Steel plate cutting is the main method of modern plate processing. Without steel plate cutting, many plates cannot realize their value. Therefore, whether it is as small as people's daily necessities or as large as the construction of industrial buildings, steel plate cutting has played a great role in promoting it.
There are many types of steel plates on the market now. For example, according to its thickness, there are thin plates, medium plates, thick plates, and extra-thick plates; according to raw materials, it can be divided into carbon steel plate and stainless steel plate,etc. according to the production method, there are hot-rolled steel plates and cold-rolled steel plates; according to surface characteristics: galvanized plates, tin plate, composite steel plate, color-coated steel plate; classified by use, there are bridge steel plates, boiler steel plates, shipbuilding steel plates, spring steel plates, etc. Since there are so many types of steel plates, the cutting methods of steel plates must naturally keep up.
The choice of steel plate cutting method depends on the situation. In addition to laser cutting, there are also water cutting, plasma cutting, wire cutting and other methods. In what scenarios are they used? Detailed answer below.
An engineer engaged in the cutting field said this:
(1) Nowadays, the mainstream fiber lasers in the market, carbon dioxide lasers are slowly being phased out because they consume too much energy. However, there is still a market in the non-metallic field.
(2) Nowadays, since the domestic production of lasers, the price of optical fiber equipment in the medium and low power range has dropped sharply.
(3) For cutting methods other than laser, the market demand for plasma and wire cutting is relatively large, but wire cutting targets many mold industries. Plasma has more demand when it comes to thick plates or low precision requirements, and water jet cutting has more demand. Nowadays it is not common in the metal industry and there are many in the non-metal industry.
(4) In the future development, laser cutting will definitely dominate the metal sheet, and non-metal cutting will also occupy a large part of the market.
(1)Laser cutting processing
Laser cutting uses a focused high-power density laser beam to irradiate the workpiece, causing the irradiated material to quickly melt, vaporize, ablate or reach the ignition point. At the same time, the molten material is blown away by a high-speed airflow coaxial with the beam, thereby cutting the workpiece. . Nowadays, CO₂ pulse laser is generally used, and laser cutting is one of the thermal cutting methods.
(2)Water cutting processing
Water cutting, also known as water jet, is a high-pressure water jet cutting technology. It is a machine that uses high-pressure water flow to cut. Under computer control, workpieces can be carved arbitrarily and are less affected by the texture of the material. Water cutting is divided into two methods: sand-free cutting and sand-added cutting.
(3)Plasma cutting processing
Plasma arc cutting is a processing method that uses the heat of a high-temperature plasma arc to partially melt (and evaporate) the metal at the incision of the workpiece, and uses the momentum of high-speed plasma to remove the molten metal to form the incision.
(4)Wire cutting processing
Wire Electrical Discharge Machining (WEDM for short) belongs to the category of electrical machining. Wire cut Electrical Discharge Machining (WEDM for short) is sometimes also called wire cutting. Wire cutting can be divided into fast wire cutting, medium wire cutting, and slow wire cutting. The wire walking speed of fast wire EDM is 6 to 12 m/s, and the electrode wire moves back and forth at high speed, resulting in poor cutting accuracy. Medium wire EDM is a new technology developed in recent years that realizes frequency conversion multiple cutting functions on the basis of fast wire EDM. The wire walking speed of slow wire EDM is 0.2m/s, the electrode wire moves in one direction at low speed, and the cutting accuracy is very high.
(1)Laser cutting
Laser cutting machines have a wide range of applications. They can cut both metals and non-metals. CO₂ laser cutting machines can be used to cut non-metals, such as cloth and leather, and fiber laser cutting machines can be used to cut metals. The plate has little deformation.
(2)Water cutting
Water cutting is a cold cutting process with no thermal deformation and good cutting surface quality. It does not require secondary processing and can be easily processed if necessary. Water cutting can punch holes and cut any material, with fast cutting speed and flexible processing size.
(3)Plasma cutting
Plasma cutting can be used for cutting stainless steel, aluminum, copper, cast iron, carbon steel and other metal materials. Plasma cutting has obvious thermal effects, low precision, and the cutting surface is not easy to undergo secondary processing.
(4)Wire cutting
Wire cutting can only cut conductive materials, and cutting coolant is required during the cutting process, so materials that are not conductive, are afraid of water, and are afraid of being contaminated by cutting coolant, such as paper and leather, cannot be cut.
The industrial application of laser cutting carbon steel is generally below 20mm. The cutting capacity is generally less than 40mm. Stainless steel industrial applications are generally below 16mm, and cutting capabilities are generally below 25mm. Moreover, as the thickness of the workpiece increases, the cutting speed decreases significantly.
(2)Water cutting
The thickness of water cutting can be very thick, 0.8~100mm, or even thicker materials.
(3)Plasma cutting
Plasma cutting thickness is 0~120mm, and the best cutting quality range is around 20mm, which is the most cost-effective plasma system.
(4)Wire cutting
The thickness of wire cutting is generally 40~60mm, and the maximum thickness can be up to 600mm.
Using a 1200W laser to cut a 2mm thick mild steel plate, the cutting speed can reach 600cm/min; to cut a 5mm thick polypropylene resin plate, the cutting speed can reach 1200cm/min. The cutting efficiency that wire EDM can achieve is generally 20 to 60 square millimeters/minute, and can reach up to 300 square millimeters/minute. Obviously, laser cutting speed is fast and can be used for mass production.
(2)Water cutting
The speed of water cutting is quite slow and is not suitable for mass production.
(3)Plasma cutting
The cutting speed of plasma cutting is slow and the relative accuracy is low. It is more suitable for cutting thick plates, but the end face has a slope.
(4)Wire cutting
For metal processing, wire cutting has higher precision, but the speed is very slow. Sometimes it is necessary to use other methods to pierce and thread wires before cutting, and the cutting size is greatly limited.
The laser cutting incision is narrow, both sides of the slit are parallel and perpendicular to the surface, and the dimensional accuracy of the cut parts can reach ±0.2mm.
(2)Plasma cutting
Plasma can reach within 1mm.
(3)Water cutting
Water cutting does not produce thermal deformation, and the accuracy is ±0.1mm. If a dynamic waterjet machine is used, the cutting accuracy can be improved, and the cutting accuracy can reach ±0.02mm, eliminating the cutting slope.
(4)Wire cutting
The accuracy of wire cutting processing is generally ±0.01~±0.02mm, and the highest can be ±0.004mm.
(1)Laser cutting
Compared with plasma cutting, laser cutting is more precise and the slit is smaller, about 0.5mm.
(2)Plasma cutting
Plasma cutting slits are larger than laser cutting, about 1 to 2 mm.
(3)Water cutting
The slit of water cutting is about 10% larger than the diameter of the knife tube, generally 0.8~1.2mm. As the diameter of the sand cutter tube expands, the cut becomes larger.
(4)Wire cutting
The slit width of wire cutting is the smallest, generally around 0.1~0.2mm.
The surface roughness of laser cutting is not as good as water cutting, and the thicker the material, the more obvious it is.
(2)Water cutting
Water cutting will not change the texture of the material around the cutting seam (laser is a thermal cutting and will change the texture around the cutting area).
Laser cutting machines have different prices for different uses. Cheap ones such as carbon dioxide laser cutting machines only cost 20,000 to 30,000 yuan, while expensive ones such as 1000W fiber laser cutting machines now cost more than 1 million yuan. Laser cutting has no consumables, but the equipment investment cost is the highest among all cutting methods, and it is not a little higher, and the use and maintenance costs are also quite high.
(2)Plasma cutting
Plasma cutting machines are much cheaper than laser cutting machines. The prices vary depending on the power and brand of the plasma cutting machine, and the cost of use is high. Basically, it can cut conductive materials.
(3)Water cutting
The cost of water cutting equipment is second only to laser cutting. It consumes high energy and has high maintenance costs. The cutting speed is not as fast as that of plasma because all abrasives are disposable and are discharged into nature after one use. The environmental pollution caused is also serious.
(4)Wire cutting
Wire cutting generally costs around tens of thousands of yuan. But wire cutting has consumables, such as molybdenum wire, cutting coolant, etc. There are two types of wires commonly used for wire cutting. One is molybdenum wire (molybdenum is valuable), which is used in fast wire-traveling equipment. The advantage is that molybdenum wire can be reused many times; the other is copper wire (which is much cheaper than molybdenum wire anyway). ), used in slow wire moving equipment. The disadvantage is that the copper wire can only be used once. In addition, fast wire-moving machines are much cheaper than slow wire-moving machines. The price of one slow wire-moving machine is equal to 5 or 6 fast wire-moving machines.
During post-processing, the steel plate will be deformed after cutting due to warping, causing the workpiece to be scrapped, affecting the normal use of the user, and causing economic losses to the company. Analysis shows that there are residual stresses in the interior and upper and lower surfaces of the steel plate after hot rolling. If the residual stress is unevenly distributed along the width and length of the steel plate, a moment will be generated on the section of the steel plate, causing the steel plate to warp after slitting. The control measures are:
(1)TMCP technology
The new TMCP technology refers to rolling under continuous high pressure at a final rolling temperature of ≥950°C, followed by ultra-rapid cooling at a cooling rate of 300 to 400°C/s.
The continuous large deformation strain accumulation in the steel plate using the new TMCP technology hardens the austenite, followed by ultra-rapid cooling. On the one hand, the hardened austenite remains unchanged, that is, the hardened austenite is "frozen". Ultra-rapid cooling also facilitates 20 nm
A large number of fine particles are precipitated below, and as the ultra-rapid cooling temperature continues to decrease, the particle distribution becomes more dispersed.
Due to the ultra-rapid cooling, the nucleation rate is increased and the ferrite grains are refined. Maintain the ultra-fast cooling state until the cooling is stopped near the phase transition point, and then control the cooling path to obtain a steel plate with excellent properties. At the same time, during continuous rolling at normal temperatures, the high temperature allows accumulated dislocations to slip and precipitate, and the high-energy state stress is released.
(2) Cooling temperature
The internal stress imbalance problem caused by laminar cooling is mainly caused by three types of uneven cooling:
① The lateral cooling is seriously uneven;
②Asymmetric cooling in the thickness direction;
③ Uneven cooling and mixing in the transverse and thickness directions.
Controlling the lateral uniformity of cooling and the symmetry in the thickness direction are necessary conditions for controlling the flatness of medium and thick plates and reducing internal stress. The lateral cooling side injection solution achieves uniformity of laminar cooling temperature control by improving the lateral angle of the lower header and the water stagnant point.
(3) Cold straightening
Straightening can improve the residual stress distribution of the steel plate. When the steel plate has uneven stress distribution on the cross-section, roll bending measures may be needed to increase local deformation to compensate for the uneven length of the longitudinal fibers to eliminate wave bending and uniformity. The purpose of internal stress in steel plate.
Adjusting the lateral crown value of the straightening machine is also an important measure to improve the residual stress distribution of the steel plate.
In summary, by using the new TMCP process to improve the uniformity of laminar cooling rate control temperature, and cold straightening the steel plate, the internal stress of the steel plate is promoted to be uniform, and the deformation problem is controlled when the steel plate is then longitudinally cut into strips.
There are many types of steel plates on the market now. For example, according to its thickness, there are thin plates, medium plates, thick plates, and extra-thick plates; according to raw materials, it can be divided into carbon steel plate and stainless steel plate,etc. according to the production method, there are hot-rolled steel plates and cold-rolled steel plates; according to surface characteristics: galvanized plates, tin plate, composite steel plate, color-coated steel plate; classified by use, there are bridge steel plates, boiler steel plates, shipbuilding steel plates, spring steel plates, etc. Since there are so many types of steel plates, the cutting methods of steel plates must naturally keep up.
The choice of steel plate cutting method depends on the situation. In addition to laser cutting, there are also water cutting, plasma cutting, wire cutting and other methods. In what scenarios are they used? Detailed answer below.
An engineer engaged in the cutting field said this:
(1) Nowadays, the mainstream fiber lasers in the market, carbon dioxide lasers are slowly being phased out because they consume too much energy. However, there is still a market in the non-metallic field.
(2) Nowadays, since the domestic production of lasers, the price of optical fiber equipment in the medium and low power range has dropped sharply.
(3) For cutting methods other than laser, the market demand for plasma and wire cutting is relatively large, but wire cutting targets many mold industries. Plasma has more demand when it comes to thick plates or low precision requirements, and water jet cutting has more demand. Nowadays it is not common in the metal industry and there are many in the non-metal industry.
(4) In the future development, laser cutting will definitely dominate the metal sheet, and non-metal cutting will also occupy a large part of the market.
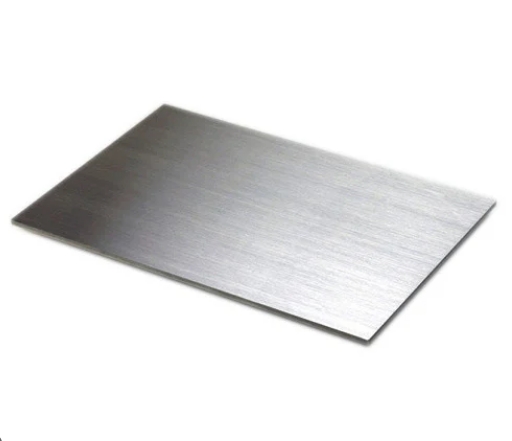
1. 4 types of steel plate cutting technologies
(1)Laser cutting processingLaser cutting uses a focused high-power density laser beam to irradiate the workpiece, causing the irradiated material to quickly melt, vaporize, ablate or reach the ignition point. At the same time, the molten material is blown away by a high-speed airflow coaxial with the beam, thereby cutting the workpiece. . Nowadays, CO₂ pulse laser is generally used, and laser cutting is one of the thermal cutting methods.
(2)Water cutting processing
Water cutting, also known as water jet, is a high-pressure water jet cutting technology. It is a machine that uses high-pressure water flow to cut. Under computer control, workpieces can be carved arbitrarily and are less affected by the texture of the material. Water cutting is divided into two methods: sand-free cutting and sand-added cutting.
(3)Plasma cutting processing
Plasma arc cutting is a processing method that uses the heat of a high-temperature plasma arc to partially melt (and evaporate) the metal at the incision of the workpiece, and uses the momentum of high-speed plasma to remove the molten metal to form the incision.
(4)Wire cutting processing
Wire Electrical Discharge Machining (WEDM for short) belongs to the category of electrical machining. Wire cut Electrical Discharge Machining (WEDM for short) is sometimes also called wire cutting. Wire cutting can be divided into fast wire cutting, medium wire cutting, and slow wire cutting. The wire walking speed of fast wire EDM is 6 to 12 m/s, and the electrode wire moves back and forth at high speed, resulting in poor cutting accuracy. Medium wire EDM is a new technology developed in recent years that realizes frequency conversion multiple cutting functions on the basis of fast wire EDM. The wire walking speed of slow wire EDM is 0.2m/s, the electrode wire moves in one direction at low speed, and the cutting accuracy is very high.
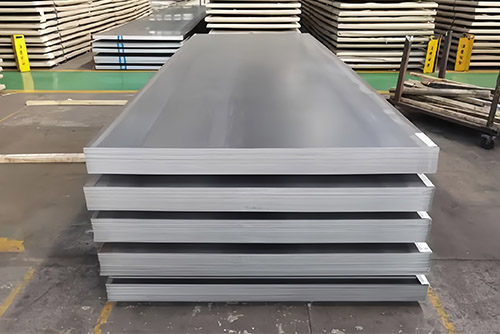
2. Comparison of application scope
(1)Laser cuttingLaser cutting machines have a wide range of applications. They can cut both metals and non-metals. CO₂ laser cutting machines can be used to cut non-metals, such as cloth and leather, and fiber laser cutting machines can be used to cut metals. The plate has little deformation.
(2)Water cutting
Water cutting is a cold cutting process with no thermal deformation and good cutting surface quality. It does not require secondary processing and can be easily processed if necessary. Water cutting can punch holes and cut any material, with fast cutting speed and flexible processing size.
(3)Plasma cutting
Plasma cutting can be used for cutting stainless steel, aluminum, copper, cast iron, carbon steel and other metal materials. Plasma cutting has obvious thermal effects, low precision, and the cutting surface is not easy to undergo secondary processing.
(4)Wire cutting
Wire cutting can only cut conductive materials, and cutting coolant is required during the cutting process, so materials that are not conductive, are afraid of water, and are afraid of being contaminated by cutting coolant, such as paper and leather, cannot be cut.
3. Cutting thickness comparison
(1)Laser cuttingThe industrial application of laser cutting carbon steel is generally below 20mm. The cutting capacity is generally less than 40mm. Stainless steel industrial applications are generally below 16mm, and cutting capabilities are generally below 25mm. Moreover, as the thickness of the workpiece increases, the cutting speed decreases significantly.
(2)Water cutting
The thickness of water cutting can be very thick, 0.8~100mm, or even thicker materials.
(3)Plasma cutting
Plasma cutting thickness is 0~120mm, and the best cutting quality range is around 20mm, which is the most cost-effective plasma system.
(4)Wire cutting
The thickness of wire cutting is generally 40~60mm, and the maximum thickness can be up to 600mm.
4. Cutting speed comparison
(1)Laser cuttingUsing a 1200W laser to cut a 2mm thick mild steel plate, the cutting speed can reach 600cm/min; to cut a 5mm thick polypropylene resin plate, the cutting speed can reach 1200cm/min. The cutting efficiency that wire EDM can achieve is generally 20 to 60 square millimeters/minute, and can reach up to 300 square millimeters/minute. Obviously, laser cutting speed is fast and can be used for mass production.
(2)Water cutting
The speed of water cutting is quite slow and is not suitable for mass production.
(3)Plasma cutting
The cutting speed of plasma cutting is slow and the relative accuracy is low. It is more suitable for cutting thick plates, but the end face has a slope.
(4)Wire cutting
For metal processing, wire cutting has higher precision, but the speed is very slow. Sometimes it is necessary to use other methods to pierce and thread wires before cutting, and the cutting size is greatly limited.
5. Comparison of cutting accuracy
(1)Laser cuttingThe laser cutting incision is narrow, both sides of the slit are parallel and perpendicular to the surface, and the dimensional accuracy of the cut parts can reach ±0.2mm.
(2)Plasma cutting
Plasma can reach within 1mm.
(3)Water cutting
Water cutting does not produce thermal deformation, and the accuracy is ±0.1mm. If a dynamic waterjet machine is used, the cutting accuracy can be improved, and the cutting accuracy can reach ±0.02mm, eliminating the cutting slope.
(4)Wire cutting
The accuracy of wire cutting processing is generally ±0.01~±0.02mm, and the highest can be ±0.004mm.
6. Comparison of slit width
(1)Laser cuttingCompared with plasma cutting, laser cutting is more precise and the slit is smaller, about 0.5mm.
(2)Plasma cutting
Plasma cutting slits are larger than laser cutting, about 1 to 2 mm.
(3)Water cutting
The slit of water cutting is about 10% larger than the diameter of the knife tube, generally 0.8~1.2mm. As the diameter of the sand cutter tube expands, the cut becomes larger.
(4)Wire cutting
The slit width of wire cutting is the smallest, generally around 0.1~0.2mm.
7. Comparison of cutting surface quality
(1)Laser cuttingThe surface roughness of laser cutting is not as good as water cutting, and the thicker the material, the more obvious it is.
(2)Water cutting
Water cutting will not change the texture of the material around the cutting seam (laser is a thermal cutting and will change the texture around the cutting area).
8. Production input cost comparison
(1)Laser cuttingLaser cutting machines have different prices for different uses. Cheap ones such as carbon dioxide laser cutting machines only cost 20,000 to 30,000 yuan, while expensive ones such as 1000W fiber laser cutting machines now cost more than 1 million yuan. Laser cutting has no consumables, but the equipment investment cost is the highest among all cutting methods, and it is not a little higher, and the use and maintenance costs are also quite high.
(2)Plasma cutting
Plasma cutting machines are much cheaper than laser cutting machines. The prices vary depending on the power and brand of the plasma cutting machine, and the cost of use is high. Basically, it can cut conductive materials.
(3)Water cutting
The cost of water cutting equipment is second only to laser cutting. It consumes high energy and has high maintenance costs. The cutting speed is not as fast as that of plasma because all abrasives are disposable and are discharged into nature after one use. The environmental pollution caused is also serious.
(4)Wire cutting
Wire cutting generally costs around tens of thousands of yuan. But wire cutting has consumables, such as molybdenum wire, cutting coolant, etc. There are two types of wires commonly used for wire cutting. One is molybdenum wire (molybdenum is valuable), which is used in fast wire-traveling equipment. The advantage is that molybdenum wire can be reused many times; the other is copper wire (which is much cheaper than molybdenum wire anyway). ), used in slow wire moving equipment. The disadvantage is that the copper wire can only be used once. In addition, fast wire-moving machines are much cheaper than slow wire-moving machines. The price of one slow wire-moving machine is equal to 5 or 6 fast wire-moving machines.
9. Control measures for steel plate cutting deformation
During post-processing, the steel plate will be deformed after cutting due to warping, causing the workpiece to be scrapped, affecting the normal use of the user, and causing economic losses to the company. Analysis shows that there are residual stresses in the interior and upper and lower surfaces of the steel plate after hot rolling. If the residual stress is unevenly distributed along the width and length of the steel plate, a moment will be generated on the section of the steel plate, causing the steel plate to warp after slitting. The control measures are:(1)TMCP technology
The new TMCP technology refers to rolling under continuous high pressure at a final rolling temperature of ≥950°C, followed by ultra-rapid cooling at a cooling rate of 300 to 400°C/s.
The continuous large deformation strain accumulation in the steel plate using the new TMCP technology hardens the austenite, followed by ultra-rapid cooling. On the one hand, the hardened austenite remains unchanged, that is, the hardened austenite is "frozen". Ultra-rapid cooling also facilitates 20 nm
A large number of fine particles are precipitated below, and as the ultra-rapid cooling temperature continues to decrease, the particle distribution becomes more dispersed.
Due to the ultra-rapid cooling, the nucleation rate is increased and the ferrite grains are refined. Maintain the ultra-fast cooling state until the cooling is stopped near the phase transition point, and then control the cooling path to obtain a steel plate with excellent properties. At the same time, during continuous rolling at normal temperatures, the high temperature allows accumulated dislocations to slip and precipitate, and the high-energy state stress is released.
(2) Cooling temperature
The internal stress imbalance problem caused by laminar cooling is mainly caused by three types of uneven cooling:
① The lateral cooling is seriously uneven;
②Asymmetric cooling in the thickness direction;
③ Uneven cooling and mixing in the transverse and thickness directions.
Controlling the lateral uniformity of cooling and the symmetry in the thickness direction are necessary conditions for controlling the flatness of medium and thick plates and reducing internal stress. The lateral cooling side injection solution achieves uniformity of laminar cooling temperature control by improving the lateral angle of the lower header and the water stagnant point.
(3) Cold straightening
Straightening can improve the residual stress distribution of the steel plate. When the steel plate has uneven stress distribution on the cross-section, roll bending measures may be needed to increase local deformation to compensate for the uneven length of the longitudinal fibers to eliminate wave bending and uniformity. The purpose of internal stress in steel plate.
Adjusting the lateral crown value of the straightening machine is also an important measure to improve the residual stress distribution of the steel plate.
In summary, by using the new TMCP process to improve the uniformity of laminar cooling rate control temperature, and cold straightening the steel plate, the internal stress of the steel plate is promoted to be uniform, and the deformation problem is controlled when the steel plate is then longitudinally cut into strips.