What is a water well casing?
Water well casing is a device used to control the collapse of the side walls of water wells and ensure wellhead work safety. It consists of two parts: the casing body and the casing accessories. The water well casing system consists of casing, cement for burying the casing, an interlayer for fixing the casing, and casing connectors.
What is well casing made of?
Common materials for deepwater well casing include carbon steel, stainless steel and titanium alloy.
1. Carbon steel casing
Carbon steel casing(such as oil casing) is the most common casing material, mainly composed of carbon and a combination of other different elements. Because of its low price, high strength and easy processing, it is widely used in many low-stage oil wells. However, carbon steel casing is prone to corrosion and wear in harsh environments such as high temperature, high pressure and corrosion, so its use in deepwater wells is limited.
2. Stainless steel casing
Stainless steel casing is made of an alloy of elements such as chromium and nickel, which has good corrosion resistance and high wear resistance. Stainless steel casing is more corrosion-resistant than carbon steel casing in deepwater well environments, and its strength and pressure resistance are relatively high, but the price is higher.
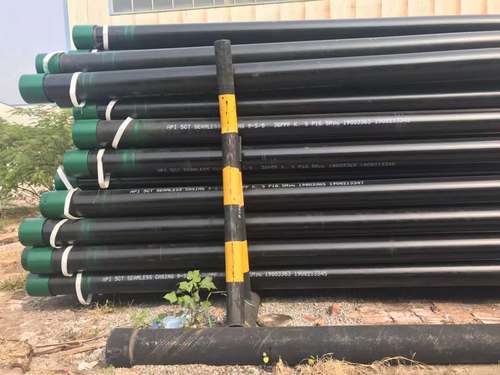
3.Titanium alloy casing
Titanium alloy refers to a variety of alloy metals made of titanium and other metals, which are widely used in deepwater wells. However, titanium alloy casings are expensive and are only suitable for areas with special requirements, such as ultra-deep wells.
Precautions for running water well casing
Casing running is a very important step in drilling. It can ensure the stability of the well wall and prevent the well wall from collapsing.
The following points need to be noted during the casing installation process.
1. First, the size and depth of the casing need to be determined, and the selection is based on factors such as well depth, formation conditions, and drilling purposes.
2. After determining the size and depth of the casing, the wellbore needs to be cleaned to ensure that the inside of the wellbore is clean to avoid obstruction when the casing sinks.
3. Next, casing needs to be run in. This process requires the use of a casing runner to run the casing into the wellbore section by section. During the running process, attention needs to be paid to controlling the speed of running the casing to avoid deformation or jamming of the casing caused by being too fast or too slow.
4. After the casing is lowered to the predetermined depth, cementing operation is required. Cement slurry is injected into the gap between the casing and the well wall to fix it in the well wall.
5. Finally, the casing needs to be sealed and inspected to ensure the quality and integrity of the casing and avoid water leakage problems.
Water well casing is a device used to control the collapse of the side walls of water wells and ensure wellhead work safety. It consists of two parts: the casing body and the casing accessories. The water well casing system consists of casing, cement for burying the casing, an interlayer for fixing the casing, and casing connectors.
What is well casing made of?
Common materials for deepwater well casing include carbon steel, stainless steel and titanium alloy.
1. Carbon steel casing
Carbon steel casing(such as oil casing) is the most common casing material, mainly composed of carbon and a combination of other different elements. Because of its low price, high strength and easy processing, it is widely used in many low-stage oil wells. However, carbon steel casing is prone to corrosion and wear in harsh environments such as high temperature, high pressure and corrosion, so its use in deepwater wells is limited.
2. Stainless steel casing
Stainless steel casing is made of an alloy of elements such as chromium and nickel, which has good corrosion resistance and high wear resistance. Stainless steel casing is more corrosion-resistant than carbon steel casing in deepwater well environments, and its strength and pressure resistance are relatively high, but the price is higher.
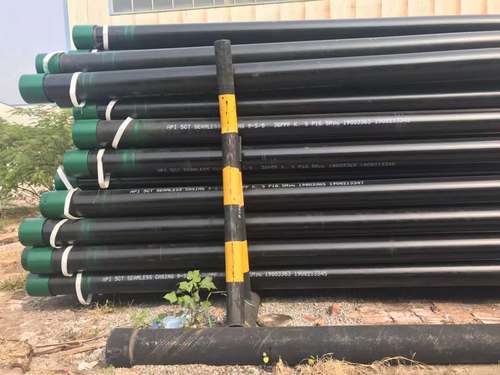
3.Titanium alloy casing
Titanium alloy refers to a variety of alloy metals made of titanium and other metals, which are widely used in deepwater wells. However, titanium alloy casings are expensive and are only suitable for areas with special requirements, such as ultra-deep wells.
Precautions for running water well casing
Casing running is a very important step in drilling. It can ensure the stability of the well wall and prevent the well wall from collapsing.
The following points need to be noted during the casing installation process.
1. First, the size and depth of the casing need to be determined, and the selection is based on factors such as well depth, formation conditions, and drilling purposes.
2. After determining the size and depth of the casing, the wellbore needs to be cleaned to ensure that the inside of the wellbore is clean to avoid obstruction when the casing sinks.
3. Next, casing needs to be run in. This process requires the use of a casing runner to run the casing into the wellbore section by section. During the running process, attention needs to be paid to controlling the speed of running the casing to avoid deformation or jamming of the casing caused by being too fast or too slow.
4. After the casing is lowered to the predetermined depth, cementing operation is required. Cement slurry is injected into the gap between the casing and the well wall to fix it in the well wall.
5. Finally, the casing needs to be sealed and inspected to ensure the quality and integrity of the casing and avoid water leakage problems.
Previous:Sheet pile shoring