In the production of cs seamless pipes, lubricants are lubricating media used to reduce the frictional resistance of friction and slow down their wear; lubricants also play the role of cooling, cleaning and preventing contamination of friction. However, the use of lubricants may cause corrosion spots, brown and white contamination spots on the surface of the cs seamless pipe, which not only reduces the appearance quality of the product, but also increases the difficulty of subsequent processing, and even affects the performance of the product.
In order to improve product quality and eliminate spots, surface degreasing and cleaning processes are required. The components and properties of lubricants are very important for surface degreasing and cleaning. The pollution spots formed on the surface of seamless steel pipes can be divided into 3 categories according to the substances causing pollution:
1.Oily pollution - oil, grease and fatty acids;
2.Water-soluble pollution - organic and inorganic acids;
3.Solid pollution - oxides, particles and dust, etc.
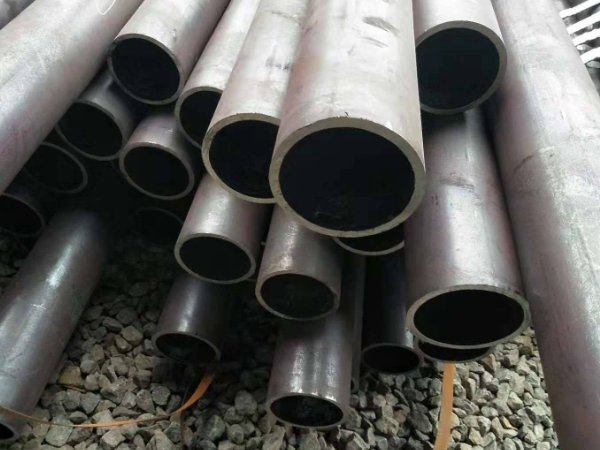
Surface degreasing method of seamless pipe:
1.The formula of the degreasing solution is: each liter of solution contains 20g-30g of sodium hydroxide, 35g-50g of sodium nitrate, and 3g-5g of sodium silicate.
2.The operating process requirements are: the liquid temperature is 70 ℃ ~ 80 ℃, and the soaking time is determined by the test method according to the amount of oil on the surface of the pipe, generally about 10 minutes to 40 minutes. The heating method can be steam.
3.Seamless pipes can be inspected by any of the following methods
①Wipe the surface of the seamless tube with clean and dry white filter paper, if there is no trace of grease on the paper, it is qualified;
②Use 100% camphor below 1mm to check the steam to flush the condensate, and it is qualified to keep rotating;
③ Check the surface of the seamless tube with ultraviolet rays with a wavelength of 3200-3800 angstroms, and the grease-free fluorescence is qualified. After degreasing treatment, the oil pollution on the pipe surface can be removed.
Requirements and inspection of degreasing seamless pipes
1. The prefabricated length of the pipeline should not exceed 20 meters (if it is too long, the steam will form condensed water prematurely, which will affect the degreasing effect, but the pipe below DN200 can be appropriately lengthened)
① Pipe prefabrication should not have U-shaped bends (if there are U-shaped bends, condensed water will accumulate to block the pipeline and it will not be easy to remove, which will affect the degreasing effect, but if there is a discharge port at the lowest point, the degreasing will not be affected)
②Because the passivation (generally nitrogen filling) of the pipeline after degreasing is more difficult, the fixed welding joint can be reserved according to the above two requirements during installation, so as to be uniformly degreasing before purging
③The medium pressure oil-free rubber pipeline can be used to connect the steam source to degreasing the pipeline.
2. Use an oil-free clean vessel to take a certain amount of vapor condensate from the degreasing pipeline. When the temperature of the condensate drops below 40 degrees, put a small grain (less than 1mm in diameter) of pure camphor, and the camphor grains are qualified by rotating continuously.
Equipment, pipes, fittings and valves shall be inspected and identified after being degreased. The inspection standard shall be carried out according to the following provisions according to the different functions of the degreased parts in production and the degree of danger or harm caused by contamination with grease
1. Equipment, pipes, fittings, valves, etc. that directly or may be in contact with strong oxidizing media such as oxygen, oxygen-rich, concentrated nitric acid, etc., can be inspected by any of the following methods:
① Check the surface of the degreased parts with ultraviolet light with a wavelength of 3200-3800 angstroms, and the grease-free fluorescence is qualified;
② Wipe the surface of the degreasing part with clean and dry white filter paper, if there is no trace of grease on the paper, it is qualified;
③Blow the degreasing part with oil-free steam, take its condensate, put in a small grain (less than 1 mm in diameter) of pure camphor, and it is qualified if the camphor material keeps rotating;
④ For the degreased parts that cannot be inspected by the above method, the solvent oil content after degreasing shall not exceed 350 mg/L to be qualified.
2. The equipment and pipelines cleaned with concentrated nitric acid should be analyzed for the total amount of organic matter contained in the acid, and it is qualified if it does not exceed 0.03%.
3. For the degreased parts degreased with solvent, the residual solvent must be completely blown away until there is no solvent smell. Those degreased with lye must be rinsed with oil-free water until neutral, and then dried. Those who are blown off with steam should dry the degreased parts in time. The oil-free water used for rinsing austenitic stainless steel should not contain more than 25ppm of chloride ions.
4. If the design has specified inspection standards, it should be inspected according to the standards specified in the design.
In order to improve product quality and eliminate spots, surface degreasing and cleaning processes are required. The components and properties of lubricants are very important for surface degreasing and cleaning. The pollution spots formed on the surface of seamless steel pipes can be divided into 3 categories according to the substances causing pollution:
1.Oily pollution - oil, grease and fatty acids;
2.Water-soluble pollution - organic and inorganic acids;
3.Solid pollution - oxides, particles and dust, etc.
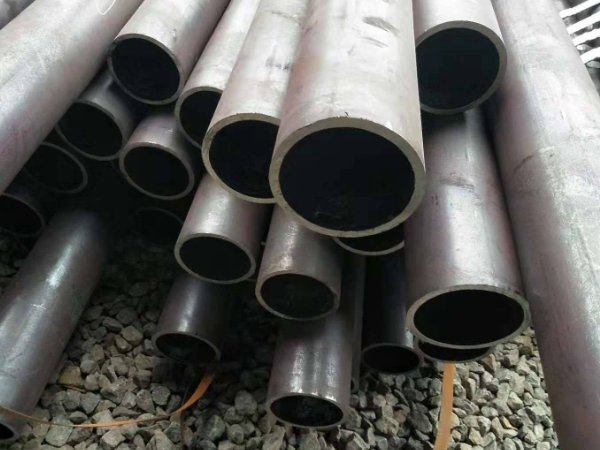
Surface degreasing method of seamless pipe:
1.The formula of the degreasing solution is: each liter of solution contains 20g-30g of sodium hydroxide, 35g-50g of sodium nitrate, and 3g-5g of sodium silicate.
2.The operating process requirements are: the liquid temperature is 70 ℃ ~ 80 ℃, and the soaking time is determined by the test method according to the amount of oil on the surface of the pipe, generally about 10 minutes to 40 minutes. The heating method can be steam.
3.Seamless pipes can be inspected by any of the following methods
①Wipe the surface of the seamless tube with clean and dry white filter paper, if there is no trace of grease on the paper, it is qualified;
②Use 100% camphor below 1mm to check the steam to flush the condensate, and it is qualified to keep rotating;
③ Check the surface of the seamless tube with ultraviolet rays with a wavelength of 3200-3800 angstroms, and the grease-free fluorescence is qualified. After degreasing treatment, the oil pollution on the pipe surface can be removed.
Requirements and inspection of degreasing seamless pipes
1. The prefabricated length of the pipeline should not exceed 20 meters (if it is too long, the steam will form condensed water prematurely, which will affect the degreasing effect, but the pipe below DN200 can be appropriately lengthened)
① Pipe prefabrication should not have U-shaped bends (if there are U-shaped bends, condensed water will accumulate to block the pipeline and it will not be easy to remove, which will affect the degreasing effect, but if there is a discharge port at the lowest point, the degreasing will not be affected)
②Because the passivation (generally nitrogen filling) of the pipeline after degreasing is more difficult, the fixed welding joint can be reserved according to the above two requirements during installation, so as to be uniformly degreasing before purging
③The medium pressure oil-free rubber pipeline can be used to connect the steam source to degreasing the pipeline.
2. Use an oil-free clean vessel to take a certain amount of vapor condensate from the degreasing pipeline. When the temperature of the condensate drops below 40 degrees, put a small grain (less than 1mm in diameter) of pure camphor, and the camphor grains are qualified by rotating continuously.
Equipment, pipes, fittings and valves shall be inspected and identified after being degreased. The inspection standard shall be carried out according to the following provisions according to the different functions of the degreased parts in production and the degree of danger or harm caused by contamination with grease
1. Equipment, pipes, fittings, valves, etc. that directly or may be in contact with strong oxidizing media such as oxygen, oxygen-rich, concentrated nitric acid, etc., can be inspected by any of the following methods:
① Check the surface of the degreased parts with ultraviolet light with a wavelength of 3200-3800 angstroms, and the grease-free fluorescence is qualified;
② Wipe the surface of the degreasing part with clean and dry white filter paper, if there is no trace of grease on the paper, it is qualified;
③Blow the degreasing part with oil-free steam, take its condensate, put in a small grain (less than 1 mm in diameter) of pure camphor, and it is qualified if the camphor material keeps rotating;
④ For the degreased parts that cannot be inspected by the above method, the solvent oil content after degreasing shall not exceed 350 mg/L to be qualified.
2. The equipment and pipelines cleaned with concentrated nitric acid should be analyzed for the total amount of organic matter contained in the acid, and it is qualified if it does not exceed 0.03%.
3. For the degreased parts degreased with solvent, the residual solvent must be completely blown away until there is no solvent smell. Those degreased with lye must be rinsed with oil-free water until neutral, and then dried. Those who are blown off with steam should dry the degreased parts in time. The oil-free water used for rinsing austenitic stainless steel should not contain more than 25ppm of chloride ions.
4. If the design has specified inspection standards, it should be inspected according to the standards specified in the design.