The main reason for cracks in seamless steel pipes is that there are defects such as pores/cracks on the inner and outer surfaces, and the reasons for these defects are as follows.
1. Raw materials
In order to save costs, some seamless steel pipe manufacturers will use round steel produced by small steel mills for processing, but these round steel will contain a lot of impurities, air bubbles and other problems, resulting in interlayers, pores and other problems inside the seamless steel pipe.After post-processing, there will be cracking problems.
2. The temperature control of heat treatment is not in place
Some manufacturers do not have rich production experience. Judging by the experience of workshop workers alone in terms of heating temperature and duration, it is impossible to guarantee whether the heat treatment of seamless steel pipes is in place. However, heat treatment will change the mechanical properties of seamless steel pipes, and ordinary manufacturers cannot judge whether seamless steel pipes have reached the performance indicators required by customers.
3. Straightening
In the process of straightening, if the straightening force is too large, it will also cause internal damage and cracks in the steel pipe.
4. Pulling
If the deformation of the drawing is too large, cracks in the steel pipe will also be formed, which will cause the steel pipe to crack during the later processing.
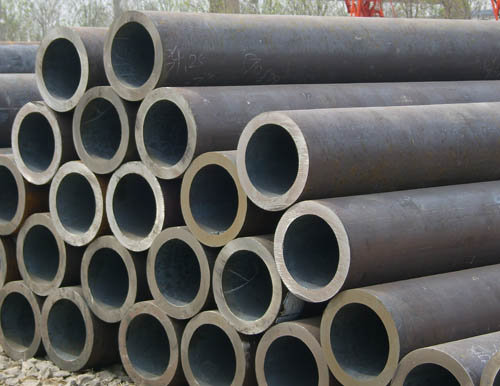
Solution
Rolling seamless steel pipes should focus on operating in strict accordance with the construction specifications and technical requirements related to indirect technology, rather than processing and repairing after cracks.For metals of special materials and new steel grades, tests should be carried out before rolling to find a more practical probe technology for review to ensure the welding quality. If there are cracks, the following methods can be used to deal with them
1) Check all cracks by means of non-destructive testing to determine the correct location.
2) The repaired welder should hold the corresponding project certificate, and the repair must be qualified once.
3) The welding environment must meet the welding requirements during repair, such as temperature, water, wind speed, etc.
4) The removal of welding defects can be carried out by mechanical methods such as a portable grinder, and cannot be cut by fire.
5) Select the filler material that meets the technical specifications, that is, the welding rod, and use it after drying according to the regulations.
6) The welding method and welding parameters used in the repair must follow the relevant welding specifications.
7) After repair, the welder must number next to the repair location and sign the welding repair record.
8) 100% x-ray damage inspection is carried out on the repaired welding, and the results are archived.
1. Raw materials
In order to save costs, some seamless steel pipe manufacturers will use round steel produced by small steel mills for processing, but these round steel will contain a lot of impurities, air bubbles and other problems, resulting in interlayers, pores and other problems inside the seamless steel pipe.After post-processing, there will be cracking problems.
2. The temperature control of heat treatment is not in place
Some manufacturers do not have rich production experience. Judging by the experience of workshop workers alone in terms of heating temperature and duration, it is impossible to guarantee whether the heat treatment of seamless steel pipes is in place. However, heat treatment will change the mechanical properties of seamless steel pipes, and ordinary manufacturers cannot judge whether seamless steel pipes have reached the performance indicators required by customers.
3. Straightening
In the process of straightening, if the straightening force is too large, it will also cause internal damage and cracks in the steel pipe.
4. Pulling
If the deformation of the drawing is too large, cracks in the steel pipe will also be formed, which will cause the steel pipe to crack during the later processing.
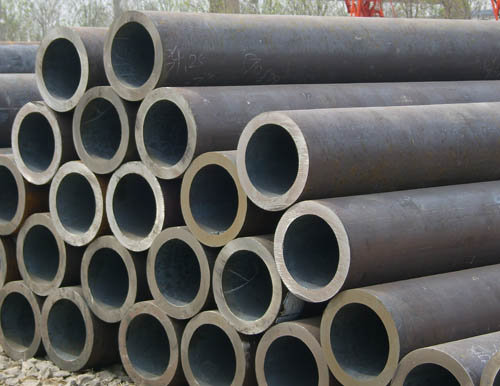
Solution
Rolling seamless steel pipes should focus on operating in strict accordance with the construction specifications and technical requirements related to indirect technology, rather than processing and repairing after cracks.For metals of special materials and new steel grades, tests should be carried out before rolling to find a more practical probe technology for review to ensure the welding quality. If there are cracks, the following methods can be used to deal with them
1) Check all cracks by means of non-destructive testing to determine the correct location.
2) The repaired welder should hold the corresponding project certificate, and the repair must be qualified once.
3) The welding environment must meet the welding requirements during repair, such as temperature, water, wind speed, etc.
4) The removal of welding defects can be carried out by mechanical methods such as a portable grinder, and cannot be cut by fire.
5) Select the filler material that meets the technical specifications, that is, the welding rod, and use it after drying according to the regulations.
6) The welding method and welding parameters used in the repair must follow the relevant welding specifications.
7) After repair, the welder must number next to the repair location and sign the welding repair record.
8) 100% x-ray damage inspection is carried out on the repaired welding, and the results are archived.