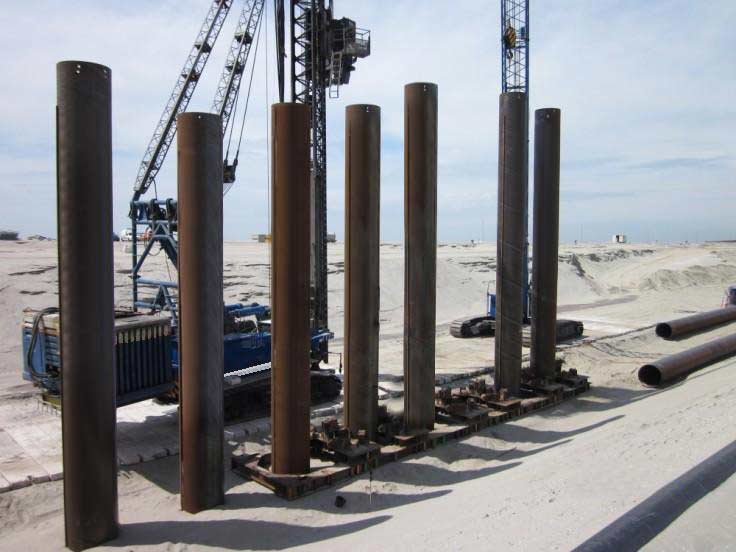
(2) Leakage slurry
During pile foundation construction, slurry leakage is often caused by the casing being buried too shallowly, the joints not being tight, the backfill soil not being compacted enough, gaps in the rocks or caves in the formation, etc. The main manifestations are bubbles or turbidity emerging from the water surface outside the casing. water.Preventive and Cure Measures for Grout Leakage from Pipe Piles
① The amount of clay should be appropriately increased, the density of the mud should be adjusted, and the clay should be used to backfill the surroundings of the casing tightly to prevent leakage of slurry at the joints at the bottom of the cylinder. Kelier chemical mud contains leakage plugging agent, which can effectively prevent slurry leakage in the sand layer.
② A slow drilling construction method should be adopted before and after the drill bit passes through the casing to reduce the height of the hammer lift and ensure the mud wall protection effect, thereby avoiding excessive vibration that may cause liquefaction of the sand layer and leakage of slurry.
③ When slurry leakage is found in pipe piles, if the slurry leakage at the joints is not serious, cotton or batting can be used to block the joints to seal the joints; if the water leakage is serious, the casing must be dug out and re-buried after the repairs are complete.
(3) Neck
During pile foundation construction, necking often occurs because the drill bit wears too fast and is not repaired in time, the pipe is pulled out too fast, the wall mud has poor performance, the concrete is not poured in time after the hole is formed, and the drilling footage is drilled too fast.
Prevention and control measures for piling pipe necking
① The condition of the soil layer should be determined before drilling. If there is a weak layer or plastic soil, the hole should be swept to expand the hole diameter; if there is a soil layer with adverse geological conditions such as water expansion, the water loss rate should be less than 3~ 5mL/30min mud is used to protect the wall to reduce water loss.
② The extubation speed should be controlled. It should be 1m/min for general soil layers and 0.3~0.8m/min for the junction of soft soil layers and soft and hard soil layers.
③ During the construction process, the drill bits should be checked in time. If wear occurs, the drill bits with more wear should be repaired and expanded to reach the designed pile diameter.
(4)Collapse hole
During pile foundation construction, pile holes often collapse due to insufficient mud density, too shallow a casing, improper hole cleaning, collision with the hole wall when lifting the drill bit and hoisting the steel cage, or too long dry drilling time.Preventive and cure measures for pipe pile collapse
① When embedding the casing, clay should be tamped at the bottom and around the casing, and backfilled evenly around the casing. At the same time, the joints between the casings should be sealed to ensure the stability of the casing.
② When punching holes in loose silt soil or quicksand, mud or high-quality mud with a larger relative density, viscosity, and colloid ratio should be used, and the footage speed should be controlled.
③When lifting the drill bit and lowering the steel cage, insert it vertically into the center of the hole and keep it vertical to prevent touching the hole wall.
(5) Offset pile
During pile foundation construction, the pile position is often deflected due to uneven construction sites, hard obstacles encountered during pile sinking, unstable drilling rig chassis, uneven settlement during drilling, etc.Prevention and control measures for partial piles
① After laying out the lines, the points placed must be protected to avoid pile position deviation due to rolling by the drilling rig. Piling construction should be carried out after verifying the pile position and calibrating it with the surrounding piles.
② The piling site should be compacted and leveled, and the pile cap, pile body and pile tip should be ensured to be in a vertical line. Piling can only be driven after passing the inspection. At the same time, when sinking the pile, hammer it gently and slowly to ensure that the pile connection is vertical.
③If you encounter obstacles such as old foundations and large rocks in the shallow part that cannot be removed, you should first use a drill to drill through the obstacles, and then implant the piles into the holes for pile sinking, and the verticality of the drilled holes will deviate No more than 0.5% of hole depth.