Galvanized steel plate refers to a steel sheet with a layer of zinc on the surface. Galvanizing is an economical and effective anti-corrosion method that is often used. About half of the world's zinc production is used in this process. Common products include galvanized seamless pipes and galvanized welded pipes.Galvanized steel panels are coated with a layer of metallic zinc to prevent corrosion and extend their service life. These zinc-coated panels are known as galvanized panels.
Galvanized sheets can be used as substrates, and their processed products are often used in various industries, covering a wide range of fields. In the import and export trade of steel products, the export proportion of galvanized sheets is higher than that of other products, and its overall profitability is also higher than that of hot-rolled/cold-rolled coils. In this regard, we need to have an in-depth understanding of galvanized sheets to lay the foundation for disseminating relevant knowledge to customers, negotiating with customers, and formulating preferential plans in the future.
The two common categories of galvanized sheets are electro-galvanized sheets and hot-dip galvanized sheets, and these two are also easy to confuse people.
(1) Electro-galvanized steel plate. Also known as cold galvanizing, it uses an electrochemical method, using a zinc ingot as an anode. Zinc atoms lose their electrons and become ions and dissolve into the electrolyte. The steel strip serves as a cathode. Zinc ions gain electrons on the steel strip and are reduced to zinc. Atoms are deposited onto the surface of the steel strip to form a coating.
(2) Hot-dip galvanized steel plate. A thin steel plate is immersed in a bath of molten zinc so that a layer of zinc adheres to its surface. At present, the continuous galvanizing process is mainly used for production, that is, the rolled steel plates are continuously immersed in a plating bath containing molten zinc to make galvanized steel plates.
(1) Concept
Hot-dip galvanizing: also called hot-dip galvanizing and hot-dip galvanizing: it is an effective method of metal anti-corrosion. It melts zinc ingots at high temperatures, then puts in some auxiliary materials, and then immerses the metal structural parts in a galvanizing bath. In it, a layer of zinc is attached to the metal components for the purpose of anti-corrosion. The advantage of hot-dip galvanizing is that it has strong anti-corrosion ability and the galvanized layer has good adhesion and hardness, thus achieving the purpose of anti-corrosion.
Electrogalvanizing: It is cold galvanizing. The amount of zinc applied is small, only 10-50g/m2. It is a process that uses electrolysis to attach a metal film to the surface of metal or other material parts. The process of forming a uniform, dense, and well-bonded metal layer can prevent corrosion, improve wear resistance, conductivity, reflectivity, and enhance aesthetics.
(2) Differences in reaction methods
Hot-dip galvanizing is a chemical treatment and is an electrochemical reaction. Hot-dip galvanizing makes the molten metal react with the iron matrix to produce an alloy layer, thereby combining the matrix and the coating.
Electro-galvanizing is a physical treatment, just brushing a layer of zinc on the surface, so the zinc layer is easy to fall off.
(3) Process differences
Hot-dip galvanizing involves degreasing, pickling, dipping and drying the workpiece, then immersing it in the molten zinc solution for a certain period of time and then lifting it out.
Electro-galvanizing uses electrolysis equipment to degrease and pickle the workpiece and put it into a solution composed of zinc salts, and connect it to the negative electrode of the electrolysis equipment; place a zinc plate opposite the workpiece and connect it to the positive electrode of the electrolysis equipment, and turn on the power. Using the directional movement of current from the positive electrode to the negative electrode, a layer of zinc will be deposited on the workpiece.
(4) Differences in galvanized finished products
The surface of hot-dip galvanizing is not as delicate and bright as electro-galvanizing, and the coating is uniform. However, the thickness of the zinc layer is dozens of times that of electro-galvanizing. The anti-corrosion performance is also dozens of times that of electroplated zinc.
Electro-galvanized, the surface of the workpiece is smooth and flat, but because the coating is relatively thin, electro-galvanized is generally within 5-30 microns, so the anti-corrosion time will be relatively short.
In suburban environments, the standard hot-dip galvanized rust-proof thickness can be maintained for more than 50 years without repair; in urban or offshore areas, the standard hot-dip galvanized rust-proof layer can be maintained for 20 years without repair;
(5) Differences in use
Hot-dip galvanizing: suitable for long-term rust prevention of steel parts for outdoor work, such as highway fences, power towers, large-size fasteners and other relatively "rough" workpieces. Earlier iron water pipes were also hot-dip galvanized.
Electro-galvanizing: It is used to prevent rust of indoor parts, such as the bottom of the casing, panels, small-size fasteners, etc.
(6) Price difference
Electro-galvanizing can only be plated on one side, while hot-dip galvanizing must be fully plated. And hot-dip galvanizing generally has a thicker galvanized layer than cold-dip galvanizing, so the price of hot-dip galvanizing is higher than that of electro-galvanizing.
(7) Environmental issues
Hot-dip galvanized square and rectangular pipes emit less pollutants, mainly waste acid from pickling workpieces.
The pollutants in electroplating mainly include waste acid from pickling workpieces, waste electroplating liquid, waste passivation liquid, etc. The types and quantities of emissions are much greater than those of hot-dip galvanizing.
A large number of galvanized sheets are used in automobile manufacturing, refrigerated containers, the construction industry, ventilation and heating installations and furniture manufacturing. (Galvanizing has become an important anti-corrosion method for steel, not only because zinc can form a dense protective layer on the surface of steel, but also because zinc has a cathodic protection effect. When the galvanized layer is damaged, it can still prevent iron from corrosion through cathodic protection. Corrosion of base material.)
(1)Construction industry
Roofs, roof elements, balcony panels, window sills, kiosks, warehouses, roller shutters, heaters, rainwater pipes, etc.
(2)Household appliances
Refrigerators, washing machines, switch cabinets, air conditioners, microwave ovens, toasters, photocopiers, vending machines, electric fans, vacuum cleaners, etc. Furniture industry: lampshades, wardrobes, tables, bookshelves, counters, signs, health equipment, etc.
(3)Transportation industry
Car ceilings, car shells, carriage panels, tractors, trams, containers, highway walls, ship bulkheads, etc.
Galvanized sheets can be used as substrates, and their processed products are often used in various industries, covering a wide range of fields. In the import and export trade of steel products, the export proportion of galvanized sheets is higher than that of other products, and its overall profitability is also higher than that of hot-rolled/cold-rolled coils. In this regard, we need to have an in-depth understanding of galvanized sheets to lay the foundation for disseminating relevant knowledge to customers, negotiating with customers, and formulating preferential plans in the future.
1. What is electro-galvanized sheet and hot-dip galvanized sheet?
The two common categories of galvanized sheets are electro-galvanized sheets and hot-dip galvanized sheets, and these two are also easy to confuse people.(1) Electro-galvanized steel plate. Also known as cold galvanizing, it uses an electrochemical method, using a zinc ingot as an anode. Zinc atoms lose their electrons and become ions and dissolve into the electrolyte. The steel strip serves as a cathode. Zinc ions gain electrons on the steel strip and are reduced to zinc. Atoms are deposited onto the surface of the steel strip to form a coating.
(2) Hot-dip galvanized steel plate. A thin steel plate is immersed in a bath of molten zinc so that a layer of zinc adheres to its surface. At present, the continuous galvanizing process is mainly used for production, that is, the rolled steel plates are continuously immersed in a plating bath containing molten zinc to make galvanized steel plates.
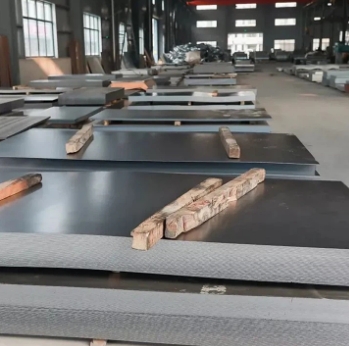
2. Electro galvanized vs hot dip galvanized steel plate
(1) ConceptHot-dip galvanizing: also called hot-dip galvanizing and hot-dip galvanizing: it is an effective method of metal anti-corrosion. It melts zinc ingots at high temperatures, then puts in some auxiliary materials, and then immerses the metal structural parts in a galvanizing bath. In it, a layer of zinc is attached to the metal components for the purpose of anti-corrosion. The advantage of hot-dip galvanizing is that it has strong anti-corrosion ability and the galvanized layer has good adhesion and hardness, thus achieving the purpose of anti-corrosion.
Electrogalvanizing: It is cold galvanizing. The amount of zinc applied is small, only 10-50g/m2. It is a process that uses electrolysis to attach a metal film to the surface of metal or other material parts. The process of forming a uniform, dense, and well-bonded metal layer can prevent corrosion, improve wear resistance, conductivity, reflectivity, and enhance aesthetics.
(2) Differences in reaction methods
Hot-dip galvanizing is a chemical treatment and is an electrochemical reaction. Hot-dip galvanizing makes the molten metal react with the iron matrix to produce an alloy layer, thereby combining the matrix and the coating.
Electro-galvanizing is a physical treatment, just brushing a layer of zinc on the surface, so the zinc layer is easy to fall off.
(3) Process differences
Hot-dip galvanizing involves degreasing, pickling, dipping and drying the workpiece, then immersing it in the molten zinc solution for a certain period of time and then lifting it out.
Electro-galvanizing uses electrolysis equipment to degrease and pickle the workpiece and put it into a solution composed of zinc salts, and connect it to the negative electrode of the electrolysis equipment; place a zinc plate opposite the workpiece and connect it to the positive electrode of the electrolysis equipment, and turn on the power. Using the directional movement of current from the positive electrode to the negative electrode, a layer of zinc will be deposited on the workpiece.
(4) Differences in galvanized finished products
The surface of hot-dip galvanizing is not as delicate and bright as electro-galvanizing, and the coating is uniform. However, the thickness of the zinc layer is dozens of times that of electro-galvanizing. The anti-corrosion performance is also dozens of times that of electroplated zinc.
Electro-galvanized, the surface of the workpiece is smooth and flat, but because the coating is relatively thin, electro-galvanized is generally within 5-30 microns, so the anti-corrosion time will be relatively short.
In suburban environments, the standard hot-dip galvanized rust-proof thickness can be maintained for more than 50 years without repair; in urban or offshore areas, the standard hot-dip galvanized rust-proof layer can be maintained for 20 years without repair;
(5) Differences in use
Hot-dip galvanizing: suitable for long-term rust prevention of steel parts for outdoor work, such as highway fences, power towers, large-size fasteners and other relatively "rough" workpieces. Earlier iron water pipes were also hot-dip galvanized.
Electro-galvanizing: It is used to prevent rust of indoor parts, such as the bottom of the casing, panels, small-size fasteners, etc.
(6) Price difference
Electro-galvanizing can only be plated on one side, while hot-dip galvanizing must be fully plated. And hot-dip galvanizing generally has a thicker galvanized layer than cold-dip galvanizing, so the price of hot-dip galvanizing is higher than that of electro-galvanizing.
(7) Environmental issues
Hot-dip galvanized square and rectangular pipes emit less pollutants, mainly waste acid from pickling workpieces.
The pollutants in electroplating mainly include waste acid from pickling workpieces, waste electroplating liquid, waste passivation liquid, etc. The types and quantities of emissions are much greater than those of hot-dip galvanizing.
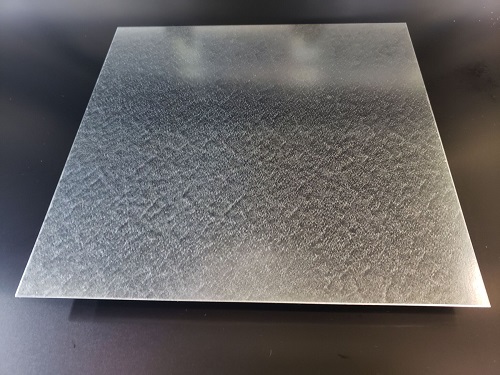
3. Main application industries of galvanized sheets
A large number of galvanized sheets are used in automobile manufacturing, refrigerated containers, the construction industry, ventilation and heating installations and furniture manufacturing. (Galvanizing has become an important anti-corrosion method for steel, not only because zinc can form a dense protective layer on the surface of steel, but also because zinc has a cathodic protection effect. When the galvanized layer is damaged, it can still prevent iron from corrosion through cathodic protection. Corrosion of base material.)(1)Construction industry
Roofs, roof elements, balcony panels, window sills, kiosks, warehouses, roller shutters, heaters, rainwater pipes, etc.
(2)Household appliances
Refrigerators, washing machines, switch cabinets, air conditioners, microwave ovens, toasters, photocopiers, vending machines, electric fans, vacuum cleaners, etc. Furniture industry: lampshades, wardrobes, tables, bookshelves, counters, signs, health equipment, etc.
(3)Transportation industry
Car ceilings, car shells, carriage panels, tractors, trams, containers, highway walls, ship bulkheads, etc.