Resistance welding is a method of applying pressure through electrodes after combining the workpieces, and using electric current through the contact surface of the joint and the resistance heat generated in the adjacent area to weld. Resistance welding is a method of using the resistance heating effect generated by the current flowing through the contact surface and adjacent areas of the workpiece to heat it to a molten or plastic state to form a metal bond. There are four main methods of resistance welding, namely spot welding, seam welding, projection welding and butt welding.
ERW steel pipe is a steel pipe welded by electric resistance welding process. It is used to transport gas and liquid objects such as oil and natural gas. It can meet various requirements of high and low pressure. At present, it occupies a pivotal position in the field of transportation pipes in the world.
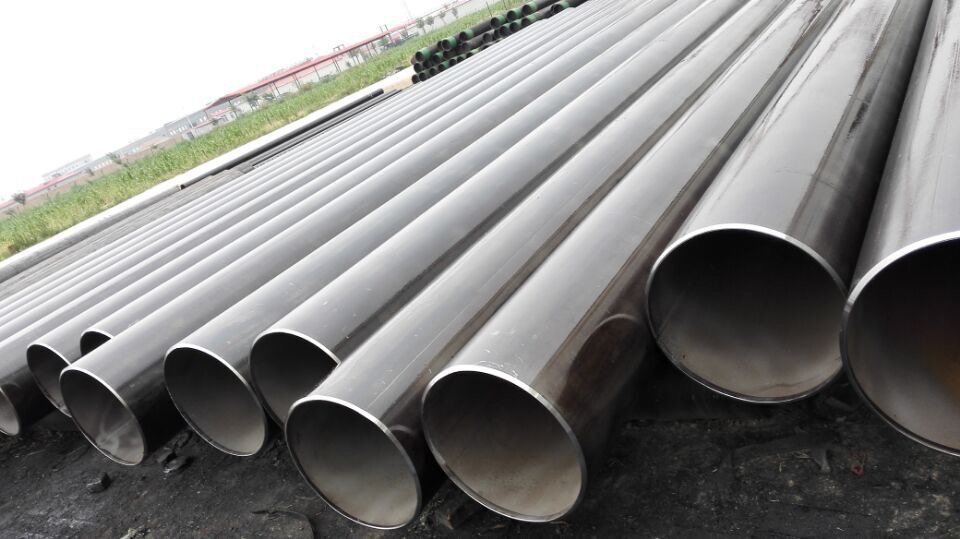
Advantages of the resistance welding process
1. When the nugget is formed, it is always surrounded by a plastic ring, the molten metal is isolated from the air, and the metallurgical process is simple.
2. The heating time is short and the heat is concentrated, so the heat affected zone is small, and the deformation and stress are also small. Usually, it is not necessary to arrange the calibration and heat treatment process after welding.
3. Filler metals such as welding wires and electrodes, and welding materials such as oxygen, acetylene, and hydrogen are not required, and the welding cost is low.
4. Simple operation, easy to realize mechanization and automation, and improve working conditions.
5. High productivity, no noise and no harmful gas. In mass production, it can be compiled into the assembly line together with other manufacturing processes. However, flash butt welding requires isolation due to sparks.
Disadvantages of the resistance welding process
1. At present, there is still a lack of reliable non-destructive testing methods. The welding quality can only be checked by destructive tests of process samples and workpieces, as well as by various monitoring techniques to ensure.
2. The lap joint of point and seam welding not only increases the weight of the component, but also forms an angle around the welding nugget of the two plates, resulting in low tensile strength and fatigue strength of the joint.
3. The power of the equipment is high, and the degree of mechanization and automation is high, which makes the equipment cost high and maintenance more difficult, and the commonly used high-power single-phase AC welding machine is not conducive to the balanced operation of the power grid.
ERW steel pipe is a steel pipe welded by electric resistance welding process. It is used to transport gas and liquid objects such as oil and natural gas. It can meet various requirements of high and low pressure. At present, it occupies a pivotal position in the field of transportation pipes in the world.
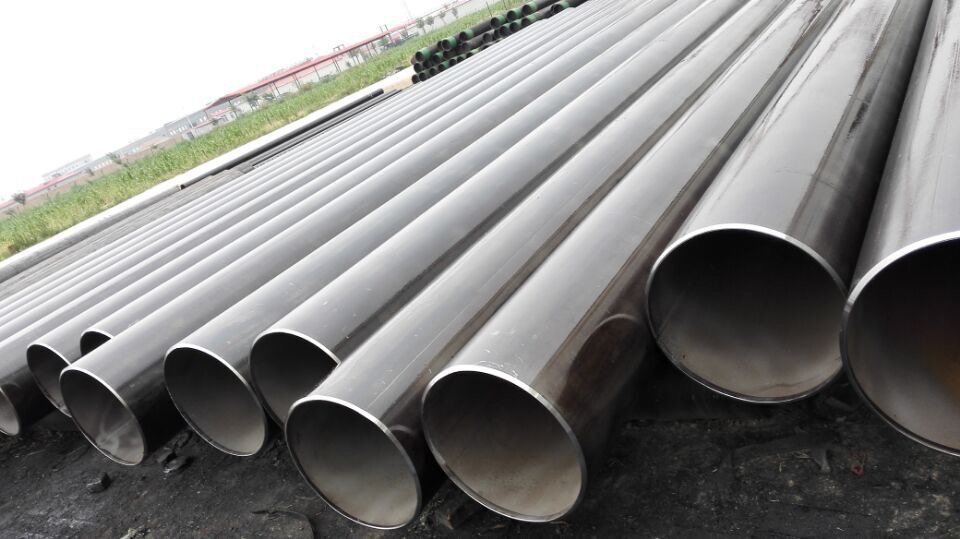
Advantages of the resistance welding process
1. When the nugget is formed, it is always surrounded by a plastic ring, the molten metal is isolated from the air, and the metallurgical process is simple.
2. The heating time is short and the heat is concentrated, so the heat affected zone is small, and the deformation and stress are also small. Usually, it is not necessary to arrange the calibration and heat treatment process after welding.
3. Filler metals such as welding wires and electrodes, and welding materials such as oxygen, acetylene, and hydrogen are not required, and the welding cost is low.
4. Simple operation, easy to realize mechanization and automation, and improve working conditions.
5. High productivity, no noise and no harmful gas. In mass production, it can be compiled into the assembly line together with other manufacturing processes. However, flash butt welding requires isolation due to sparks.
Disadvantages of the resistance welding process
1. At present, there is still a lack of reliable non-destructive testing methods. The welding quality can only be checked by destructive tests of process samples and workpieces, as well as by various monitoring techniques to ensure.
2. The lap joint of point and seam welding not only increases the weight of the component, but also forms an angle around the welding nugget of the two plates, resulting in low tensile strength and fatigue strength of the joint.
3. The power of the equipment is high, and the degree of mechanization and automation is high, which makes the equipment cost high and maintenance more difficult, and the commonly used high-power single-phase AC welding machine is not conducive to the balanced operation of the power grid.